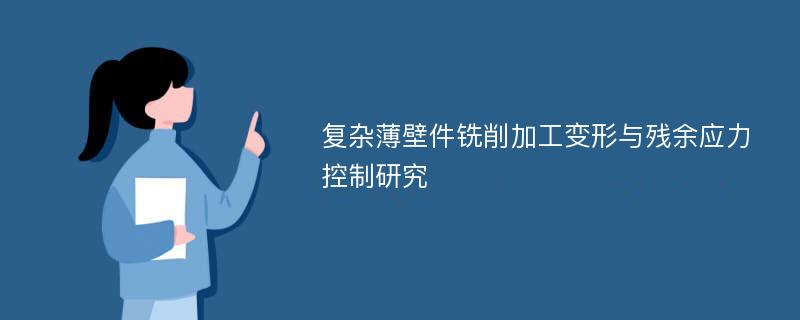
论文摘要
薄壁零件具有结构复杂、材料去除率高及刚性差等特点,在加工过后,零件通常会出现弯曲、扭曲等变形,加工精度极难达到设计要求,薄壁零件制造过程最突出的问题就是加工变形,本文以航天复杂薄壁小刚性关键件的加工变形为对象,围绕引起薄壁件变形的主要因素,包括毛坯初始残余应力的释放,铣削加工引入的残余应力对于变形的影响,切削参数对于铣削加工力的影响及工艺方案中涉及的走刀路径,装夹方案,加工顺序等入手,展开以下研究:首先,根据金属铣削机理建立了铣削加工有限元模型,采用Advantedge切削仿真有限元软件,切削模型采用二维和三维弹塑性有限元技术和Johnson-Cook本构模型,仿真分析不同的切削参数对于切削力及残余应力的影响,并且对仿真的结果进行实验验证。然后,建立航空铝合金初始残余应力及切削残余应力导致零件加工变形的有限元模型,分析毛坯初始应力对于薄壁件变形的影响,选择合适的毛坯的余量去除方式,以减小初始应力对于零件变形的影响。同时根据不同切深的残余应力对薄壁件变形的不同影响,对于切削加工中的切深进行变切深安排,以提高加工的效率和保证质量。再次,建立有限元模型分析薄壁件的加工顺序及走刀路径。采用残余应力仪测试工件表面铣削后的残余应力分布,按照不同的走刀路径编程导入至有限元软件当中,选取对于变形影响最小的走刀路径。建立不同的零件特征加工顺序的有限元模型,分析不同的零件挖槽过程中的残余应力对零件变形的影响,选取最优的切削加工顺序。。最后,综合考虑毛坯初始残余应力、切削残余应力、铣削力对于薄壁件变形的影响,并对于仿真优化方案进行实验验证,进而提出薄壁件的加工工艺,以提高薄壁件加工的精度。
论文目录
摘要Abstract第一章 绪论1.1 课题的研究背景及意义1.1.1 课题的研究背景1.1.2 课题的研究意义1.2 薄壁件加工变形成因分析1.2.1 工件的材料力学特性与结构特点1.2.2 加工过程中毛坯初始残余应力的释放1.2.3 切削过程中刀具与工件间的热力耦合作用1.2.4 工件的装夹1.2.5 刀具下刀方式的影响1.2.6 加工顺序的影响1.3 铝合金毛坯切削加工变形和残余应力控制研究现状1.3.1. 铝合金初始毛坯残余应力研究现状1.3.2 切削加工残余应力的研究现状1.3.3 切削加工变形的研究现状1.3.4 高速加工技术1.4 本章小结1.5 本文研究内容1.6 论文章节安排第二章 航空铝合金切削及其变形仿真2.1 金属切削变形基本理论2.2 基于Third Wave AdvantEdge的切削模型的建立2.2.1 AdvantEdge FEM软件介绍2.2.2 金属切削本构方程的建立2.3 二维正交切削加工仿真模型2.4 二维正交仿真结果2.4.1 切削力随着进给的变化情况2.4.2 切削力随切深的变化情况2.4.3 切削力随着刀具转速的变化情况2.5 工艺参数对残余应力和变形影响的研究2.5.1 切削残余应力仿真模型2.5.2 切削的残余应力导致变形的有限元模型2.5.3 切深对残余应力及变形的影响2.5.4 进给对残余应力及变形的影响2.5.5 转速对残余应力及变形的影响2.6 变切深的工步参数设计2.7 本章小结第三章 考虑残余应力作用下的薄壁件加工变形与工艺优化研究3.1 铝合金初始应力有限元模型3.1.1 毛坯初始应力3.1.2 毛坯初始应力对变形的影响3.1.3 残余应力消除办法3.2 毛坯余量去除方式的选择3.3 考虑残余应力的加工顺序优化3.3.1 不同的加工顺序对于薄壁件变形的影响3.3.2 基于残余应力仿真分析不同加工顺序对于薄壁件刚度变化的曲线3.4 走刀路径影响3.5 本章小结第四章 加工工艺实验研究4.1 切削力及表面粗糙度测试4.1.1 切削实验平台的搭建4.1.2 切削力实验测试数据4.1.3 铣削表面质量测试4.1.4 残余应力测试4.2 工艺方法实验4.2.1 走刀路径实验4.2.2 刀具直径对于变形的影响实验4.2.3 加工顺序对变形的影响实验4.3 本章小结第五章 总结和展望5.1 研究工作总结5.2 论文创新点5.3 课题研究展望参考论文在学期间的研究成果及发表论文致谢
相关论文文献
标签:薄壁件论文; 残余应力论文; 工艺优化论文; 走刀路径论文; 加工顺序论文;