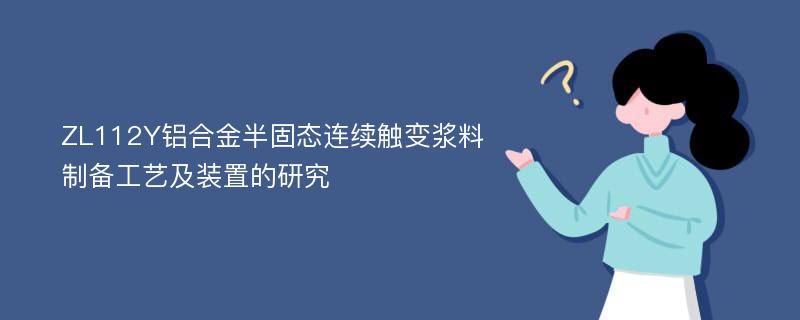
论文摘要
本论文是研究ZL112Y 铝合金的半固态连续触变成形料坯制备工艺,设计一套合适的半固态连续触变重熔装置,以及找到一套合理的连续触变重熔工艺的工艺参数。根据半固态连续触变成形的原理,自行设计了一套实验装置。装置主要包括原始坯料的制备装置以及二次重熔装置。原始坯料是采用低过热法制备,因此坯料制备装置包括熔炼铝合金的电阻炉以及浇注料坯的金属模具。坯料的二次重熔选用感应加热方式,因此二次重熔装置包括用以二次加热的三台感应加热设备及与之匹配的感应线圈、重熔用坩埚、支撑坩埚用的支架以及控制半固态浆料出料的底座。在实验过程中不断的进行了实验装置的改进,包括坩埚的加固、坩埚材料的重新选择以及底座结构的改进。装置设计完后,进行了装置的可行性性验证。经实验证明:1)支架的结构合理,能够实现对感应加热设备及坩埚有序的组装,满足连续式生产的要求;2)感应线圈稳定性好,与感应加热设备能很好的匹配,发挥感应加热设备较大的加热功率;3)控制半固态浆料出料的端座的结构比较合理,能够有效的操控半固态浆料的流出,在端座中采用升热装置后,浆料在流出过程不会发生凝固现象而保持半固态状态。4)整套装置的关键问题在于重熔用的坩锅的选用,经过实验证明,选用的几种坩埚的强度均达不到实验的要求,在高温下出现了裂纹而发生铝液的泄漏,因此坩埚问题还有待改进。为找到一套合理的连续重熔工艺,采用了ANSYS 数值模拟软件进行了坯料在连续触变重熔过程中的温度场分布的模拟。在进行连续触变重熔的模拟前,为了验证模拟的正确性,进行了对原有的最大振荡功率加热、缓慢加热、以及采用优化工艺加热实验的模拟。通过模拟结果与实测结果的对比,证明模拟能够正确的反映坯料在实际加热过程中温度变化的规律,而且模拟得到的坯料温度数据与实测数据基本吻合,误差不大。在进行了细微的材料物理参数修正以及感应加热模型的改进后,进行了半固态连续触变重熔的模拟。通过对在三台感应加热设备不同加热功率匹配下的模拟,找到了坯料由室温加热到半固态过程中各台感应加热设备合理的加热功率以及加热时间。大、中、小功率三台设备的振荡电流值分别为:1350A、800A、600A,加热时间总共为9 分钟,各台感应加热设备的加热时
论文目录
中文摘要英文摘要1 绪论1.1 选题背景1.2 半固态加工技术概述1.2.1 半固态成形工艺的特点1.2.2 半固态金属加工的工艺过程1.2.3 半固态金属浆料的制备工艺1.2.4 半固态坯料的二次加热工艺1.2.5 铝合金半固态成形零件的特点1.2.6 铝合金半固态成形国内外现状综述1.3 本论文的工作1.3.1 本研究的目的1.3.2 本研究的具体内容2 实验装置的设计2.1 原始料坯的制备2.1.1 料坯材料的选择2.1.2 半固态原始坯料的制备2.2 半固态连续触变重熔实验装置的设计2.2.1 试验装置总装图的设计2.2.2 装置支架的设计2.2.3 加热设备的选取2.2.4 感应线圈的设计与制作2.2.5 底座的设计2.2.6 坩埚材料的选择2.2.7 测温系统的设计2.3 装置其它部分的设计2.3.1 线圈与坩埚的间隙2.3.2 线圈与线圈之间的间隙2.3.3 坩埚与底座之间的固定2.3.4 抽杆的设计2.4 实验装置可行性验证2.4.1 刚玉坩埚中熔化棒料2.4.2 石英砂加固后的刚玉坩埚中熔化棒料2.4.3 红泥加固后的刚玉坩埚中熔化棒料2.4.4 耐火水泥加固后的刚玉坩埚中熔化棒料2.4.5 高铝坩埚中熔化棒料2.5 半固态连续触变重熔装置的讨论3 ANSYS 有限元数值模拟3.1 ANSYS 有限元数值模拟在实验中的运用3.2 数值模拟技术在半固态成形工艺中的应用3.3 ANSYS 数值模拟3.4 感应加热有限元分析理论3.4.1 感应加热原理3.4.2 感应加热坯料温度分布计算3.5 有限元模拟过程3.5.1 模型的生成3.5.2 几何实体模型的建立3.5.3 有限元模型的生成3.5.4 材料物理参数3.5.5 创建物理环境、施加边界条件及载荷进行求解3.6 有限元求解结果与实验结果的比较3.6.1 最大振荡功率时的感应加热模拟3.6.2 缓慢加热时的感应加热模拟3.6.3 优化工艺加热时的感应加热模拟3.7 模拟结果的精度分析3.8 坯料连续触变重熔的温度场模拟3.8.1 4 种不同加热工艺下连续触变重熔的温度场模拟结果3.8.2 ANSYS 数值模拟结论4 结论致谢参考文献附录:作者在攻读硕士学位期间发表的论文独创性声明学位论文版权使用授权书
相关论文文献
标签:连续触变成形论文; 二次重熔工艺论文; 触变重熔装置论文; 数值模拟论文; 铝合金论文;
ZL112Y铝合金半固态连续触变浆料制备工艺及装置的研究
下载Doc文档