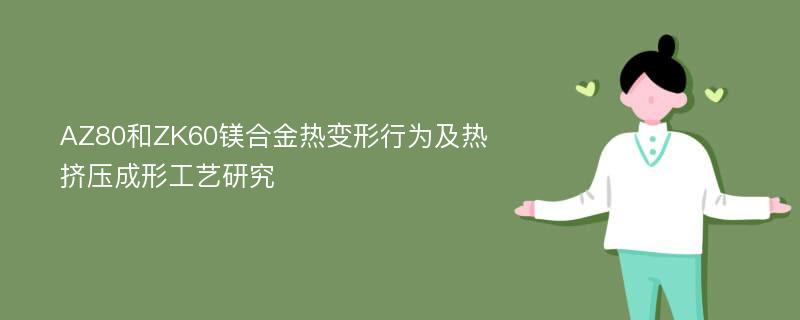
论文摘要
随着制作大型结构件、结构多样化和轻量化的要求,变形镁合金在未来交通、航空航天、家电等领域都将起着无可替代的作用。然而,变形镁合金塑性成形技术研究的相对迟缓,大大限制了变形镁合金的广泛应用。因此,深入研究变形镁合金的变形行为、成形性能及塑性成形技术对于突破现阶段变形镁合金产品类别少、应用范围窄的局限,使变形镁合金作为理想的轻质材料在更多更广阔的领域得到应用有着相当重要的理论和应用意义。本文的目的是通过对连铸AZ80镁合金和挤压态ZK60镁合金在不同变形条件下的热压缩行为、微观组织演变、成形性能及热加工图的研究,在建立本构模型和动态再结晶演化模型的基础上,对镁合金典型挤压零件(多层壳体和管件)热成形过程和内部组织演变进行数值模拟。同时利用自己设计的模具进行实际成形研究,探索在复杂成形过程中镁合金的流动规律和组织演变规律,确定使镁合金获得良好变形性能的工艺条件,进而对镁合金进行固溶及时效处理来提高其使用性能,从而为镁合金塑性成形技术的发展和应用提供可靠的依据。为此,本文着重进行以下几个方面的研究:采用连铸AZ80镁合金和挤压态ZK60镁合金,在240~440℃温度范围内和0.001~1s-1的应变速率条件下,通过单向热压缩实验研究变形镁合金在高温下的塑性变形行为,并对其结果进行了设备误差修正、摩擦影响修正和温度修正,得到了AZ80和ZK60镁合金精确的应力一应变曲线,建立本构模型、动态再结晶演化模型及等温条件下的晶粒长大模型,为数值模拟计算和预测流变应力及微观组织提供了有效的计算方法和数学模型依据。通过对建立的AZ80和ZK60镁合金在温度为240℃~440℃、应变速率为0.001~1s-1、应变分别为0.1~0.6条件下热加工图的研究表明:AZ80镁合金绝大部分为可加工区,塑性流动失稳区域随变形量的不同而发生改变,塑性失稳区大都在高应变低温区和高温区域;ZK60镁合金具有良好加工性能的区间在280~420℃及应变速率0.003~0.2s-1的范围内。采用数值模拟和物理模拟相结合,对不同凹模型面对挤压过程的影响进行了研究。结果表明,半模角α在60。-70。时,管材成形所需挤压力较小且有利于金属流动。锥模的挤压力较小且材料利用率较高,适用于实际生产。当锥模半模角为70。时,.管材成形所需挤压力最小。采用有限元数值模拟的方法分析和预测AZ80镁合金多层壳体零件及ZK60镁合金管件热挤压成形过程中工艺参数对成形力及微观组织的影响规律。研究表明:挤压力与挤压速度、挤压比及摩擦系数成正比,而与坯料温度成反比;变形温度升高,晶粒长大;速度增加,晶粒细化;变形程度越大,再结晶晶粒就越细小。在设备允许的情况下,为了获得细小均匀的组织,应选择较高的挤压速度和挤压比,较低的坯料温度。通过模拟优化,分析多层壳体件及管件的结构形状特点,计算成形力,并设计制造适合AZ80镁合金多层壳体件反挤压成形和ZK60镁合金管件热挤压成形的实验装置并进行实验研究。对于AZ80镁合金多层壳体件反挤压成形研究结果表明:坯料直径在φ75mmm左右成形性较好,当直径大于φ88mm,易使挤压力过大,造成掉底,当直径小于φ65mm,不容易对中,造成偏心;在模具温度为一定(大于290℃)时,坯料需要加热到350℃以上,才能得到外观较好的零件,挤压后零件晶粒明显细化,随坯料温度的升高,力学性能呈现先降低后升高的规律;当坯料温度一定时,成形零件随模具温度逐渐升高,零件的成形性、力学性能逐渐升高。对于AZ80镁合金多层壳体件反挤压成形,模具温度320-350℃,坯料温度350-410℃范围内所挤压成形的零件综合性能较好。ZK60镁合金管件热挤压成形研究结果表明:对lmm/s、1.5mm/s、2mm/s三个速度进行管材挤压实验和金相组织分析,可得出,增大挤压速度有利于管材件的晶粒细化,但同时挤压力也会变大,因此,1.5mm/s为合理的挤压速度;在270-390℃温度范围内进行实验,随温度的升高,挤压力减小而晶粒尺寸增大;从挤压力和晶粒尺寸两方面考虑,坯料温度在300-360℃时的等温挤压适合管材成形;当T坏=330℃,T模=300℃时,晶粒尺寸细小且组织均匀,挤压力也比较合理,最利于管材挤压成形。考察AZ80镁合金热成形后进行固溶及时效处理工艺的组织性能,结果表明:经固溶处理后,随固溶温度的提高,位于晶界处的粗大、硬脆第二相β-Mg17Al12弥散均匀于基体中,第二相的溶解导致镁合金内强化相的减少或消失,因而合金塑性得到提高,而强度下降;随时效时间的延长,β-Mg17Al12相的数量逐渐增加,且连续析出相的比例逐渐增多,导致合金的抗拉强度逐渐升高,而合金的延伸率明显降低;AZ80镁合金固溶处理后,断口形貌为具有一定塑性变形的准解理特征;时效处理后合金的拉伸断口形貌呈现以解理为主的脆性断裂特征,断裂主要发生在结合较薄弱的晶界及β-Mg17Al12相析出相的片层间。
论文目录
摘要Abstract第1章 绪论1.1 镁及变形镁合金的应用1.1.1 金属镁的特点1.1.2 金属镁的发展1.1.3 镁合金特性1.1.4 变形镁合金的应用1.2 镁合金加工技术1.2.1 镁合金铸造成形技术1.2.2 镁合金塑性成形技术1.2.3 镁合金焊接成形技术1.3 镁合金塑性变形行为研究概论1.3.1 镁及镁合金塑性变形机制1.3.2 镁合金塑性变形行为研究方法1.3.3 镁合金塑性变形行为研究进展1.3.4 镁合金动态再结晶的研究1.4 热加工图在镁合金热变形中的应用1.5 铁合金挤压成形技术应用概况1.6 有限元技术镁合金塑性成形中的应用1.7 选题意义及研究内容1.7.1 本论文研究意义1.7.2 本论文研究内容第2章 变形镁合金热加工工艺基础研究2.1 实验材料与方法2.1.1 实验材料2.1.2 实验方法与设备2.1.3 组织观察2.2 热压缩试验结果及修正2.2.1 应变速率的设备误差2.2.2 AZ80及ZK60合金载荷—应变曲线2.2.3 摩擦系数的影响及修正2.2.4 温度变化的修正2.2.5 修正后的真应力—真应变曲线2.3 AZ80和ZK60合金本构关系模型2.3.1 金属塑性变形本构方程概述2.3.2 AZ80和ZK60合金本构方程2.3.3 本构方程的验证2.4 AZ80和ZK60合金热加工图2.4.1 热加工图理论2.4.2 AZ80镁合金热加工图的建立和分析2.4.3 ZK60镁合金热加工图的建立和分析2.5 AZ80镁合金热变形过程组织演变2.5.1 AZ80镁合金热变形组织2.5.2 AZ80镁合金热变形动态再结晶演化模型2.6 AZ80镁合金等温过程中晶粒长大数学模型2.6.1 实验研究2.6.2 模型中相关参数的确定2.6.3 模型验证2.7 ZK60镁合金热变形过程组织演变2.7.1 ZK60镁合金热变形组织2.7.2 ZK60镁合金热变形动态再结晶演化模型2.8 本章小结第3章 镁合金成形件挤压工艺分析及模具研制3.1 AZ80镁合金多层壳体零件成形工艺及模具设计3.1.1 多层壳体零件结构特点及成形方式分析3.1.2 多层壳体零件成形力的计算3.1.3 多层壳体零件挤压模具的研制3.2 ZK60镁合金管材成形工艺及模具设计3.2.1 ZK60镁合金管材成形方式分析3.2.2 镁合金管材挤压成形力的计算3.2.3 镁合金管材挤压最佳凹模型面研究3.3 本章小结第4章 镁合金多层壳体及管件热挤压成形数值模拟研究4.1 弹塑性有限元法及MSC.Marc有限元软件4.1.1 弹塑性有限元法简介4.1.2 MSC.Marc有限元软件4.2 镁合金材料库的建立4.3 AZ80镁合金多层壳体反挤压成形过程有限元分析4.3.1 有限元模型建立4.3.2 壳体反挤压模拟过程分析4.3.3 工艺参数对壳体挤压力的影响4.4 AZ80镁合金多层壳体热挤压的组织演变预测4.4.1 热挤压过程组织演变二次开发4.4.2 热挤压过程中晶粒尺寸变化4.4.3 热挤压过程中再结晶体积分数分布规律4.4.4 工艺参数对晶粒尺寸的影响4.5 ZK60镁合金管件正挤压成形数值模拟4.5.1 有限元模型建立4.5.2 管件正挤压模拟过程分析4.5.3 工艺参数对管件挤压力的影响4.6 ZK60镁合金管件热挤压的组织演变规律4.6.1 管件热挤压中晶粒尺寸变化4.6.2 热挤压过程中再结晶体积分数分布规律4.6.3 热挤压过程残余应变的分布规律4.6.4 工艺参数对晶粒尺寸的影响4.7 本章小结第5章 AZ80镁合金多层杯件热反挤压工艺研究5.1 多层杯件热反挤压工艺研究实验内容及方案5.1.1 多层壳体热反挤压实验5.1.2 拉伸实验5.1.3 金相实验5.1.4 断口扫描实验5.2 多层杯件热反挤压成形质量分析5.2.1 压盖筒壁高度偏差5.2.2 挤压制件的缩口和扩口5.2.3 挤压制件外表面的裂纹5.3 坯料直径对挤压的影响5.4 坯料温度对反挤压成形的影响5.4.1 坯料温度对零件的表面质量的影响5.4.2 坯料温度对零件的显微组织的影响5.4.3 坯料温度对零件的力学性能的影响5.4.4 不同坯料温度下成形零件的断口形貌及分析5.5 模具温度对零件性能的影响5.5.1 模具温度对零件的表面质量的影响5.5.2 模具温度对零件的显微组织的影响5.5.3 模具温度对零件的力学性能的影响5.5.4 不同模具温度下成形零件的断口形貌及分析5.6 固溶处理对AZ80镁合金挤压件组织及力学性能影响5.6.1 AZ80镁合金固溶处理5.6.2 不同挤压参数对AZ80镁合金固溶处理的影响5.6.3 固溶处理对AZ80镁合金力学性能的影响5.6.4 AZ80镁合金固溶态拉伸断口形貌分析5.7 时效处理对AZ80镁合金挤压件组织及力学性能影响5.7.1 AZ80镁合金时效处理5.7.2 时效处理对AZ80镁合金组织的影响5.7.3 时效处理对AZ80镁合金力学性能的影响5.7.4 时效后拉伸断口形貌分析5.8 本章小结第6章 ZK60镁合金管件热正挤压工艺研究6.1 管件热挤压工艺研究实验方案6.1.1 管件热挤压实验6.1.2 其它实验6.2 管件热挤压成形质量分析6.2.1 挤压管件的裂纹6.2.2 挤压管件的弯曲6.3 挤压凹模半模角对挤压力的影响6.4 挤压比对管件挤压成形的影响6.4.1 挤压比对挤压力的影响6.4.2 挤压比对管件显微组织的影响6.4.3 挤压比对管件力学性能的影响6.5 挤压速度对管件挤压成形的影响6.5.1 挤压速度对挤压力的影响6.5.2 挤压速度对管件显微组织的影响6.5.3 挤压速度对管件力学性能的影响6.6 坯料温度对管件挤压成形的影响6.6.1 坯料温度对挤压力的影响6.6.2 坯料温度对管件显微组织的影响6.6.3 坯料温度对管件力学性能的影响6.7 断口扫描实验结果与分析6.8 本章小结第7章 结论参考文献致谢攻读博士学位期间发表论文作者简介
相关论文文献
标签:变形镁合金论文; 热变形行为论文; 本构模型论文; 热加工图论文; 微观组织演变论文; 数值模拟论文; 挤压论文; 固溶论文; 时效论文;
AZ80和ZK60镁合金热变形行为及热挤压成形工艺研究
下载Doc文档