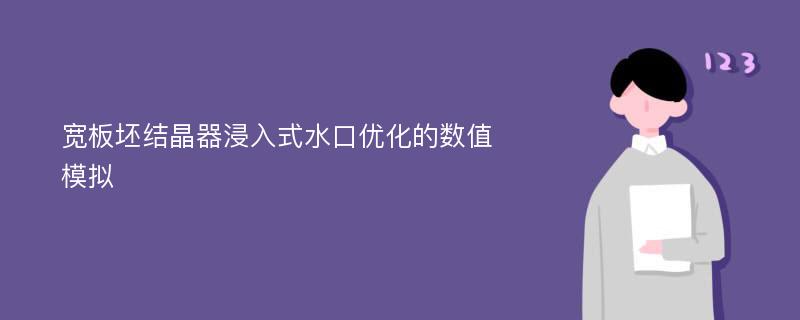
论文摘要
本文以宝钢220×(1350~2300)mm2、300×(1500mm~2300)mm2断面的宽板坯连铸结晶器为原型,基于商用软件FLUENT操作平台,采用连续性方程和动量方程以及能量方程建立数学模型,模拟研究了结晶器内钢水流动和传热行为,重点针对生产中存在的铸坯表面纵裂纹问题开展了结晶器浸入式水口结构参数的优化研究。研究结果表明:原有水口上循环弱,热交换慢,保护渣融化不均匀导致铸坯出现裂纹。针对原水口存在的问题,通过改变水口形状、中孔侧孔面积比及底部形状,设计了五种新水口方案,通过模拟择优选出了两个最适合现有工艺条件下浇注的浸入式水口。220mm厚结晶器使用扁形、侧孔倾角-15°、底部形状为凸底的水口;300mm厚结晶器使用圆形、侧孔倾角-15°、底部形状为平底的水口。采用新水口浇铸时,结晶器内钢液流动稳定,温度分布均匀,有利于改善宽板坯质量具有积极的作用。现场试验结果表明,使用优化的水口,液渣分布均匀,铸坯表面纵裂纹减少了30%以上,纵裂纹报废率为0,水口使用效果良好。
论文目录
摘要ABSTRACT1 绪论1.1 板坯连铸技术发展现状1.2 结晶器内钢液流动行为1.2.1 结晶器内钢液流动研究1.2.2 结晶器内钢液流场基本特征1.2.3 结晶器内钢液流动对铸坯质量的影响1.2.4 浸入式水口结构参数对结晶器流场的影响1.2.5 国内外研究现状1.3 课题研究目的、意义及主要内容1.3.1 研究的目的和意义1.3.2 研究的主要内容2 结晶器钢液流动模型建立与验证2.1 基本原理2.2 基本假设2.3 控制方程2.3.1 流体流动模型2.3.2 传热模型2.3.3 物质传输模型2.3.4 夹杂物运动轨迹模型2.4 边界条件设置2.4.1 水口入口处2.4.2 对称面和出口2.4.3 结晶器液面2.4.4 结晶器壁面#宽板坯连铸结晶器模型的建立'>2.5 宝钢3#宽板坯连铸结晶器模型的建立2.5.1 结晶器计算区域的建立2.5.2 板坯连铸结晶器流场的基本特征2.5.3 水力学模型对数学模型的验证2.6 本章小结3 结晶器内钢液流动的数值模拟研究3.1 现场调研目的和内容3.1.1 调研目的3.1.2 调研内容3.2 现用水口的评价3.2.1 200mm 厚结晶器不同断面流场模拟3.2.2 220mm 不同断面温度场模拟3.2.3 液面附近温度速度分析3.2.4 300mm 不同断面流场模拟3.2.5 300mm 不同断面温度场模拟3.2.6 液面温度和速度分析3.3 待用水口的评价3.3.1 不同断面流场模拟3.3.2 不同断面温度场模拟3.4 新水口的设计3.4.1 220mm 断面新水口数值模拟3.4.2 300mm 断面新水口数值模拟3.5 最优水口与原用水口的比较3.5.1 220mm 厚断面的比较2 断面的比较'>3.5.2 300×2300mm2断面的比较3.5.3 夹杂物的模拟3.6 本章小结4 结晶器水口优化前后工艺跟踪及效果分析4.1 优化水口试验结果分析4.2 220mm 厚度结晶器优化水口实验结果分析 4.2.1 液渣分布情况分析4.2.1 液渣分布情况分析4.2.2 铸坯质量检测结果分析4.3 300mm 厚度结晶器优化水口实验结果分析4.3.1 液渣分布情况分析4.3.2 铸坯质量检测结果分析4.4 小结5 结论致谢参考文献附录 攻读硕士期间发表的论文
相关论文文献
标签:宽板坯论文; 结晶器论文; 流场论文; 温度场论文; 浸入式水口论文; 数值模拟论文;