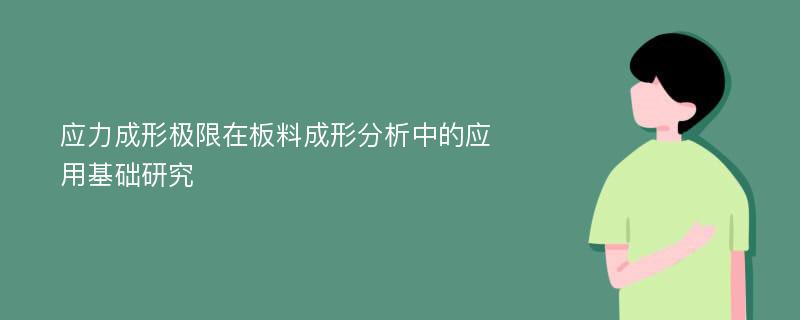
论文摘要
板料塑性成形是重要的金属成形工艺之一,在航空航天、汽车及家电制造业中有着广泛的应用,是现代制造业中不可或缺的重要组成部分。成形极限分析判据是板料塑性成形过程中判断成形能否顺利进行的依据。基于极限应变的成形极限图(Forming Limit Diagram,FLD)是目前应用最为广泛且具实用价值的成形极限判据,也是评价不同板料成形性的工具。但是,由于FLD的应变路径相关性缺陷,因此具有应变加载路径无关特性的成形极限应力图(Forming Limit Stress Diagram,FLSD),成为复杂应变加载路径条件下成形极限分析新判据的研究热点。本文针对应力成形极限应用存在的关键问题开展深入系统的研究,为FLSD的应用奠定基础。本文完成的主要工作和取得的成果如下:(1)系统分析研究了基于应变极限的成形极限图在分析板料成形极限时存在的缺陷和面临的问题,分析了基于应力极限的成形极限图(FLSD)在复杂应变路径下成形极限分析的应用前景及在应用中急需解决的关键问题,提出了采用实验研究和理论分析相结合的方法来解决FLSD应用的关键问题的方案。(2)基于塑性成形理论综述分析了与板料成形极限研究相关的屈服准则及失稳理论。对几种比较典型的各向异性屈服函数进行了对比分析研究,归纳了各自的特点及适合的应用条件,同时还对几种典型的板料拉伸失稳准则进行了比较分析。依据分散扩散失稳理论推导了单向拉伸、双向拉伸条件下的极限应变预测公式。(3)在基本理论分析的基础上,根据板料成形极限试验标准,进行了体心立方晶格类型的低碳钢板(SPCEN、DC01、DC03、08AL四种牌号)及面心立方晶格的铝合金(LF21M)三种厚度系列(s=0.8mm,1.2mm,2.1mm)的板料进行了包括线性加载路径、单向拉伸预应变、双向拉伸预应变及平面预应变等在实际生产中典型的应变路径进行了全面系统的成形极限试验研究。通过试验研究,获得了不同板料在不同应变路径条件下的FLD,并分析比较了不同应变路径、不同板厚、预应变量等条件下的FLD特性。(4)在FLD实验的基础上,推导了不同屈服准则下的应力应变转换方程,依据转换方程求得的极限应力值,构建板料成形极限应力图(FLSD),得出了不同应变路径下的FLSD、不同屈服准则下的FLSD、不同晶格类型材料的FLSD及不同预应变量下的FLSD,并对其进行了比较分析。此外,还尝试用有限元仿真方法建立板料成形FLSD的方法,为FLSD的获得提供了一条方便途径。(5)进行了应用连续损伤力学原理建立FLSD的研究。综合文献资料推导了板料损伤的拉伸失稳预测模型,在以板材密度的变化作为损伤变量,测定板材损伤变量实验的基础上,根据模型求出特征点的极限应变值,再利用应力应变转换关系得出相应的FLSD。分析比较了用损伤力学原理得出的FLD与FLSD的特性,同时还与试验方法获得的FLSD进行了相应的比较分析,得出了基于损伤力学原理的预测模型的合理性的结论,为FLSD的进一步理论预测研究开拓了思路。(6)通过分析实验研究获得的成形极限应力、应变数据与变形条件之间的关系,并结合模糊数学和神经网络理论的优点,提出了采用模糊神经网路建立FLSD预测模型的设想。以试验数据及有限元仿真数据为样本,建立了板料成形FLSD的预测模型,提供了一种建立板料成形FLSD的新方法。同时对该模型的可靠性进行了测试,测试结果表明所建立的模糊神经网络模型预测精度高,具有良好的稳定性和抗干扰能力。(7)在实验研究及理论分析基础上,基于DYNAFORM板料有限元软件环境,在国内首次开发了用于多工步板料成形的工步之间的数据传递软件模块及以FLSD为成形极限判据的软件模块,实现了板料成形的FLSD判据的有限元分析,分析结果的准确性满足实际工程应用的需要。(8)进行了以FLSD为判据的板料成形的有限元分析结果的验证性现场试验研究。利用开发的软件模块在DYNAFORM软件环境中对轿车左后悬挂架多工步成形零件以FLSD为成形极限判据进行有限元模拟分析,并对分析结果在南汽集团跃进汽车有限公司的冲压车间进行了现场的冲压验证试验。试验结果与分析结果具有很好的一致性。本文的研究结果表明:FLSD具有应变加载路径的无关性特征,利用其分析复杂应变加载路径条件下的板料成形极限分析是有效的和可靠的。本文的研究工作为以后在板料成形模拟仿真中,使用成形极限应力图替代应变成形极限图作为极限判据奠定了基础。
论文目录
摘要Abstract第一章 绪论1.1 引言1.2 成形极限判据及其在板成形分析中的作用1.2.1 板料成形极限与成形极限图1.2.2 成形极限图的建立方法1.2.3 成形极限图的应用1.3 应变成形极限判据的路径相关性缺陷及应力成形极限的提出1.3.1 应变成形极限判据的路径相关性缺陷1.3.2 应力成形极限的提出及成形极限应力图1.4 板料复杂应变路径下成形极限研究的国内外现状1.4.1 基于应变的成形极限研究的国内外现状1.4.2 基于应力的成形极限研究的国内外现状1.5 成形极限应力图研究存在的问题1.6 本文研究背景及主要研究内容1.6.1 研究背景1.6.2 主要研究内容第二章 板料塑性变形的基本理论2.1 引言2.2 材料的初始屈服准则2.2.1 材料各向同性屈服准则2.2.2 材料各向异性屈服准则2.3 应变硬化材料的强化规则与后继屈服函数2.4 塑性变形时的应力应变关系2.4.1 弹性应力应变关系2.4.2 塑性应力应变关系2.4.3 增量理论2.4.4 全量理论2.5 板材的塑性拉伸失稳理论与失稳极限应变2.5.1 Swift 分散性失稳准则2.5.2 Hill 集中性失稳准则及极限应变2.5.3 M-K 凹槽失稳准则2.6 本章小结第三章 基于试验研究的成形极限应力图的建立3.1 引言3.2 板料成形极限试验3.2.1 板料成形极限图的试验测定原理3.2.2 板料成形极限图的试验方案3.2.3 板料成形极限图的试验设备与材料3.2.4 网格印制技术设备与成形试样的网格印制3.2.5 胀形试验3.2.6 应变测量与 FLD 的建立3.3 FLD 与 FLSD 的转换3.3.1 极限应变与极限应力的转换方程推导3.3.2 FLD 转换为FLSD3.3.3 成形极限应力图FLSD 的构造3.3.4 板料 FLD 与 FLSD 的结果对比分析3.4 基于有限元仿真方法建立板料成形极限应力图3.4.1 有限元仿真建立 FLSD 的基本思路3.4.2 FEM 方法建立FLSD3.5 本章小结第四章 基于连续损伤力学原理的成形极限应力图的建立4.1 引言4.2 材料的损伤表征4.2.1 损伤变量的定义4.2.2 损伤后的有效应力4.3 损伤变量的测定4.3.1 常用损伤变量的测定原理4.3.2 以密度作为损伤变量的实验研究4.4 材料的弹塑性损伤4.4.1 应变等效假设和能量等效假设4.4.2 损伤应变能释放率4.4.3 损伤判据4.4.4 损伤演变方程4.5 基于损伤演化失稳准则的板料成形极限预测4.5.1 成形极限应变预测4.5.2 成形极限图4.5.3 成形极限应力图4.5.4 结果及分析讨论4.6 本章小结第五章 基于模糊神经网络的板料成形极限应力图预测模型研究5.1 引言5.2 模糊神经网络的基本原理5.2.1 模糊逻辑基础及模糊聚类分析5.2.2 人工神经网络基本理论概述5.2.3 模糊神经网络5.2.4 混合型 Pi—sigma 模糊神经网络模型及学习算法5.3 基于模糊神经网络的板料成形极限应力图预测模型的建立5.3.1 模糊神经网络训练数据的获得5.3.2 输入变量的区间划分与隶属函数的选取5.3.3 模糊神经网络的训练5.3.4 模糊神经网络的算法流程及其模块的程序实现5.3.5 模糊神经网络的预测结果5.4 本章小结第六章 应力成形极限判据在有限元分析中的应用6.1 引言6.2 板料成形有限元模拟方法和模拟软件的基本结构6.2.1 有限元模拟方法的处理过程6.2.2 有限元分析软件的基本结构6.2.3 板料成形过程的有限元仿真的技术路线特点6.3 板料有限元分析软件概况6.4 DYNAFORM 有限元分析软件的特点6.4.1 DYNAFORM 的结构6.4.2 DYNAFORM 非线性有限元求解格式6.4.3 DYNAFORM 求解器输出的D3plot 文件6.4.4 DYNAFORM 软件中的成形极限判据6.5 应力成形极限判据的有限元应用软件模块的设计与实现6.5.1 基本功能要求6.5.2 整体程序流程与结构6.5.3 多工步板料成形有限元分析中工步间的数据传递6.5.4 FLSD 软件模块的整体程序流程实现6.5.5 FLSD 软件模块应用实例6.6 本章小结第七章 成形极限应力图的初步应用研究7.1 引言7.2 成形极限应力图初步应用研究方案7.2.1 板料成形的加载路径特点7.2.2 成形极限应力图初步应用研究方案7.3 某型汽车底板零件的拉延成形有限元模拟分析与试验验证7.3.1 模拟方案的拟定7.3.2 成形模拟相关参数7.3.3 成形模拟分析7.3.4 现场试冲试验验证7.4 轿车左后悬挂架的拉延成形有限元模拟分析7.4.1 模拟方案的拟定7.4.2 成形模拟相关参数7.4.3 有限元模型的建立7.4.4 单步拉延成形数值模拟7.4.5 多工步拉延成形数值模拟7.5 轿车左后悬挂架的现场冲压试验分析7.6 应用效果分析7.7 本章小结第八章 总结与展望8.1 全文总结8.1.1 本文完成的主要工作8.1.2 本文的主要创新点8.2 后继研究工作展望参考文献致谢在学期间的研究成果及发表的学术论文
相关论文文献
标签:应力成形极限论文; 板料成形论文; 有限元分析论文; 模糊神经网络论文; 应变路径论文; 损伤力学论文;