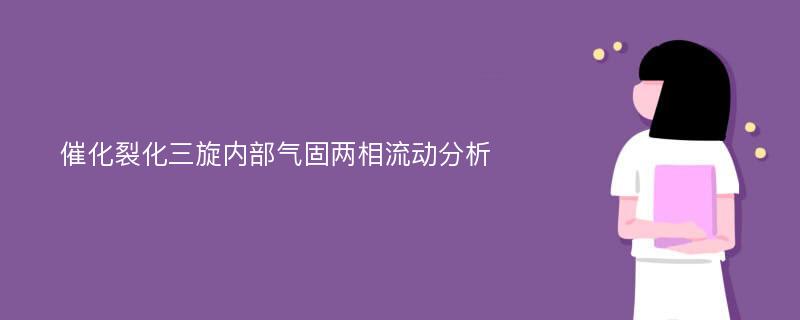
论文摘要
旋风分离器是利用含尘气体旋转时所产生的离心力将粉尘从气流中分离出一种干式气固分离设备。由于其具有结构简单、高效、能承受高温高压等优点,已经广泛应用于能源、化工、冶金、环保等众多领域。立置多管式三旋的核心部件是轴流导叶式旋风管,针对导叶式旋风管对于5 m的颗粒除尘效率较低的缺点,利用数值计算和实验为手段,结合理论解析方法,用发展中的现代多相流理论、湍流原理、计算流体动力学理论为指导,对其内部气固两相流动、分离机理和压力损失等性能特性进行深入分析。首先,为更好了解导叶式旋风管内部气相流动机理,利用理论解析方法和数值模拟方法对旋风管内部气相流场及压力场进行分析。其中,从柱坐标系下的Navier-Stokes方程和连续性方程出发,建立导叶式旋风管分离柱内旋风流场涡旋流动的精确解,采用无粘性流体假设,对于流场内部进行较为全面的求解。给出了径向速度、切向速度和轴向速度的表达式,以及压力梯度与静压的解析解。利用先进计算流体动力学(Computtational Fluid Dynamic, CFD)技术对于导叶式旋风管内部气相流动规律进行数值预测,采用雷诺应力模型(Reynold Stress Model, RSM)模拟气相流场,运用有限体积法和SIMPLEC(压力速度耦合算法)分析了旋风管内部流场和压力场分布。重点针对导向叶片内部流动进行分析,提出合理叶型准线设计方法。同时分析不同排气和排尘结构对于气相流场的影响,得到结构参数影响内部流动的一般规律。在流场分析基础上,从导叶式旋风管阻力沿程损失方式及组成出发,认为旋风管阻力可以分为进口阻力,本体内部损失,出口损失三部分,而旋风管本体阻力损失包括摩擦损失和涡流损失。在旋风管流场分析的基础上,构建了基于阻力复合原理的旋风管阻力模型,计算表明,进口损失约占15.7%,在分离空间旋转流场中阻力损失最大约为64.15%,而出口损失基本上属于纯能耗,占能量损失的19.79%,涡流损失为最主要的阻力损失,约为整体损失的40.88%。与试验结果相比,基本符合导叶式旋风管的阻力分布情况。其次,在气相流场模拟基础上,应用Euler-Lagrange气固两相流理论,气相流场采用雷诺应力模型,固相模型采用双相耦合的颗粒离散相模型计算颗粒轨迹,并采用单元内颗粒源法计算颗粒的浓度分布。得到不同入口位置对于颗粒运动轨迹的影响规律,以及旋风管内部不同粒径颗粒浓度分布特点,同时总结出计算导叶式旋风管分离效率和压力损失的数值计算方法,数值预测结果与实验结果较为吻合。然后,在流场分析基础上,通过引进旋风管颗粒浓度分布修正因子,充分考虑旋风管内部颗粒浓度分布呈现中间浓度较低,边壁浓度较高的特点,突破了传统意义上固相颗粒浓度径向混合均一的假设,提出转圈理论和边界层理论相结合的新型混合的旋风管性能理论计算方法。第三,利用数值模拟技术,研究不同操作参数下(诸如入口流量、温度、压力和底部灰斗抽气等)的导叶式旋风管内部气固两相流动特点,有利于进一步开发设计出高效低阻型导叶式旋风管,以及进一步发展全面的旋风管气固分离的机理模型。最后,对于多管组合旋风管进行全模型数值分析,研究不同进口结构参数对进气室内部气流均匀性的影响,提出在进口处设置多层扩散锥以提高气流分布均匀性的方法,并进行数值模拟验证。对于三旋装置不同流动空间来说,在进气室内单管入口流量不同,进气室内部压力分布并不均匀,其中各个入口附近出压力变化比较明显,且存在一定影响区域,一般小于进气室内部的平均压强,靠近入口区域的单管入口压降较大。而在公共灰斗内的窜流返混比较严重,可通过灰斗泄气有效抑制。
论文目录
摘要ABSTRACT创新点摘要表格目录插图目录第1章 绪论1.1 引言1.2 课题背景与意义1.3 旋风器及导叶式旋风管结构改进的研究现状和发展趋势1.3.1 进口型式研究现状1.3.2 排气结构研究现状1.3.3 排尘结构研究现状1.4 旋风器及导叶式旋风管气固两相流动数值模拟研究现状1.4.1 旋风分离器内气相流场数值模拟研究进展1.4.2 旋风分离器内气固两相流动数值模拟研究进展1.4.3 操作参数对旋风分离器气固两相流动数值模拟研究进展1.5 本文的研究的目的、方法和内容第2章 旋风管内气固两相流动数值模拟理论基础2.1 前言2.2 气相流场流动模型建立2.2.1 气相湍流控制方程组建立2.2.2 湍流计算模型2.2.3 控制方程的离散方法及离散格式的选择2.2.4 气相流场数值解法2.3 气固两相流动模型2.3.1 多相流动理论模型2.3.2 颗粒相随机轨道模型2.4 本章小结第3章 导叶式旋风管气相流动规律与压力分布3.1 引言3.2 旋风管内涡旋流动求解分析3.2.1 导叶式旋风管分离空间流场基本方程3.2.2 基本方程求解3.2.3 计算结果与讨论3.3 导叶式旋风管物理模型与计算方法3.3.1 旋风管物理模型3.3.2 湍流模型的确定3.3.3 边界条件与初始条件3.3.4 计算方法3.3.5 网格划分及网格无关性验证3.3.6 模拟结果的可靠性验证3.4 导叶式旋风管内部气相流场基本特征3.4.1 压力分布3.4.2 切向速度3.4.3 轴向速度3.4.4 径向速度3.4.5 湍流动能和湍流耗散分布3.4.6 导叶式旋风管内部流动矢量图3.4.7 分区间旋风管流场特征3.5 导叶式旋风管结构参数对气相流场影响分析3.5.1 导向器内部流动分析r)|-) 对旋风管流场影响'>3.5.2 排气管直径比((dr)|-) 对旋风管流场影响c)|-)对旋风管流场影响'>3.5.3 排尘锥直径比((dc)|-)对旋风管流场影响3.6 导叶式旋风管压降组成及阻力模型3.6.1 导叶式旋风管压降模型概述3.6.2 导叶式旋风管压力损失组成3.6.3 导叶式旋风管阻力模型3.6.4 结果分析与讨论3.6.5 排气管内流动减阻分析3.7 本章小结第4章 导叶式旋风管内部颗粒运动分析4.1 引言4.2 颗粒相运动模型与初始条件4.2.1 几何模型4.2.2 气体湍流模型和两相流模型4.3 颗粒运动轨迹数值模拟4.3.1 导向器内颗粒运动轨迹分析4.3.2 微粒(d=1.5 m)的运动轨迹4.3.3 细粒(d=4 m)的运动轨迹4.3.4 中粒(d=10 m)的运动轨迹4.4 旋风管内部颗粒浓度分布数值模拟4.4.1 旋风管颗粒浓度数值模拟初始条件4.4.2 颗粒浓度沿径向的分布4.4.3 颗粒浓度沿轴向的分布4.5 导叶式旋风管分离效率数值计算4.6 导叶式旋风管分离模型4.6.1 SHELL型导叶式旋风管流场参数总结4.6.2 旋风管内颗粒运动轨迹分析4.6.3 旋风管分离模型建立4.6.4 结果分析与讨论4.7 本章小结第5章 操作参数对旋风管气固两相流动影响5.1 引言5.2 入口流量对旋风管流场及性能影响分析5.3 温度和压力对旋风管流场影响分析5.3.1 温度对旋风管流场及性能影响分析5.3.2 温度对旋风管内颗粒浓度分布影响分析5.3.3 高温条件下压力对旋风管流场及性能影响分析5.3.4 温度和压力对旋风管性能综合考虑5.4 抽气率对旋风管流场影响分析5.4.1 灰斗抽气对导叶式旋风管流场和性能影响5.4.2 窜气对导叶式旋风管流场和性能影响5.5 本章小结第6章 多管组合三旋内部流动分析6.1 概述6.2 多管三旋进气室内流动分析6.2.1 物理模型及数值模型建立6.2.2 多管组合旋风管排气室内气流均匀性数值分析结果与讨论6.3 多管三旋内部基本流场计算与分析6.3.1 物理模型及计算模型分析6.3.2 多管三旋内部流动分析6.3.3 多管三旋“气流反窜”现象分析6.4 本章小结第7章 结论7.1 全文总结7.2 展望主要符号表参考文献攻读博士学位期间取得的研究成果致谢作者简介
相关论文文献
标签:催化裂化三旋论文; 导叶式旋风管论文; 结构优化论文; 计算流体动力学论文; 数值模拟论文; 阻力损失论文; 分离性能论文;