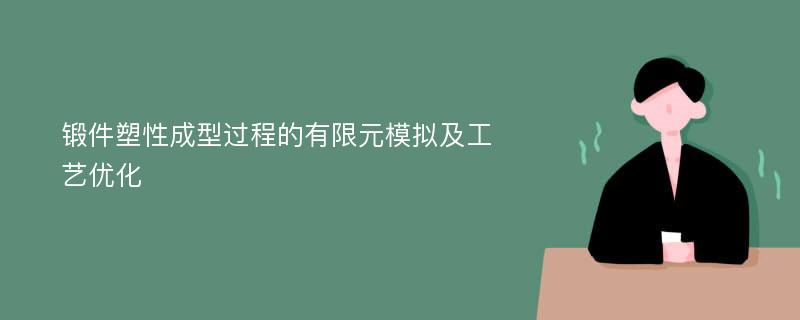
论文摘要
金属塑性成型是一个极其复杂的过程,不仅塑性变形量大,而且成型过程和产品质量受材料性能、摩擦状况、工艺条件、模具结构和加工设备的共同影响。长期以来主要是采用基于经验的试错方法进行工艺及模具设计,这使得新产品和新工艺开发试制周期较长、材料消耗大、费用高,产品的质量也往往不能完全保证,而以有限元为代表的数值模拟方法是对金属成形工艺进行科学预测、工艺优化和定量控制的有效方法。采用DEFORM软件作为模拟分析的工具,基于刚塑性有限元理论,建立了具有典型特点的三类零件固定支座,导向套,支架成型的有限元模型,论文完成了以下几项工作:1)结合锻压生产的工艺特点,阐述了利用有限元模拟来分析三类零件锻压过程的必要性,可行性和优越性。2)根据三类零件的塑性变形特点,进行了适当的假设和简化,选用刚塑性有限元法,为其建立合理的理论模型,选择适宜的求解方法,力求使模拟条件接近实际生产条件。3)对成形过程的数值模拟结果进行了详细的分析,得到了金属流动的速度场、变形力随时间的变化情况、锻件内等效应力场、等效应变场的分布及锻件温度对成型的影响等,揭示了金属的流动变形规律,并用模拟结果来指导和优化工艺,以改善锻件的成形填充过程。4)研究了固定支座的成形机理,分析了该零件锻压成型过程中典型缺陷产生的原因,并提出了相应的解决方法。文中利用缺陷产生处的节点的速度分析对“缺肉”进行了解释,材料本身的塑性属性、摩擦、模具结构以及表面状况等对产生“缺肉”起着重要的影响,通过反复修改参数模拟,给出了解决缺陷问题的措施。锻压成型质量受很多因素影响,对几个典型影响因素进行了分析与优化,为改进和优化锻压工艺提供了理论指导。
论文目录
摘要Abstract引言1 文献综述1.1 课题研究背景1.1.1 金属塑性加工1.1.2 塑性加工的基本环节1.1.3 塑性加工研究的目标和任务1.1.4 锻件塑性加工过程有限元数值模拟的意义1.2 基于有限元分析的锻造工艺优化设计技术的研究现状1.2.1 有限元法的发展应用1.2.2 锻压工艺有限元法分析的发展及现状1.3 锻造过程有限元分析存在的问题及发展趋势1.3.1 锻造过程有限元分析存在的问题1.3.2 锻造有限元分析技术的发展趋势1.4 研究内容和目标1.4.1 课题的研究内容1.4.2 研究目标及实施路线2 金属塑性变形基础及有限元技术2.1 金属塑性变形基础2.1.1 塑性及塑性指标2.1.2 影响金属塑性和变形抗力的主要因素2.1.3 成型缺陷的产生机理及原因2.2 有限元模拟技术2.2.1 有限元法的基本原理2.2.2 有限元法的分析步骤2.2.3 刚塑性有限元法的基本原理2.3 DEFORM 模拟软件2.3.1 DEFORM 软件简介2.3.2 DEFORM 的特点3 锻压过程有限元分析模型的建立3.1 金属塑性加工模拟过程3.1.1 建立几何模型3.1.2 单元网格的划分3.1.3 材料参数的定义3.1.4 迭代准则及边界条件3.1.5 摩擦力计算模型3.1.6 缺陷预测3.2 DEFORM 软件有限元模型的建立步骤3.2.1 建立坯料和模具的几何模型3.2.2 设置模拟名称、类型3.2.3 输入工件及工件数据3.2.4 输入模具3.2.5 工件和模具的定位3.2.6 设置物体温度3.2.7 设置模具的移动3.2.8 模拟控制设定3.2.9 对象间关系设定3.2.10 生成数据库文件4 固定支座的有限元模拟4.1 模拟条件及参数设置4.2 模拟结果及分析4.2.1 固定支座的成型过程4.2.2 等效应力分析4.2.3 破坏系数分析4.2.4 成型载荷分析4.2.5 变形过程中材料流动速度的分析4.2.6 温度变化对成型影响的分析4.2.7 缺陷分析4.2.8 坯料对锻造变形力的影响4.3 本节小结5 导向套的有限元模拟5.1 模拟条件及参数设置5.1.1 导向套锻件和锻模三维造型5.1.2 导向套的模拟条件及参数设置5.2 模拟结果及分析5.2.1 模拟的变形过程5.2.2 网格划分对模拟的影响5.2.3 变形速度对锻压力的影响5.2.4 模具圆角半径对充型和锻件质量的影响5.2.5 温度对锻件质量的影响5.2.6 变形条件优化后的成型模拟结果5.3 本节小结6 支架的有限元模拟6.1 模拟条件及参数设置6.2 模拟结果及分析6.3 本节小结结论参考文献致谢导师简介作者简介学位论文数据集
相关论文文献
标签:有限元论文; 模锻论文; 数值模拟论文;