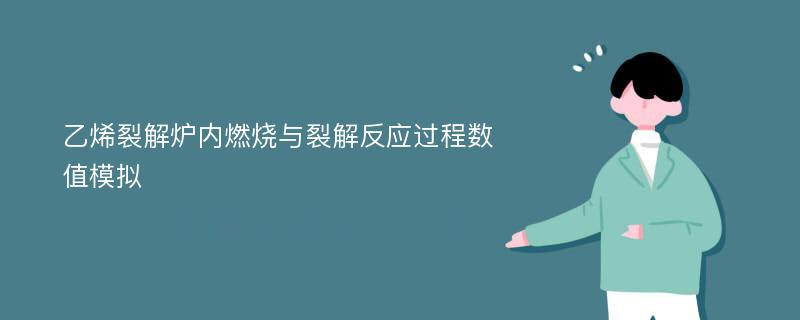
论文摘要
乙烯裂解过程是乙烯工业的关键技术之一,裂解炉是乙烯装置的核心设备。目前世界上仅有少数公司掌握生产乙烯的成套技术,国内对引进、吸收此项技术十分重视。但是截止目前,由于国内对裂解炉炉内的流体流动、燃烧、裂解反应与热量传递等情况缺乏充分的认识,导致我国乙烯裂解炉技术还比较落后。因此,深入研究裂解炉内传递与反应过程细节对于裂解炉运行分析和优化设计具有十分重要的意义。本文在研究国内外乙烯工业的历史、现状、发展趋势的基础上,全面系统的对乙烯裂解炉膛内燃料燃烧、烟气流动传热和反应管内的裂解原料的流动、传热及裂解反应等过程及其各个过程之间的耦合关系进行分析,采用扩散燃烧PDF模型,离散坐标辐射传热模型、25分子反应动力学并结合湍流k-ε模型,建立了能够描述裂解炉内燃烧与裂解反应等众多复杂传递反应过程及其耦合作用的综合数学模型。利用新建的乙烯裂解炉内的数学模型对齐鲁石化的北方裂解炉进行模拟计算,模拟计算结果与工业数据吻合良好,验证了建立的数学模型的准确性。并对乙烯裂解炉膛和反应管内的速度、温度、压力、热通量分布及组分浓度分布进行了进一步的分析,揭示了乙烯裂解炉内流动、传热、传质、燃料燃烧与裂解反应等过程的基本特征,以及这些过程之间强烈的耦合关系,为乙烯裂解炉的改造和设计提供全方位、多层次的化学工程参数。利用已经建立的乙烯裂解炉数学模型,对反应管内不同的操作参数(裂解原料质量流率、热通量和水蒸汽稀释比)和结构参数进行数值模拟,得到了不同工况下的温度及组分浓度分布。通过对模拟结果进行比较,定量掌握了各个操作参数和结构参数对裂解炉内燃烧与反应过程的影响,为裂解炉的设计和优化操作提供理论指导。通过对乙烯裂解炉分离迭代算法优缺点的分析,提出能真正体现炉膛与反应管之间的热量耦合关系的乙烯裂解炉耦合模拟计算的新方法,并对缩小简化的工业裂解炉进行模拟计算。计算结果表明:燃料与裂解原料分别在炉膛与反应管内各自的空间内进行一系列的流动、传热与传质过程,炉膛与反应管之间的热通量分布随空间的不同而不同,验证新方法的合理性。
论文目录
摘要ABSTRACT第一章 文献综述1.1 乙烯装置主要的产品及其用途1.2 国内外乙烯工业的生产现状1.2.1 全球乙烯工业发展简述1.2.2 我国乙烯工业的发展简述1.3 乙烯生产方法及其典型工艺1.3.1 乙烯的生产方法1.3.2 裂解炉与典型生产工艺1.4 乙烯技术的国有化进展和发展趋势1.4.1 乙烯技术的国有化进展1.4.2 CBL 裂解技术的发展1.4.3 我国乙烯工业的发展趋势1.5 乙烯裂解炉内传递与反应过程简述1.5.1 乙烯裂解炉内传递与反应过程描述1.5.2 乙烯裂解炉内存在问题1.6 裂解炉内燃烧与反应过程的研究方法1.6.1 实验研究1.6.2 工程试验1.6.3 计算流体力学(CFD)数值模拟1.7 本课题的主要研究任务及意义第二章 乙烯裂解炉内燃烧裂解反应数值模拟方法的选择2.1 乙烯裂解炉内数学模型的开发2.2 湍流流动模型的选择2.3 湍流燃烧的选择2.3.1 湍流燃烧的直接数值模拟2.3.2 湍流燃烧的大涡模拟2.3.3 燃烧的PDF 输运方程模拟2.3.4 湍流燃烧的条件矩封闭模型2.3.5 湍流燃烧的简化PDF 模型2.3.6 湍流燃烧的关联矩模型2.3.7 唯象的湍流燃烧模型2.3.8 湍流燃烧的随即涡模拟2.3.9 本节小结2.4 辐射传热模型的选择2.4.1 经验法2.4.2 罗伯-伊万斯法2.4.3 别洛康法2.4.4 区域法2.4.5 热通量法2.4.6 蒙特卡罗法2.4.7 球形谐波法2.4.8 离散传播法2.4.9 离散坐标法2.4.10 有限体积法2.4.11 本节小结2.5 裂解反应动力学模型的选择2.5.1 经验模型2.5.2 分子模型2.5.3 自由基机理模型2.6 本章小结第三章 乙烯裂解炉数学模型的建立3.1 基本微分方程组3.2 炉膛燃烧反应数学模型的建立3.2.1 燃料燃烧3.2.2 辐射传热模型3.2.3 气体辐射特性计算方法的分析与选择3.3 反应管数学模型的建立3.3.1 反应动力学数学模型3.3.2 裂解炉管的传热3.3.3 炉管的压力降3.3.4 裂解数学模型小结3.4 本章小结第四章 乙烯裂解炉数值模拟工况4.1 模拟计算工况4.2 网格划分策略及边界条件设置4.2.1 计算区域4.2.2 网格划分4.2.3 边界条件设置4.3 控制方程离散化及求解4.3.1 控制方程的离散化处理4.3.2 离散化方程求解4.4 乙烯裂解炉数学模型的数值求解过程4.4.1 炉膛数学模型的数值求解过程4.4.2 反应管数学模型的数值求解过程4.4.3 乙烯裂解炉数学模型的数值求解过程4.5 计算框图第五章 乙烯裂解炉膛模拟结果分析5.1 宏观工艺参数的模拟验证5.2 烟气流场分析5.3 炉膛内温度分布5.4 组分浓度分布5.5 炉膛向反应管传递的热通量分布5.6 本章小结第六章 乙烯裂解炉反应管管内模拟结果分析6.1 反应动力学选择6.2 流速分布6.3 压力分布6.4 温度分布6.5 浓度分布6.6 裂解反应速率分布6.6.1 反应动力学控制分析6.6.2 乙烷消耗反应速率分布6.6.3 丙烷消耗反应速率在反应管内的分布6.6.4 丁烷消耗反应速率在反应管内的分布6.6.5 乙烯二次反应速率在反应管内的分布6.7 本章小结第七章 反应管管内结焦模拟数值计算7.1 结焦对裂解过程的影响7.2 结焦机理的研究7.3 结焦机理动力学研究7.4 裂解管内结焦数学模型的建立7.5 结焦计算模拟结果分析7.5.1 结焦母体生成速率分布和浓度分布7.5.2 碳颗粒生成速率分布和浓度分布7.6 小结第八章 乙烯裂解炉优化运行的研究8.1 工艺参数对裂解反应的影响8.1.1 裂解温度和停留时间对裂解反应的影响8.1.2 压力(烃分压)8.2 裂解原料的质量流率优化调节8.2.1 温度随裂解原料的质量流率的变化8.2.2 出口组分浓度随裂解原料质量流率的变化8.2.3 出口结焦母体浓度随裂解原料质量流率的变化8.2.4 本节小结8.3 热通量优化调节8.3.1 热通量对温度的影响8.3.2 热通量对裂解原料的影响8.3.3 裂解产物随热通量的变化8.3.4 结焦母体随热通量的变化8.3.5 本节小结8.4 烃分压优化调节8.4.1 出口温度随水蒸汽的稀释比的变化8.4.2 反应物组分浓度随水蒸汽的稀释比的变化8.4.3 生成物组分浓度随水蒸汽的稀释比的变化8.4.4 结焦母体浓度随水蒸汽的稀释比的变化8.4.5 本节小结8.5 炉管结构的调整优化8.6 本章小结第九章 乙烯裂解过程整体耦合模型的提出和验证9.1 耦合模拟新方法提出背景9.2 简化裂解炉模型及网格划分9.2.1 计算域示意图9.2.2 网格划分9.3 边界条件设置和计算过程9.3.1 边界条件设置9.3.2 计算方法9.4 耦合模拟计算结果分析9.4.1 流线分布图9.4.2 温度与热通量分布9.4.3 炉膛内的燃烧结果分析9.4.4 反应管内的裂解反应结果分析9.5 本章小结第十章 总结与展望10.1 本文主要研究成果10.2 工作展望参考文献发表论文和参加科研情况说明致谢
相关论文文献
标签:裂解炉论文; 数值模拟论文; 湍流流动论文; 燃料燃烧论文; 辐射传热论文; 裂解反应论文; 耦合算法论文;