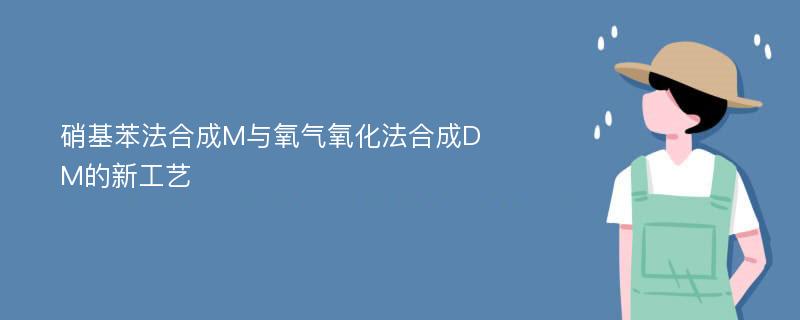
论文摘要
本文对硝基苯代替苯胺合成橡胶促进剂2.毓基苯并噻唑和氧气氧化法合成橡胶促进剂2,2’-二硫代二苯并噻哗的新工艺进行了研究。2-巯基苯并噻唑(简称M)是一种通用型橡胶促进剂,在天然胶和一般硫磺硫化的合成胶中具有快速促进作用,也是很多种橡胶促进剂的原料,并可作为增塑剂和医药中间体。本文在传统的苯胺法合成M的基础上,采用苯胺法的副产物硫化氢作为还原剂将硝基苯还原为苯胺,与-硫化碳、硫磺在高压反应釜中合成M,该法减少了硫化氢的排放,降低了成本。对其合成工艺进行了研究,并优化获得了较佳的工艺条件。根据单因素与正交实验得硝基苯部分替代苯胺的最优工艺条件为:反应温度250。C、保温压力5.0~6.0MPa、保温时时间3h。苯胺和硝基苯的摩尔比在5:1~1:1之间,平均收率达85%。苯胺和硝基苯的摩尔比在5:1~3:1之间,满足合格品仞熔点160℃要求。精制后都能达到仞熔点170℃优级品的要求。硝基苯全部替代苯胺的工艺条件为:缓慢升温,反应最高温度不得超过210℃。超过这一温度条件就会出现温度和压力的突变,严重时会发生爆炸现象。产品红外分析表明符合M的结构特征要求。鉴于该反应条件苛刻,建议采用先还原后合成的工艺。硫化氢先还原硝基苯后合成M的工艺为:硫化氢与硝基苯在温度80~100℃的条件下,反应3~4h,直接在还原后的系统中加入二硫化碳的溶硫液,按照苯胺一硝基苯法合成橡胶促进剂M的反应条件进行反应。反应过程其压力、温度变化缓和,且比单纯的苯胺法压力、温度均有所降低,对设备的损耗也大大减少。2,2’-二硫代二苯并噻唑(简称DM)为天然橡胶、合成橡胶、再生胶通用型促进剂,也可作为医药中间体。它的硫化临界温度较高(130℃),温度在140℃以上活性增加,有显著的后效性,操作安全。本文在传统的亚硝酸钠、氯气氧化法的基础上,采用粗品M为原料,氨水为溶剂,以绿色环保、来源经济的氧气做氧化剂对DM的小试合成进行了系统研究,并优化获得了较佳的工艺条件。氧气氧化法的较佳的工艺条件为:氨水浓度5%、保持温度在50~60℃、压力为0.7MPa,催化剂加入量为粗品M质量的0.20%,DM的平均收率为87.1%:平均熔点为177.6℃,达到DM一级品的要求。红外分析表明符合DM的结构特征要求。对所得产品DM精制所得的较佳的工艺条件为:甲苯和水作溶剂与粗DM质量比7:1,温度120℃,加热lh,冷却3h,冷却至30℃,抽滤、洗涤、烘干、检测,熔点达183.0℃,收率达92%,得到的DM是浅黄色品体。在小试研究的基础上,完成了2-巯基苯并噻唑(M)铵盐的氧气法制备2,2’-二硫代二苯并噻唑(DM)新工艺的中试研究,打通了工艺流程,并获得了较佳的工艺条件。中试研究得到的较佳的工艺条件为:氨水浓度5%,氨水和粗M的摩尔比4:1,溶解温度50~85℃,氧化温度60℃,氧化反应的压力O.5~O.8MPa,氧化时间约3h。用最佳条件进行多次重复试验,产品DM的质量均在一级品以上,收率均在98%以上。述结果优于小试结果。有关以氨水为溶剂,采用氧气氧化法制备DM的中试研究,目前未有文献报道。
论文目录
摘要ABSTRACT第一章 前言1.1 橡胶助剂的简介1.1.1 国外橡胶助剂的进展1.1.2 我国橡胶助剂的进展1.2 橡胶促进剂的简介1.3 橡胶促进剂发展历程1.4 橡胶促进剂发展趋势1.5 存在问题及发展建议1.6 橡胶促进剂M 简介1.6.1 橡胶促进剂M 的结构分析1.6.2 橡胶促进剂M 的传统合成方法1.6.2.1 邻硝基氯苯法生产M1.6.2.2 苯胺法生产M1.6.2.3 苯胺-硝基苯混合法生产M1.6.3 硝基苯法合成M1.6.4 橡胶促进剂M 的性质与应用1.6.5 橡胶促进剂M 的国内外发展概况1.6.6 橡胶促进剂M 的最新进展1.7 橡胶促进剂DM 的简介1.7.1 橡胶促进剂DM 结构、特性及用途1.7.2 橡胶促进剂DM 研究现状1.7.3 橡胶促进剂DM 制备方法1.7.3.1 传统的M 精制方法1.7.3.2 传统DM 的生产方法1.7.3.2.1 用亚硝酸钠作氧化剂生产DM1.7.3.2.2 用氯气作氧化剂合成DM1.7.3.2.3 次氯酸钠作氧化剂合成DM1.7.4 橡胶促进剂DM 最新研究进展1.8 本课题研究的目的和意义1.8.1 硝基苯法合成M 的目的和意义1.8.2 氧气氧化法合成DM 的目的和意义第二章 硝基苯部分或全部取代苯胺合成橡胶促进剂M2.1 实验原料和试剂2.2 实验仪器和设备2.3 苯胺法合成橡胶促进剂M2.3.1 苯胺法合成M 试验2.3.1.1 苯胺法合成橡胶促进剂M 的试验2.3.1.2 苯胺-硝基苯法合成橡胶促进剂M 的试验2.3.1.2.1 试验内容及目的2.3.1.2.2 试验步骤2.3.1.2.3 试验记录2.3.2 苯胺-硝基苯法合成M 的正交试验2.3.3 后处理阶段2.3.4 精制阶段2.3.5 检测熔点2.3.6 结构鉴定2.4 苯胺法合成橡胶促进剂M 试验结果2.5 硫化氢还原硝基苯的研究2.5.1 硝基苯的还原机理2.5.2 硫化氢还原硝基苯的试验2.6 硝基苯法合成M 试验流程2.7 硝基苯法生产M 试验过程2.8 产物的提纯精制2.9 还原硝基苯后合成橡胶促进剂M2.10 物料配比对合成M 的影响2.11 M 的精制2.12 M 的检测2.12.1 产品M 熔点检测2.12.2 产品M 红外光谱检测2.13 本章小结第三章 氧气氧化法合成橡胶促进剂DM 的研究3.1 实验原料和试剂3.2 实验仪器和设备3.3 橡胶促进剂DM 的合成3.3.1 M 的溶解3.3.2 M 的氧化3.3.2.1 大配比试验情况3.3.2.2 小配比试验3.3.2.3 稳定性试验3.3.2.3.1 操作程序3.3.2.3.2 试验数据3.3.2.3.3 尾气排放3.3.2.3.4 抽滤时损失3.3.2.3.5 转料时挥发3.3.2.3.6 烘干时的损失3.3.3 树脂的处理3.3.3.1 氨水法3.3.3.2 酸碱法3.3.4 废水情况3.4 收率及成本核算3.4.1 收率计算3.4.2 原料成本核算3.5 正交试验确定反应的工艺条件3.5.1 确定试验指标3.5.2 确定试验因素3.5.3 确定水平3.5.4 制定因素水平表3.5.5 选择正交表并进行试验3.5.6 正交试验结果分析3.5.7 最佳反应条件下的重复试验3.6 经济效益与社会效益的分析与评价3.6.1 经济效益分析3.6.2 社会效益分析3.6.3 评价3.6.4 设备投资及中试建议3.7 精制部分3.7.1 DM 的提纯3.7.2 萃取法3.7.3 重结晶法3.8 橡胶促进剂DM 的检测3.8.1 产品DM 熔点检测3.8.2 产品DM 红外光谱检测3.9 合成橡胶促进剂DM 小试的结果与讨论3.9.1 合成DM 的影响因素3.9.2 粗M 与氨的比例3.9.3 温度对溶解粗M 的影响3.9.4 压力对氧化反应的影响3.9.5 温度对氧化反应的影响3.9.6 催化剂的选择3.9.7 母液的循环利用3.9.8 最佳工艺条件3.10 氧气氧化法合成DM 的反应机理3.10.1 机理一3.10.2 机理二3.11 本章小结第四章 氧气氧化法合成橡胶促进剂DM 的中试4.1 引言4.2 中试试验部分4.2.1 中试生产所需主要设备4.2.2 生产中所需主要原料4.3 生产工艺4.3.1 工艺过程4.3.2 操作过程4.3.3 生产工艺流程图4.3.4 产品分析结果4.4 产品的使用性能4.5 总结4.5.1 结论4.5.2 存在的问题和认识4.6 新工艺效益分析报告4.6.1 社会效益4.6.2 经济效益4.7 目前状况4.8 发展设想4.9 本章小结结论参考文献致谢攻读学位期间发表的学术论文目录
相关论文文献
标签:巯基苯并噻唑论文; 二硫代二苯并噻唑论文; 硝基苯论文; 硫化氢论文; 氨水论文; 氧气氧化论文;