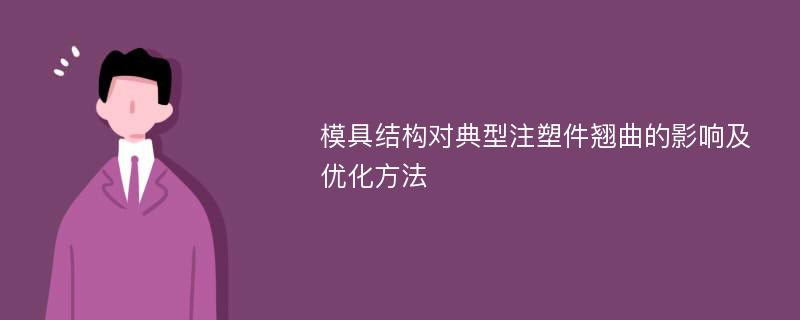
论文摘要
翘曲变形程度作为衡量产品质量的主要指标之一,越来越多地受到产品设计师、用户的关注和重视。改善和减少产品的翘曲变形,进行注塑工艺和模具结构的优化成为注塑制品生产中的重点问题之一。利用优化理论和优化方法与CAE技术相结合对工艺参数选择或产品、模具的结构进行改进成为当前注塑件翘曲变形研究的主要内容。本文针对施耐德项目“针对翘曲变形的注塑件质量改进”课题的需求,关注于模具结构对翘曲变形的影响,对注塑成型中的翘曲变形现象和CAE模拟应用作了较深入的研究,主要对典型零件注塑模浇口位置和冷却管道布置的参数选取进行了相应的优化。研究内容包括:1.研究了塑件产生翘曲变形的主要原因,尤其是注塑模具结构对翘曲变形的影响。并在此基础上讨论了注塑成型CAE模拟的发展和应用,以及翘曲变形CAE模拟的分析过程;2.利用MPI软件的翘曲分析,对典型电气外壳件注塑模的浇口位置进行了优化,使最大翘曲量模拟值减小26%;将其与实测值进行了比较,整体尺寸最大偏差0.12mm(预测值为实际值的77.6%),基本可以认为MPI的模拟值是可信的;3.采用实验设计法和神经网络对典型电气外壳件注塑模的浇口位置和冷却管道布置的参数进行了优化,最大翘曲量减小33.3%,比CAE模拟直接优化的最大翘曲量小8.3%,证明了浇口位置和冷却管道布置对翘曲变形的影响很大;4.用通用优化软件和MPI集成对简单U型件注塑模的浇口位置和数量进行优化,提出并实现了翘曲变形CAE模拟和优化算法相结合对浇口位置进行的直接优化流程和模型,优化后使得翘曲目标函数值减小了27.4%;5.从计算量和计算时间、优化结果准确程度和方法选择的目的几个方面研究并比较了翘曲优化问题中采用的几种优化方法,为优化方法的选用提供了一定的依据。
论文目录
摘要ABSTRACT第一章 概述1.1 注塑件的翘曲变形研究进展1.1.1 注塑件的翘曲变形1.1.2 翘曲变形的研究1.2 模具结构对注塑制品翘曲变形的影响1.2.1 浇注系统设计对注塑制品翘曲的影响1.2.2 冷却系统设计对注塑制品翘曲的影响1.2.3 顶出系统设计对注塑制品翘曲的影响1.3 本文主要的研究内容第二章 注塑成型CAE 的研究和应用2.1 注塑成型过程的流变学模型2.1.1 流变学基本方程2.1.2 注塑成型各阶段的数学模型假设2.2 塑料模具行业的CAE 技术2.2.1 CAE 技术简介2.2.2 塑料模CAE 技术的应用2.3 注塑件翘曲变形的CAE 研究和应用2.3.1 翘曲变形CAE 的研究2.3.2 翘曲变形CAE 的分析过程2.4 本章小结第三章 基于CAE 分析的注塑模结构优化和验证3.1 MPI(MOLDFLOW PLASTICS INSIGHT)介绍3.1.1 MOLDFLOW 软件介绍3.1.2 MPI 翘曲分析原理3.1.3 MPI 翘曲分析优化的流程3.2 基于MPI/Warp 的典型注塑模结构改进3.2.1 塑件建模3.2.2 MPI 的翘曲分析3.2.3 基于MPI 的结构改进和优化结果3.3 模拟结果的准确性验证3.3.1 测量条件3.3.2 侧壁变形的比较3.3.3 高度的比较3.3.4 模拟准确性讨论3.4 本章小结第四章 基于DOE 和神经网络的注塑模结构优化4.1 实验设计(DOE)4.1.1 实验设计概述4.1.2 正交设计概述4.2 神经网络的理论和应用4.2.1 BP 神经网络的基本原理4.2.2 BP 算法的改进4.2.3 神经网络在注塑CAE 优化中的应用4.3 基于DOE 的结构改进和优化4.3.1 全面实验对浇口位置的优化4.3.2 正交实验对冷却系统的优化4.3.3 优化结果分析和讨论4.4 神经网络和优化算法结合的浇口位置优化4.4.1 设计变量和目标函数的确定4.4.2 BP 神经网络的训练策略及结果4.4.3 最终训练后的神经网络结构和优化结果4.5 本章小结第五章 基于现代优化算法的浇口位置直接优化5.1 优化算法概述5.1.1 数值优化方法5.1.2 探索优化方法5.1.3 专家系统优化5.2 优化算法在注塑模结构设计中的应用5.2.1 优化算法在注塑模结构优化中的应用5.2.2 翘曲变形研究中的优化模型5.3 基于优化算法的浇口位置和数目优化流程5.3.1 浇口的位置和数目与产品质量5.3.2 优化算法与CAE 结合的优化流程5.4 针对翘曲变形的U 型塑件浇口位置优化5.4.1 算法选取5.4.2 数学模型建立和设计变量选取5.4.3 优化结果分析5.5 三种优化方法的比较5.6 本章小结第六章 结论与展望6.1 全文总结6.2 研究展望参考文献致谢攻读硕士期间已发表或录用的论文
相关论文文献
标签:翘曲论文; 注塑论文; 模拟论文; 优化论文;