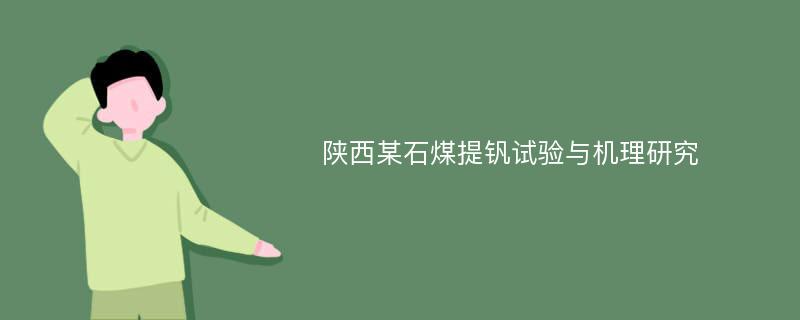
论文摘要
我国石煤提钒工艺相对比较成熟,但普遍存在着成本高、污染大、回收率低和不能大量处理等缺点,推广受到限制。因此寻求短流程、大规模、低成本、低污染的普适性新工艺用于石煤提钒与残渣的综合利用,是石煤提钒新技术未来的发展方向。新型工艺的开发研究对于减少污染,提高资源利用率具有重要意义。论文主要研究了焙烧和浸出两个阶段,重点研究了焙烧和浸出阶段影响石煤中高价钒的转化率和浸出率的因素。影响焙烧阶段钒的转化率的主要因素有:焙烧温度、焙烧时间、有机质、矿样粒度等,并对低价钒转化为高价钒的动力学过程及热力学过程进行了初步探讨;影响浸出阶段钒浸出率的主要因素有:硫酸用量、浸出温度、浸出时间以及助浸剂的用量,对浸出过程的动力学过程及热力学过程进行了深入的探讨。石煤试样含五氧化二钒0.66%、氧化硅69.21%、碳7.38%,针对该矿样的特点采用了空白氧化焙烧-酸浸工艺流程。确定了最佳焙烧工艺条件为:磨矿细度为85%-74μm,焙烧温度800℃,焙烧时间1.5小时,焙烧气氛为氧气。浸出阶段的最佳工艺参数为:硫酸用量1.2 t/t(焙砂),液固比为3:1,浸出温度为80℃,浸出时间为8小时。钒的浸出率可达到85%以上,浸出液必须通过后续的离子交换、沉钒等工艺加以除杂和提纯,浸渣可以作为石膏加以利用,实现资源的合理利用。由浸出基础理论研究中的热力学和动力学分析可知,浸出液中的钒是五价为主四价和三价伴存。根据推导的相关动力学方程,得出影响该反应的因素,在浸出过程中需降低颗粒粒度,适当提高浸出温度,以加快浸出反应的速度。该工艺的优点在于石煤原矿不必进行钠化焙烧,直接采用空白氧化焙烧-硫酸浸出工艺流程。该工艺得到钒的回收率高,且不产生有害气体和烟尘。浸出后的残渣可直接综合利用,资源利用率高,减少环境污染,同时设备投入少,操作简单。
论文目录
摘要ABSTRACT第一章 绪言1.1 前言1.2 石煤1.3 石煤提钒工艺现状1.3.1 石煤的预处理1.3.2 焙烧1.3.3 浸出1.3.4 微生物浸出技术1.3.5 溶剂萃取-反萃法1.3.6 离子交换法1.3.7 沉钒1.3.8 小结1.4 石煤提钒工艺的应用前景和今后研究重点1.5 主要研究内容1.6 论文研究的目的和意义第二章 试验样品、药剂、仪器设备及试验方法2.1 试样2.1.1 试样的制备2.1.2 原矿工艺矿物学研究2.2 试验设备及药剂2.2.1 试验设备2.2.2 试验药剂及材料2.3 试验方法2.3.1 选矿试验2.3.2 焙烧试验研究2.3.3 浸出试验研究2.3.4 焙烧过程的热力学基础理论研究2.3.5 浸出过程的热力学基础理论研究第三章 选矿试验研究3.1 磨矿细度试验研究3.2 摇床重选试验3.3 浮选脱碳试验研究第四章 焙烧试验研究4.1 焙烧温度对钒转化率的影响4.2 有机质对钒转化率的影响4.3 焙烧时间对钒转化率的影响4.4 矿石粒度对钒浸出率的影响4.5 焙烧动力学探讨4.6 焙烧研究的结论第五章 浸出试验研究5.1 酸浸探索试验5.1.1 原矿直接酸浸与选矿精矿酸浸对比试验5.1.2 酸浸是否加助浸剂试验5.1.3 硫酸用量试验5.1.4 碳质石煤对钒液的吸附试验5.2 酸浸条件试验5.2.1 四因素三水平正交试验5.2.2 方差分析5.2.3 进一步研究方向的讨论5.2.4 最佳条件下的综合酸浸试验5.2.5 高温酸浸试验5.3 后续离子交换及沉钒工艺5.3.1 离子交换工艺5.3.2 沉钒工艺第六章 焙烧过程的理论研究6.1 焙烧的基本原理6.1.1 焙烧过程的热力学计算6.1.2 焙烧过程的动力学基本原理第七章 浸出过程的理论研究7.1 浸出的基本原理7.1.1 浸出过程的热力学计算7.1.2 电势-pH图7.1.3 浸出过程的动力学7.2 硅酸盐矿物在浸出中的行为探讨第八章 石煤提钒过程的三废治理8.1 废水处理8.1.1 废水的成分8.1.2 废水处理方法8.1.3 常见的除铁方法8.2 废渣处理8.3 废气处理第九章 结论9.1 主要结论9.2 创新点致谢参考文献附录
相关论文文献
标签:石煤论文; 提取论文; 浸出论文; 焙烧论文;