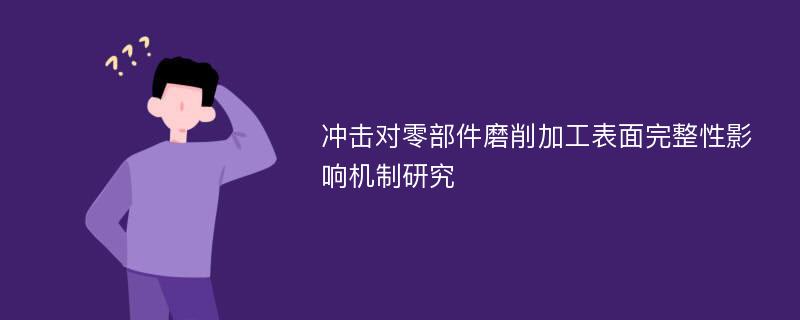
论文摘要
磨削过程中磨粒对工件的冲击强化是指砂轮在对工件磨削的过程中,由于砂轮的高速旋转而使得砂粒对工件材料进行反复不断的冲击,这样的冲击使得工件表面金属的硬度等性质发生改变,对零件表面完整性造成影响,主要就是体现在表面强化作用上。本文研究了磨削的机理,对磨削的过程、磨削的特点、磨削过程中砂轮的有效刃数、接触弧长、未变形切削厚度、磨削力等进行了分析和计算,并对磨削过程中磨粒冲击的特性进行了分析,从数量级上分析计算了普通磨削和高速超高速磨削的磨粒接触时间和材料的应变率。分析了磨削过程中磨粒的冲击对零件表面完整性的影响机制,主要是针对表面加工硬化这一方面来展开讨论的,同时对冲击对零件表面残余应力的影响和表面粗糙度的影响也做了阐述。磨粒冲击造成的硬化现象经过分析讨论主要是磨粒在冲击零件表面的时候由于冲击力的作用,零件表面有很大的应变率,零件表面位错的密度会迅速变大,宏观现象就是材料的硬度变硬。工件表面会随着冲击压力的增大而变硬,当冲击硬化达到一定的饱和状态时,则随着压力的增加,材料表面的硬化现象将减小。原因是冲击形成的热会在结构中形成材料的再生和再结晶,从而减小冲击生成的缺陷效应。以理论为基础,用DEFORM-3D软件对基于单颗磨粒平面磨削冲击过程对45钢进行了有限元仿真,获得了磨削力的变化规律及工件内部的应力场的分布情况,对磨削过程中零件表面应变和应变率的进行了分析对比,提出磨削参数对磨削过程的影响。磨削过程中材料受力曲线体现出磨削力的加载和卸载过程,对等效应力的分析说明磨削过程中工件受力其实是很多的脉冲力合成的,磨削过程其实就是冲击过程。应变率曲线体现出冲击这一现象。仿真分析和理论分析互相验证彼此的正确性。最后对磨削表面强化层厚度和磨削表面硬度做测量,一方面验证了仿真的准确性,另一方面说明磨削过程中磨粒的冲击作用确实存在,但是在常规磨削中冲击作用要弱于淬火作用。
论文目录
摘要Abstract第1章 绪论1.1 课题研究背景1.2 磨削表面冲击强化1.2.1 高速超高速磨削1.2.2 磨削强化层金相组织1.2.3 磨削表面冲击强化技术1.2.4 磨削强化层残余应力1.3 本课题研究的主要内容第2章 磨削过程的理论分析2.1 磨削过程2.1.1 磨削的物理模型2.1.2 磨削过程的三个阶段2.1.3 冲击作用2.2 磨削特点2.3 砂轮的有效刃数2.3.1 静态有效磨刃数d'>2.3.2 动态有效磨削刃数Ndmom'>2.3.3 瞬时有效磨刃数Nmom2.3.4 影响有效磨刃数的因素2.4 接触弧长和接触长度c'>2.4.1 几何接触弧长lck'>2.4.2 运动接触长度lk2.5 切削厚度2.5.1 未变形切削厚度对磨削的影响2.5.2 切削厚度计算2.6 磨削力模型2.6.1 磨削力的理论公式2.6.2 磨削力经验公式2.7 磨削过程冲击特性分析2.7.1 单颗磨粒加工特征时间2.7.2 磨削过程中材料表面应变率2.8 本章小结第3章 磨粒冲击对零件表面完整性影响机制3.1 基于冲击作用的工件表面磨削加工硬化层的产生与机制3.1.1 工件表面层加工硬化层指标3.1.2 冲击产生的硬化3.1.3 高应变率下材料的动态响应3.1.4 位错的形成3.1.5 位错的应力场理论3.1.6 加工硬化理论分析3.1.7 位错强化的数学表达3.1.8 磨削区位错密度3.2 冲击对零件残余应力的影响3.2.1 残余应力的分类3.2.2 磨削残余应力产生原因分析3.3 冲击对零件表面粗糙度的影响3.3.1 磨削表面粗糙度理论分析3.3.2 磨削加工表面粗糙度经验公式3.4 本章小结第4章 单颗磨粒对零件表面冲击过程仿真4.1 DEFORM软件4.1.1 软件简介4.1.2 自适应网格重划分技术4.2 拉格朗日插值法4.3 刚塑性有限元法4.3.1 概述4.3.2 刚塑性有限元法基本方程4.4 刚塑性有限元列式及求解4.4.1 离散化4.4.2 罚函数法基本求解公式4.4.3 线性化4.5 模型的建立和求解4.5.1 几何模型的建立4.5.2 有限元模型的建立4.5.3 模拟参数的确定4.6 仿真结果与讨论4.6.1 单颗磨粒切削成屑分析4.6.2 磨削阶段主切削力的分析4.6.3 等效应力的分析4.6.4 等效应变率的分析4.6.5 硬化层厚度分析4.7 本章小结第5章 冲击对零部件磨削表面强化作用的实验研究5.1 实验设备5.2 实验过程5.3 试件硬度及硬化层厚度测量5.3.1 实验仪器及原理简介5.3.2 实验过程和结果及分析5.4 本章小结第6章 结论与展望6.1 结论6.2 展望参考文献参加科研情况说明致谢
相关论文文献
标签:冲击论文; 零部件论文; 磨削加工论文; 完整性论文; 强化作用论文;