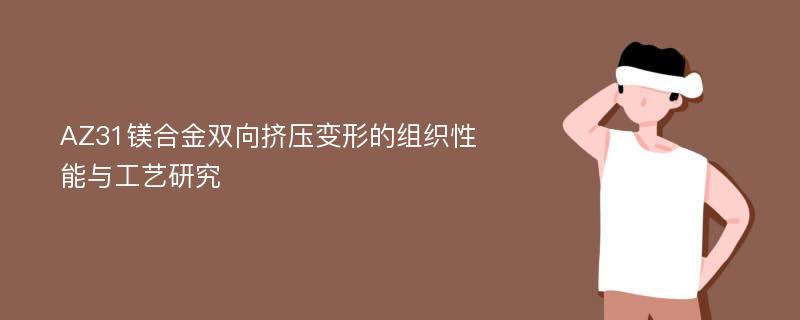
论文摘要
本文旨在研究DDE变形过程中AZ31系镁合金的微观组织演变和变形后的力学性能以及DDE变形工艺。重点讨论了DDE变形过程中的晶粒细化机制,变形后的室温力学性能及断裂机制,以及DDE变形过程中的挤压力和应力应变分布。以期对AZ31镁合金的DDE变形机理和DDE变形工艺本身进行初步研究和探讨。论文选取了应用比较广泛的AZ31镁合金作为研究对象。采用金相显微分析(OM)、X射线衍射分析和电子背散射衍射分析(EBSD)等手段,对不同挤压温度下AZ31镁合金在DDE变形过程中的显微组织和织构的演变规律进行了分析;进行室温力学性能测试,探讨了DDE成型后AZ31镁合金的室温力学性能和室温下的断裂方式及断裂机理;采用透射电子显微技术(TEM),探讨了DDE变形过程中AZ31镁合金的晶粒细化机制;对经DDE变形后的AZ31镁合金进行了退火处理,探讨了经DDE变形后AZ31镁合金显微组织的变化及其力学性能;采用有限元软件对DDE变形工艺进行了模拟分析,对DDE变形过程中挤压力和应力应变分布进行了初步探讨。取得如下结果:AZ31镁合金经DDE变形后,镁合金晶粒明显细化。变形后合金室温延伸率随晶粒细化而提高,屈服强度和硬度都随晶粒细化而提高,与Hall-Petch关系的趋势符合,由于受织构影响,250℃时与Hall-Petch关系相违背。在250450℃温度范围内进行DDE变形,AZ31镁合金的晶粒随变形温度的降低而减小。AZ31镁合金经DDE热变形后,合金的室温强韧性得到综合改善。随着挤压比的增大,合金的晶粒细化效果更显著。在挤压比为10.125时,晶粒变得更加致密细小,而且分布均匀,镁合金的屈服强度和延伸率都得到了提高。同时在挤压比为10.125,温度300℃,挤压后的AZ31镁合金,平均晶粒尺寸为3μm,屈服强度达到232MPa,延伸率达到了18.6%,说明在低温与大挤压比的共同作用下,镁合金的韧性能有效地得到提高。DDE变形过程中AZ31镁合金的晶粒细化机制可以归结为模具转角的剪切作用和挤压比变形引起的晶粒破碎和整个DDE变形过程中发生的连续动态回复和再结晶(CDRR)。对于连续动态回复和再结晶,变形初期在粗晶粒内产生许多位错,位错会发生交互作用,重新排列形成位错界面以及亚晶界,而形成的位错界面以及亚晶界会进一步演化为小角度晶界和大角度晶界,镁合金得以细化。利用有限元软件Deform-3D对DDE变形过程中的挤压力和应力应变分布进行了有限元模拟,发现模拟结果和实验结果基本吻合。
论文目录
摘要ABSTRACT1 绪论1.1 概述1.2 镁合金的特点及应用1.2.1 镁合金的主要特点1.2.2 镁合金的应用领域1.3 国内外镁合金研究现状1.3.1 国外镁合金研究现状1.3.2 国内镁合金研究现状1.4 变形镁合金传统挤压研究1.4.1 传统挤压工艺1.4.2 传统挤压存在的问题1.5 变形镁合金等径角变形研究1.5.1 ECAP 工艺1.5.2 ECAE 存在的问题1.6 晶粒和织构对镁合金力学性能的影响1.7 再结晶退火概述1.7.1 再结晶现象1.7.2 再结晶退火意义1.7.3 再结晶形核与核长大1.8 动态再结晶概述1.8.1 动态再结晶现象1.8.2 动态再结晶意义1.8.3 镁合金动态再结晶的理论基础1.8.4 动态再结晶的影响因素1.8.5 动态再结晶的形核机制1.9 课题的目的和意义1.10 课题的主要研究内容1.11 小结2 实验内容2.1 实验方案2.2 模具设计2.3 实验材料2.4 不同温度不同挤压比DDE 变形实验2.5 退火处理2.6 金相观察实验2.7 显微硬度测定实验2.8 晶粒尺寸测量2.9 X–衍射实验2.10 力学性能实验2.11 扫描电镜实验2.12 透射电镜实验2.13 EBSD 实验2.14 小结3 DDE 变形AZ31 镁合金的微观组织演变与分析3.1 不同挤压温度的流变组织演变3.2 挤压前后横截面组织对比3.3 挤压前后纵截面组织对比3.4 提高挤压比后的显微组织3.5 挤压态退火态横截面组织对比3.6 挤压态与退火态的纵截面组织对比3.7 X 射线衍射分析3.7.1 均匀化3.7.2 双向挤压3.8 织构演变分析3.9 影响DDE 成型组织和性能的主要因素3.9.1 内角Ф3.9.2 挤压比λ3.9.3 挤压温度T3.9.4 挤压速度3.9.5 润滑3.10 小结4 DDE 变形AZ31 镁合金的力学性能4.1 显微硬度测试4.2 拉伸压缩性能测试4.3 断口失效分析4.3.1 挤压态压缩破坏实验4.3.2 退火态压缩破坏实验4.3.3 挤压态拉伸破坏样4.3.4 拉伸和压缩变形方式对镁合金的影响4.3.5 孪生与断裂之间的关系4.4 小结5 DDE 变形AZ31 镁合金晶粒细化机理5.1 DDE 镁合金晶粒细化及变形机理5.2 DDE 变形过程中动态再结晶机制5.3 小结6 DDE 变形有限元模拟分析6.1 等通道转角挤压过程有限元分析的基本理论6.1.1 有限元模型(Finite Element Model-FEM)研究背景6.1.2 有限元法的基本原理6.1.3 刚塑性材料的基本方程6.1.4 刚塑性有限元变分原理6.1.5 有限元法的一般解题步骤6.1.6 FEM 在塑性成型中的应用6.2 有限元模拟6.2.1 DEFORM-3D 软件介绍6.2.2 有限元模型的建立6.2.3 材料的流动应力-应变曲线6.2.4 模拟过程参数选取6.3 模拟结果分析6.3.1 变形行为6.3.2 应力6.3.3 应变6.3.4 挤压力6.4 DDE 变形展望6.5 小结7 结论致谢参考文献附录附录A 作者在攻读学位期间发表的论文目录附录B 作者在攻读学位期间取得的科研成果目录
相关论文文献
标签:镁合金论文; 双向挤压论文; 力学性能论文; 微观组织演变论文; 有限元论文;