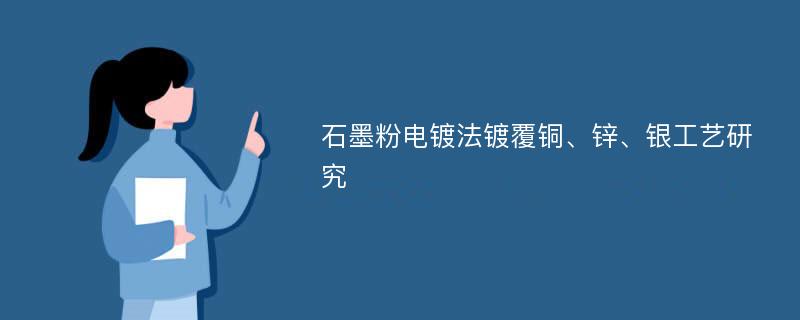
论文摘要
石墨/铜(锌、银)复合材料结合了铜(锌、银)优良的导电性、导热性、延展性和石墨的自润滑性、耐高温和耐腐蚀等优异性能,其应用范围越来越广,是当前相关复合材料领域研究的热点。用电镀法在预处理过的微米级鳞片石墨粉上分别镀覆一层铜、锌、银,制备出了性能优良的铜/石墨、锌/石墨和银/石墨复合材料粉末。考察了工艺条件对所制得的成品含铜量、含锌量、含银量及电镀效果的影响,并对所制得的块状复合材料的电阻率、硬度、密度和抗折强度等性能进行了研究。采用含碳量大于98.5wt%的鳞片石墨粉作为主要原料,经除油、粗化、表面活性剂浸泡等过程制得预处理石墨粉。镀液的配制是将主盐、络合剂及添加剂等按一定比例和顺序混合均匀,然后把一定量的预处理石墨粉加入镀液中,经超声振荡、搅拌,得到均匀的分散体系。以预镀金属(铜、锌、银)作为阴极和阳极,通以适当的电流,调整镀液的pH值,隔一定时间进行搅拌,电镀即可进行。成品经洗涤、过滤后,用钝化剂进行钝化处理,然后洗涤并烘干,即可制得表面镀覆一层金属的石墨粉。用扫描电子显微镜(SEM)对石墨/铜(锌、银)的微观形貌进行表征;用X射线衍射仪(XRD)对复合材料粉末850℃灼烧后的剩余物进行分析判断并计算复合粉末中金属含量;用激光粒度分析仪测量预处理石墨粉和复合材料粉末的粒度变化曲线。实验结果表明:在800ml蒸馏水中加入8g CuSO4·5H2O和20ml浓硫酸配制成电镀液,加入5g预处理过的石墨粉,搅拌间隔时间10min,控制电流密度为9A/dm2和电镀时间60min时制得的镀铜石墨粉的含铜量可达70wt%。镀锌过程中,考察了氧化锌、石墨粉加入量和电镀时间等工艺对镀锌石墨粉含锌量及电镀效果的影响。最佳工艺条件为:ZnO浓度为12.5g/L、NaOH浓度为125g/L、石墨粉加入量为8.3g/L、控制电流6A、搅拌间隔时间15min、施镀时间为75min时制备的镀锌石墨粉镀锌率可达78wt%。扫描电镜照片显示锌在镀锌石墨粉制成的复合材料中呈弥散分布,该复合材料的界面为锌/锌界面,界面结合强度较高。而锌与石墨机械混合制得的石墨/锌复合材料,锌在其中基本成孤岛结构,通电时难以形成电流连续的通道。对两种材料的密度、硬度、电阻率和抗折强度进行分析,并与传统的通过机械混合法制得的复合材料进行对比,发现前者具有低的电阻率以及高的密度、硬度、抗弯强度,是一种性能优异的新型石墨/锌复合材料。镀银过程中,主要研究了镀液中硝酸银浓度、石墨粉加入量和阴极电流密度等工艺条件对镀银石墨粉含银量和电镀效果的影响。研究结果表明:当镀液中硝酸银浓度为12g/L,预处理石墨粉加入量为6g/L,丁二酰亚胺做络合剂且用量为28g/L,电流密度控制在0.2-0.5A/dm2,pH值在8.5-10.0之间时,制得含银量超过70wt%的镀银石墨粉。通过电镀法制得的块状复合材料其金属在石墨基体中呈弥散分布,形成了连续的三维网络结构,使其在通电时容易形成电流连续的通道,有效降低了其电阻率。另外,金属与金属之间的结合强度比金属与石墨之间的结合强度大,所以使得块状复合材料的硬度和抗折强度等性能均有所提高。
论文目录
摘要Abstract插图索引表格索引第1章 绪论1.1 前言1.1.1 电镀工业发展概况1.1.2 电镀基本概念1.2 复合电镀1.2.1 复合电镀的历史及研究现况1.2.2 电沉积机理1.2.3 电镀的影响因素1.3 电镀法石墨粉表面镀铜1.3.1 石墨/铜复合材料的历史及研究现状1.3.2 石墨/铜复合材料的制备方法1.3.3 石墨/铜复合材料的应用1.3.4 电镀法镀铜表面活性剂1.3.5 镀铜石墨粉的表面稳定化处理1.4 电镀法石墨粉表面镀锌1.4.1 石墨/锌复合材料的历史及研究现状1.4.2 石墨/锌复合材料的制备方法1.4.3 石墨/锌复合材料的应用1.4.4 电镀液废水处理1.5 电镀法石墨粉表面镀银1.5.1 石墨/银复合材料的历史和研究现状1.6 选题背景及研究内容第2章 实验方法及实验内容2.1 实验主要原料和仪器设备2.1.1 实验主要原料2.1.2 实验主要仪器设备2.1.3 电镀装置简图2.2 试样制备2.2.1 石墨粉预处理2.2.2 电镀液配制2.2.3 电镀工艺流程2.2.4 电镀后样品钝化处理2.2.5 复合材料试样制备2.3 试样性能测试2.3.1 体积密度测定2.3.2 肖氏硬度测定2.3.3 室温体积电阻率测定2.3.4 抗压强度测定2.3.5 X射线衍射(XRD)分析2.3.6 扫描电子显微镜(SEM)分析2.3.7 镀铜石墨粉含铜量测定2.3.8 镀锌石墨粉含锌量测定2.3.9 镀银石墨粉含银量测定第3章 石墨粉电镀法镀铜工艺研究3.1 引言3.2 硫酸盐镀铜电极过程3.3 电镀工艺对镀铜石墨粉含铜量的影响3.3.1 搅拌间隔时间对镀铜石墨粉含铜量的影响3.3.2 浓硫酸加入量对镀铜效果的影响3.3.3 石墨粉加入量对镀铜效果的影响3.3.4 表面活性剂浓度对镀铜效果的影响3.3.5 电流密度和电镀时间对镀铜效果的影响3.3.6 最佳工艺配方的确定3.4 石墨粉镀铜前后粒度变化分析3.5 扫描电镜(SEM)分析3.5.1 预处理石墨粉和镀铜石墨粉SEM分析3.5.2 镀铜石墨粉复合材料SEM分析3.6 本章小结第4章 石墨粉电镀法镀锌工艺研究4.1 引言4.2 实验原理4.3 电镀工艺对镀锌石墨粉含锌量的影响4.3.1 搅拌间隔时间对镀锌石墨粉含锌量的影响4.3.2 ZnO浓度对镀锌石墨粉含锌量的影响4.3.3 石墨粉加入量对镀锌石墨粉含锌量的影响4.3.4 NaOH浓度对镀锌石墨粉含锌量的影响4.3.5 施镀时间对镀锌石墨粉含锌量的影响4.3.6 施镀电流对镀锌效果的影响4.4 钝化剂钝化效果分析4.5 石墨粉镀锌前后粒度变化分析4.6 扫描电镜(SEM)分析4.6.1 镀锌石墨粉扫描电镜分析4.6.2 石墨/锌复合材料扫描电镜分析4.7 石墨/锌复合材料的物理性能4.8 本章小结第5章 石墨粉电镀法镀银工艺研究5.1 引言5.2 电镀工艺对镀银石墨粉含银量的影响5.2.1 硝酸银浓度对镀银石墨粉含银量的影响5.2.2 石墨粉加入量的影响5.2.3 络合剂的选择和用量对镀银石墨粉含银量的影响5.2.4 阴极电流密度对镀银效果的影响5.3 石墨粉镀银前后粒度变化分析5.4 镀银石墨粉扫描电镜(SEM)分析5.5 本章小结结论本论文主要创新点参考文献致谢附录A:攻读学位期间所发表的论文
相关论文文献
标签:石墨粉论文; 电镀工艺论文; 镀覆金属量论文; 复合材料论文;