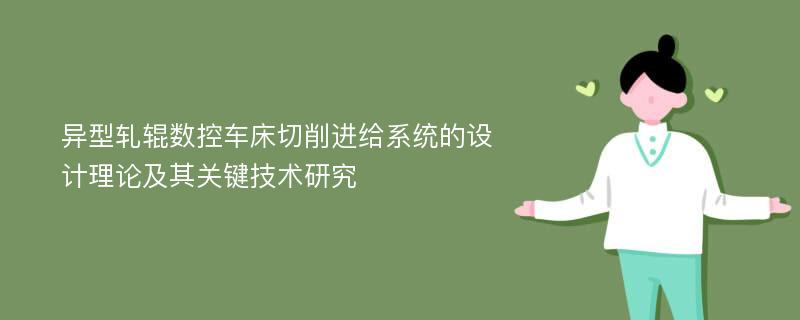
论文摘要
轧辊是轧机的重要部件之一,是轧制作业的主要变形模具,其质量直接决定了轧制产品的质量。而异型轧辊属于非圆截面零件,由于其复杂的截面形状,较高的形位、尺寸精度,以及较差的加工工艺性,对加工设备的性能提出了更高的要求。如何提高复杂曲面异型轧辊的加工质量、加工效率,降低成本,已成为冶金机械领域中备受关注的难点和热点之一。本课题以异型轧辊数控专用车床设计开发中的关键技术为切入点,利用曲线拟合理论、机械运动学、动力学理论、优化方法及有限元方法等手段,较深入地研究了异型轧辊数控专用车床的进给系统的设计理论和关键技术。取得了以下主要创新性成果:1.对异型轧辊横截面外轮廓曲线进行了分析与拟合,给出了异型轧辊环状孔型曲线的解析式;依据孔型曲线的特性,提出了分段逼近的策略和逼近方法。2.提出了异型轧辊数控车床采用双径向进给系统,并对进给系统刀具的运动特性进行了分析,利用ADAMS软件对刀具的径向进给运动进行了仿真,确定了刀具径向进给参数。3.完成了进给系统与主轴系统的运动学匹配设计。并得出两点结论:一是在满足加工精度的前提下,应尽可能地降低主轴转速,使径向进给速度和加速度具有较大设计空间;二是刀具的进给速度和加速度较高时,径向进给系统必须具有较高的刚度、固有频率和合适的阻尼,且具有较小的运动惯量、时间常数和弹性变形。4.建立了进给系统的结构模型和动力学模型。进行了动态性能仿真,并具体分析了传动系统各结构参数对系统动态性能的影响,优化了相关结构参数,满足了实际生产的要求。本课题是针对异型轧辊的加工提出的,其研究成果对非圆类零件车削加工技术的研究同样具有参考价值和指导意义。
论文目录
摘要ABSTRACT第一章 绪论1-1 数控机床的应用和发展1-1-1 数控机床的构成及应用1-1-2 数控机床的发展趋势1-2 数控机床的进给伺服系统1-2-1 数控机床进给伺服系统的功能1-2-2 数控机床进给伺服系统的构成1-2-3 数控机床对进给伺服系统的要求1-2-4 进给伺服系统的发展趋势及研究现状1-3 本课题的研究背景1-3-1 非圆截面零件的应用1-3-2 非圆截面零件的车削加工方法1-3-3 异型轧辊的应用及工艺要求1-3-4 车削工艺及其在异型截面加工中的应用1-4 本课题的研究内容及意义1-5 本章小结第二章 异型轧辊环状孔型曲线分析2-1 异型轧辊环状孔型曲线拟合2-1-1 异型轧辊环状孔型曲线加工工艺要求2-1-2 异型轧辊横截面外廓曲线拟合2-2 异型轧辊环状孔型曲线逼近2-2-1 等间距直线逼近法2-2-2 等步长直线逼近法2-2-3 等误差直线逼近法2-2-4 等误差圆弧逼近法2-3 曲线逼近方法综合优选2-4 本章小结第三章 刀具径向进给运动特性分析及运动仿真3-1 异型轧辊数控车床刀具径向进给运动特性分析3-1-1 刀具径向进给运动分析3-1-2 刀具径向进给运动特性3-2 刀具径向进给运动仿真及进给参数求解3-2-1 机械系统仿真软件ADAMS3-2-2 刀具径向进给运动仿真3-2-3 仿真结果分析3-3 本章小结第四章 异型轧辊数控车床进给传动系统的动力学建模4-1 机床的动力分析及动态设计4-2 机床进给系统结构参数对其动态性能的影响4-3 机床的动力学建模及结构模型的简化4-4 异型轧辊数控车床进给传动系统的动力学建模4-4-1 U 向进给传动系统动力学建模4-4-2 X 向进给传动系统动力学建模4-5 本章小结第五章 数控车床进给系统动态性能分析及仿真5-1 机械系统的动态性能分析5-1-1 机械系统的时域响应分析5-1-2 时域响应分析中的性能指标5-1-3 机械系统的频率特性分析5-1-4 频率特性分析中的性能指标5-1-5 机械系统的稳定性分析5-1-6 稳定性分析中的性能指标5-1-7 数控机床进给系统动态性能分析中的干扰信号5-2 U 向、X 向进给传动系统的状态空间模型5-2-1 U 向进给传动系统的状态空间模型5-2-2 X 向进给传动系统的状态空间模型5-3 数控车床进给系统动态性能仿真及结果分析5-3-1 U 向进给系统动态性能仿真5-3-2 U 向进给系统结构参数改变时的动态性能仿真5-3-3 X 向进给系统动态性能仿真5-3-4 X 向进给系统结构参数改变时的动态性能仿真5-4 本章小结第六章 数控车床进给传动系统结构参数的优化6-1 机械优化设计方法6-1-1 优化问题的建模6-1-2 优化问题的求解6-2 U 向进给传动系统优化数学模型的建立6-2-1 U 向进给传动系统的设计变量6-2-2 U 向进给传动系统的目标函数6-2-3 U 向进给传动系统的约束条件6-2-4 U 向进给传动系统的优化目标函数求解6-3 X 向进给传动系统优化数学模型的建立6-3-1 X 向进给传动系统的设计变量6-3-2 X 向进给传动系统的目标函数6-3-3 X 向进给传动系统的约束条件6-3-4 X 向进给传动系统的优化目标函数求解6-4 进给传动系统优化前后动态性能的比较6-4-1 U 向进给传动系统优化前后的动态性能比较6-4-2 X 向进给传动系统优化前后的动态性能比较6-5 提高进给系统结构参数的具体措施6-6 本章小结第七章 车刀几何参数设计7-1 刀具种类选取7-2 刀片设计7-2-1 刀片外形的选择7-2-2 车刀角度选取7-3 加工过程中切削力计算7-3-1 切削运动分析7-3-2 切削力计算7-4 刀柄几何参数设计7-4-1 刀柄材料的选取7-4-2 刀颈形状选取7-4-3 刀柄尺寸的设计7-5 基于有限元的车刀刚度验证及几何参数优化7-5-1 有限元方法简介7-5-2 问题描述7-5-3 刀柄的优化设计7-6 本章小结第八章 车削部件受力分析及设计8-1 刀架方案的提出8-2 有限元算法建模与流程8-2-1 有限元模拟建模相关数据8-2-2 静态力学分析假设和量纲8-2-3 有限元计算模型的前处理8-2-4 有限元计算模型的后处理8-3 有限元计算结果分析与方案选定8-3-1 结果输出8-3-2 结果分析8-4 刀架方案的优化设计8-4-1 初始方案分析8-4-2 几何优化设计数学模型的建立8-4-3 结构优化设计方案8-5 本章小结第九章 非线性载荷工况下车削部件力学分析9-1 非线性问题概述9-2 径向非线性动态切削量计算9-3 时间序列计算9-4 非线性切削力计算9-5 非线性载荷加载9-5-1 加载方案一:非线性载荷单分析步直接加载9-5-2 加载方案二:非线性载荷两分析步过渡加载9-5-3 加载特性分析9-6 车削部件准静态力学分析9-6-1 刀架应力分布分析9-6-2 刀尖点位移分析9-7 车削部件动态力学分析9-7-1 刀尖点动态位移响应9-7-2 刀尖点动态运动特性9-7-3 刀架支反力动态响应9-7-4 车削部件固有频率9-8 本章小结第十章 总结与展望10-1 工作总结10-2 问题与展望参考文献致谢攻读博士学位期间取得的相关成果
相关论文文献
- [1].四辊轧机轧辊轴向窜动分析与控制[J]. 冶金管理 2020(05)
- [2].火车轮轧制用主轧辊环状裂纹原因分析[J]. 大型铸锻件 2020(04)
- [3].轧辊磨削中的常见问题及其处理[J]. 柳钢科技 2020(03)
- [4].轧辊开裂原因浅析[J]. 热处理 2020(05)
- [5].车轮主轧辊工作面裂纹失效分析[J]. 大型铸锻件 2020(06)
- [6].轧辊修复方法的研究[J]. 现代制造技术与装备 2018(01)
- [7].考虑轧辊成本的轧制计划编制与调整[J]. 控制与决策 2017(01)
- [8].高速轧辊磨头偏心套油膜润滑压力的数值求解[J]. 现代机械 2017(02)
- [9].轧辊铸锭的温度场计算机数值模拟[J]. 煤炭技术 2017(05)
- [10].轧辊偏心的间歇采样重复控制补偿[J]. 燕山大学学报 2017(03)
- [11].轧辊轴颈损伤分析及解决对策[J]. 本钢技术 2016(03)
- [12].轧辊偏心信号的辨识及补偿方法研究[J]. 自动化与仪器仪表 2017(08)
- [13].板形矫正轧辊轧制变形的受力分析与仿真研究[J]. 合肥工业大学学报(自然科学版) 2017(10)
- [14].废旧轧辊再制造新技术填补国内空白[J]. 表面工程与再制造 2016(01)
- [15].基于有限元法的均匀轧辊研究(英文)[J]. 机床与液压 2016(12)
- [16].应用豪克能技术提高轧辊耐磨性和抗疲劳性能应用试验[J]. 现代冶金 2014(05)
- [17].中钢邢机成功再制造国内154吨超大轧辊[J]. 表面工程与再制造 2015(05)
- [18].有效降低森吉米尔轧机轧辊成本的方法[J]. 轧钢 2020(02)
- [19].在轧辊检测中应用涡流和表面波复合探伤[J]. 冶金管理 2020(05)
- [20].冷轧轧辊失效原因分析及改进措施[J]. 金属世界 2020(03)
- [21].积极响应绿色发展 全面树立行业标杆——记邢台德龙机械轧辊有限公司[J]. 环境保护 2019(09)
- [22].离心复合高铬钢轧辊的研究与实践[J]. 中国金属通报 2019(10)
- [23].轧辊精车加工工艺改进[J]. 工具技术 2017(02)
- [24].大型和超大型冶金轧辊再制造技术研究与应用[J]. 中国高新技术企业 2017(07)
- [25].冷连轧过程控制系统轧辊高效管理的实现[J]. 机械设计与制造 2015(12)
- [26].2300线高铬铁报废轧辊在1880线的改制应用[J]. 金属世界 2014(06)
- [27].轧辊及轧辊轴承备品的管理[J]. 河北企业 2015(06)
- [28].轧辊材料疲劳裂纹扩展理论计算与分析[J]. 宝钢技术 2015(04)
- [29].轧辊气雾冷却[J]. 科技创新与品牌 2015(11)
- [30].关于离心轧辊辊身亮斑问题的探讨[J]. 铸造技术 2013(09)
标签:异型轧辊论文; 进给系统论文; 动态性能论文; 动力学建模论文; 优化设计论文; 有限元论文;
异型轧辊数控车床切削进给系统的设计理论及其关键技术研究
下载Doc文档