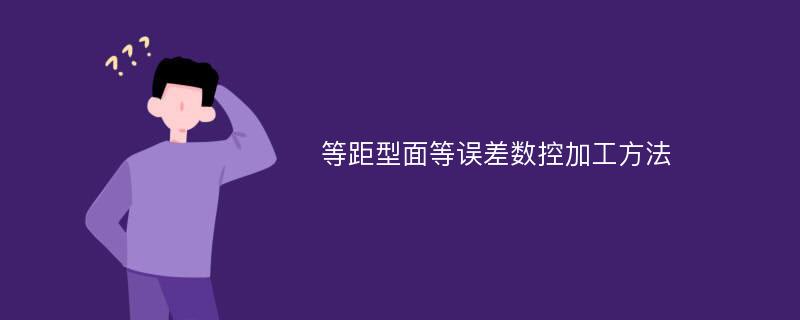
论文摘要
等距型面无键联接的应力集中不显著,装拆方便,传递扭矩大,能够实现自动对中,以间隙配合装配,以过盈配合工作,具有较高的应用价值。但因等距型面加工工艺复杂,制约了等距型面无键联接的推广应用。数控技术的快速发展为等距型面的加工提供了制造基础,也为等距型面无键联接的应用提供了技术支持。本文首先分析了等距曲线的等误差直线逼近方法,等距曲线是由参数方程决定的较为复杂的曲线,按常规的等角度、等误差、等弦长等方法进行逼近,很难求解。因此,本文采用等误差步长估计的方法推导出节点坐标的递推公式。这种方法也为由参数方程描述的其它复杂曲面数控加工提供了借鉴。其次,以节点坐标的递推公式为基础,编制Visual Basic程序,来计算节点的坐标,避免了烦琐的手工计算,提高了计算精度。对任意给定参数(一般N=3,平均半径R和偏心率e为任意给定)和加工误差(δ)要求的等距曲线,可自动计算并生成节点坐标数据。为检查输出数据的准确性,利用MasterCAM X3实现自动编程并进行刀具路径模拟。由于数控加工精度高,数控加工时的尺寸公差要求与普通机床有较大区别。在论文的第三章,提出了如何合理确定数控加工尺寸,提高数控加工精度的方法。MasterCAM X3生成的NC程序不能直接应用于生产,需要大量的手工修改。故对MasterCAM X3后处理程序进行了编辑与优化,使MasterCAM X3生成的NC程序可以直接应用于生产,实现了真正的自动编程。自动编程生成的NC程序能否加工出合格的产品,在企业里通常采用“单步运行”、“首件试切”的方法检验并调试程序。本文采用数控仿真软件来检验和调试NC程序,降低了加工成本,提高了加工效率,实现了CAD/CAM自动编程软件与仿真软件的科学结合,保证了所生成的NC程序准确无误。最后,利用XH714B三轴立式加工中心对本文提出的编程方法进行了实验验证,加工出了等距型面传动轴和弹性柱销联轴器等距型面毂孔,表面质量及公差满足了图纸要求。通过对实验数据进行深入分析,提出了进一步提高加工精度和表面质量的方法和措施。
论文目录
致谢摘要Abstract1. 引言1.1 论文课题来源1.2 论文课题的提出及其意义1.3 国内外的研究现状1.4 本文的主要研究内容1.5 本章小结2. 等距型面的等误差直线逼近2.1 等距曲线的形成及其方程2.1.1 直线的法式方程2.1.2 等距曲线的形成与方程2.1.3 其它形式的等距曲线方程2.2 等距曲线的等误差直线逼近2.3 本章小结3. 等距曲线节点参数的求解3.1 Visual Basic 程序的流程图3.2 界面设计3.3 编写程序事件过程3.4 程序的运行3.5 计算实例3.6 几何尺寸公差的处理3.7 节点计算实例3.7.1 求等距型面轴和孔的平均尺寸和平均公差3.7.2 等距型面轴的节点坐标计算3.7.3 联轴器等距型面毂孔节点坐标计算3.8 本章小结4. 等距型面数控加工自动编程4.1 等距曲线绘制4.2 三维模型的建立4.3 等距型面轴数控加工自动编程4.3.1 机床选型与参数设置4.3.2 面铣削刀具路径4.3.3 外形铣削粗加工刀具路径4.3.4 外形铣削精加工刀具路径4.3.5 实体加工模拟4.4 联轴器等距型面毂孔加工仿真4.4.1 机床选型与参数设置4.4.2 面铣削刀具路径4.4.3 挖槽粗加工刀具路径4.4.4 残料式外形铣削精加工刀具路径4.4.5 实体加工模拟4.5 本章小结5 后置处理的编辑与优化5.1 后置处理文件*.PST 的组成5.2 后置处理文件*.PST 的编辑与优化5.2.1 后置处理的意义5.2.2 NC 程序特点分析5.2.3 后处理文件的编辑与优化5.3 本章小结6. 数控加工仿真6.1 数控机床的对刀6.1.1 X、Y 轴对刀6.1.2 Z 方向对刀6.2 等距型面轴的数控加工仿真6.3. 等距型面毂孔数控加工仿真6.4 本章小结7. 加工试验与数据分析7.1 数控加工试验7.2 实验数据整理7.3 试验数据分析7.4 本章小结8 结论与展望8.1 结论8.2 创新点8.3 展望参考文献附录Ⅰ:MasterCAMX3 默认后处理器编辑与优化部分程序代码附录Ⅱ:等距型面轴部分 NC 程序清单附录Ⅲ:联轴器等距型面毂孔部分 NC 程序清单作者简历学位论文数据集
相关论文文献
标签:等距型面论文; 等误差直线逼近论文; 数控加工论文; 编程论文; 仿真论文; 自动编程论文;