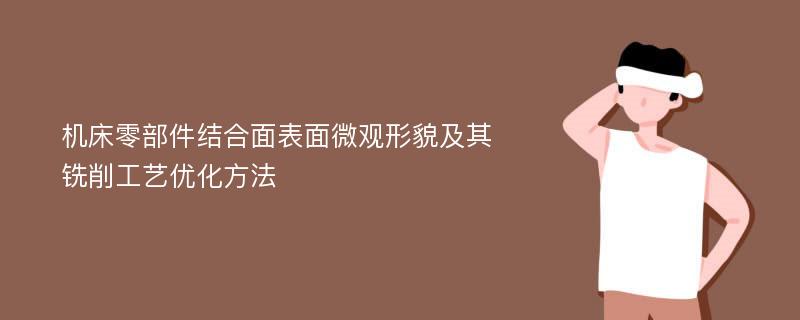
论文摘要
随着机床制造行业的不断发展,对设计制造具有特定性能及高表面质量的机床零部件需求越来越大,这对零部件表面的加工提出了新的要求。在此情况下,研究基于结合面性能要求的机床零部件加工工艺优化方法对提高我国机床制造企业的竞争力有着极大的现实意义。本文在科技重大专项课题“水室封头车铣加工中心重要零部件加工工艺技术研究(2011ZX04002-111)”的支持下,在齐齐哈尔二机床(集团)已有加工工艺的基础上,分析机床结合面表面微观形貌对结合面性能的影响,提出了基于结合面性能要求的机床结合面铣削工艺优化方法,主要内容如下:针对机床及零部件结合面的结构、性能进行分析,得到结合面性能对机床性能的影响程度;建立了机床结合面表面微观形貌评价指标体系;通过结合面性能与表面微观结构关系模型,获得表面微观形貌参数对结合面性能的影响规律。以机床结合面表面微观形貌为对象,建立包括刀具安装误差、刀具磨损、切削振动及刀具变形等影响因素的面铣刀切削加工表面微观形貌模型;对表面微观形貌进行仿真分析,获得了各影响因素对表面微观形貌形成的影响规律。对面铣刀切削加工实验结果进行分析,获得了切削过程中各切削参数对面铣刀切削加工特征变量的影响程度及规律,并通过运用灰色系统理论得到了刀具磨损、切削振动、切削力、微观形貌参数及加工效率等切削加工特征变量之间的交互作用。对面铣刀切削加工优化目标及其影响因素进行层次分析,获得了优化目标与影响因素的层次结构关系,并在此结果的基础上建立了面铣刀切削加工动、静结合面表面加工工艺优化设计方法,最后通过机床结合面表面加工对比验证了该方法的有效性。
论文目录
摘要Abstract第1章 绪论1.1 课题研究的目的与意义1.2 国内外研究现状1.3 机床零件加工存在问题1.4 论文主要研究内容第2章 机床结合面性能及结构分析2.1 机床性能分析及结合面结构描述2.1.1 机床性能分解2.1.2 结合面类型及其性能2.1.3 结合面性能与机床性能相关性2.2 2机床结合面表面微观形貌评价指标2.2.1 表面微观结表征2.2.2 表面微观形貌与误差分布关系分析2.2.3 表面微观形貌与依附曲面变形关系分析2.3 机床静结合面性能与表面结构关系2.4 机床动结合面性能与表面结构关系2.5 本章小结第3章 机床结合面表面微观形貌形成分析3.1 面铣刀切削运动轨迹模型3.2 机床结合面表面微观形貌仿真模型3.2.1 刀片安装误差对刀工接触关系影响3.2.2 刀片磨损对刀工接触关系影响3.2.3 刀具振动对刀工接触关系模型影响3.2.4 刀具变形对刀工接触关系影响3.2.5 表面微观形貌模型及仿真结果3.3 刀具安装误差及切削参数对表面形貌影响仿真3.4 切削特征变量对表面微观形貌影响仿真3.4.1 考虑刀片磨损影响的表面微观形貌仿真3.4.2 考虑刀具振动影响的表面微观形貌仿真3.4.3 考虑刀具变形影响的表面微观形貌仿真3.5 本章小结第4章 面铣刀切削结合面实验研究4.1 实验条件4.2 切削特征变量实验结果及分析4.2.1 加工表面微观形貌参数极差分析4.2.2 面铣刀切削力极差分析4.2.3 面铣刀切削振动极差分析4.2.4 面铣刀刀具磨损极差分析4.3 切削特征变量影响显著性分析4.4 本章小结第5章 机床结合面表面微观形貌加工工艺优化5.1 铣削加工工艺层次结构要素分析5.2 机床结合面加工表面优化模型5.2.1 面铣刀切削加工效率模型5.2.2 面铣刀切削加工质量模型5.2.3 面铣刀切削加工表面微观形貌模型5.2.4 面铣刀切削加工影响因素模型5.3 机床结合面表面加工工艺优化及实验验证5.3.1 机床静结合面工艺优化方法5.3.2 机床动结合面工艺优化方法5.3.3 结合面工艺参数优化验证5.4 本章小结结论参考文献攻读学位期间发表的学术论文致谢
相关论文文献
标签:机床零部件论文; 结合面论文; 表面微观形貌论文; 铣削工艺论文;