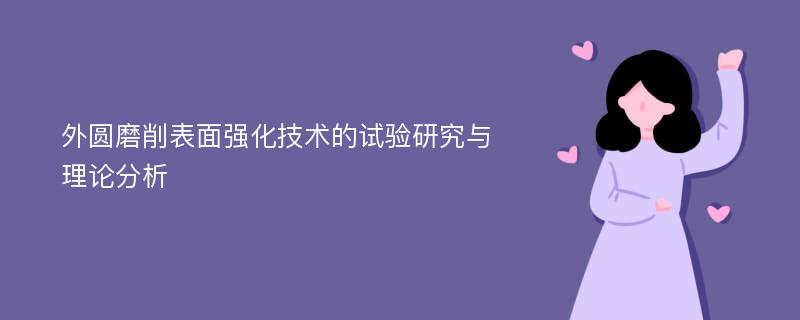
论文摘要
磨削表面强化技术利用磨削过程中生成的磨削热使工件表层温度瞬间升高到Ac3以上,然后迅速冷却,以使表层材料马氏体化。该技术集成了磨削加工工艺与表面热处理工艺,可以有效缩短产品生产周期、提高生产效率、降低制造成本,具有显著的经济价值和社会效益。本文采用了40Cr钢与45号钢两种材料进行了外圆单程切入式磨削表面强化技术的试验研究,并对强化试件进行了金相组织观测与硬度分布测量。结果表明工件表层材料的金相组织由外至内依次分为强化层、过渡层与基体三部分,组织成分分别为马氏体、马氏体与铁素体混合物、铁素体与珠光体混合物。在本试验条件下,工件表面硬度值最高为HV824.1,硬化厚度最高为1.1mm,达到了与高频淬火相同的强化效果。采用了不同的磨削深度、工件速度和砂轮特性进行外圆磨削表面强化效果的正交试验,并对硬化厚度和表面硬度两项指标进行了分析,以研究各因素对强化效果的影响程度及影响规律。结果表明,对于硬化层厚度,三项因素的影响显著程度依次为磨削深度、工件速度、砂轮特性,硬化厚度值随磨削深度增加而增大、随工件速度增加先增大后减小、采用白刚玉砂轮的硬化厚度大于铬刚玉而且小磨粒粒度号砂轮的硬化厚度大于大磨粒粒度号砂轮。对于表面硬度,仅磨削深度具有较显著影响,硬度值随磨削深度的增加而增大。在本文试验条件下采用0.4mm的磨削深度、0.5m/s的工件速度、WA46L8V砂轮进行外圆磨削表面强化,可以兼顾较深的硬化层厚度与较高的表面硬度,获得最佳的试件表面综合强化效果。对比40Cr钢与45号钢两种不同材料工件的强化效果,发现两种材料在同等的磨削参数与条件下,外圆磨削的表面强化效果与各因素的影响规律相似。但40Cr钢硬化厚度大于45号钢;45号钢的表面硬度高于40Cr钢。这种差异源于材料特性。对外圆磨削表面强化过程中砂轮二次经过的重叠强化区进行了金相观测与硬度分布测量。结果表明,该区域内经历的重叠强化过程实质上为二次淬火,其金相组织与硬度分布没有发生明显变化。砂轮退刀后工件表面上的残留热量沿砂轮移动方向继续传递,造成了重叠强化区尾部的工件表面硬度下降并伴随少量的回火索氏体出现。但由于其尺寸较小(1.0mm)而且最低硬度值HV479.6仍满足工件的硬度要求,因此对整体强化效果没有显著影响。对已强化试件进行了精磨以满足表面粗糙度与加工质量要求,并对精磨结果进行研究。结果表明,试件的金相组织与表层硬度分布并没有受到精磨过程的影响,通过合理选取磨削参数与条件,外圆磨削表面强化技术可以同时满足工件表面的硬度要求与加工精度要求。采用测力顶尖与红外测温仪,在强化试验过程中采集了磨削力与磨削温度数据,为后续的理论分析提供了依据。在此基础上,针对磨削力与磨削温度的变化规律与影响因素进行了研究。研究表明,外圆磨削表面强化中的磨削力与工件速度、磨削深度均呈现正比关系,法向分力与切向分力之比远大于普通磨削情况;而磨削温度的影响因素按显著程度依次为磨削深度、砂轮特性、工件速度,影响规律均与对硬化厚度的影响规律相同。深入研究了强化过程的切削机理,利用切削过程中的单颗磨粒能量消耗,并结合磨粒分布情况,提出了外圆磨削表面强化过程中磨削力的计算方法。在此基础上考虑了磨粒对材料的耕犁作用,以及磨粒对材料的大切深情况,使得计算结果更加准确。将磨削力的计算结果与试验中的实测值对比,发现二者具有较好的一致性。充分考虑了磨除工件材料的不同阶段,建立了外圆磨削表面强化过程的复合型热源模型与热量分配比模型。并进一步研究了磨削条件对热量分配比的影响规律。研究表明,在诸多因素中,磨粒粒度与砂轮线速度对工件表面的热量分配比影响最为显著。磨粒粒度号增大,传入工件表面的热量减少;砂轮线速度增加,传入工件表面的热量增加。采用ANSYS软件对外圆磨削表面强化过程进行了仿真。研究了强化过程中温度场的动态分布与时变情况,以及工件模型中不同位置点的温度变化情况。研究表明,磨削温度的仿真结果与测量值有较好的一致性,表明仿真结果有效可靠、建立的热源模型准确合理。在试验不便进行时,可以利用仿真方法进行研究分析。
论文目录
致谢摘要Abstract1 绪论1.1 课题的研究背景与意义(Background and Significance)1.1.1 磨削表面强化技术的提出(Source of the Subject)1.1.2 磨削表面强化技术的阶段与特点(Stages and Characteristics of Surface Grind-hardening)1.1.3 磨削表面强化技术的意义(The Significance)1.2 国内外研究现状(Research Status of the Subject)1.2.1 国外研究状况(Foreign Research States)1.2.2 国内研究状况(Domestic Research States)1.3 目前研究中的存在问题(The Present Problems)1.4 本课题的主要内容与研究方法(Main Contents and Research Methods of the Subject)2 外圆磨削表面强化试验的系统设计与试验过程2.1 试验目的(Experiment Purpose)2.2 试验方法(Experiment Approach)2.2.1 常规方法及其不足(Current Approach and the Defects)2.2.2 磨削力的测量(Measurement of Grinding Force)2.2.3 磨削温度的测量(Measurement of Grinding Temperature)2.2.4 试验系统的确定(Determination of Experiment System)2.3 试验条件(Experiment Conditions)2.3.1 工件形状与材料(Shape and Material of the Workpiece)2.3.2 试验磨床(Grinding Machine for Experiment)2.3.3 磨具磨料的选择(Grinding Tool and Abrasive)2.3.4 砂轮的静平衡与修整(Static Balance and Dressing of Wheels)2.4 试验方案的制定(Establishment of Experiment Scheme)2.5 试验过程(Experiment Process)2.6 本章小结(Chapter Summary)3 外圆磨削表面强化试验结果与研究3.1 试样的制备(Preparation of Samples)3.2 试样的金相组织观测结果与分析(Results and Analysis of Metallurgical Structure Observation)3.2.1 40Cr 钢试样金相观测结果与分析(The Observation Results and Analysis of 40Cr Steel Samples)3.2.2 45 号钢试样金相观测结果与分析(The Observation Results and Analysis of 45Steel Samples)3.3 试样的硬度测量结果与分析(Results and Analysis of Hardness Testing)3.3.1 硬度测量方法与系统(Method and System of Hardness Testing)3.3.2 硬度测量结果(Results of Hardness Testing)3.3.3 结果分析与影响因素的研究(Analysis of Results and Research of Influencing Factors)3.3.4 两种材料的强化效果对比(Comparision of Grind-hardening Effectiveness Between the Materials)3.4 磨削力及其影响因素(Grinding Force and the Influencing Factors)3.5 磨削温度及其影响因素(Grinding Temperature and the Influencing Factors)3.6 重叠强化区的强化结果分析(Analysis of Overlap Hardened Zone)3.7 精磨阶段的结果分析(Analysis of Fine Grinding Results)3.8 本章小结(Chapter Summary)4 外圆磨削表面强化过程中磨粒的切削机理研究4.1 磨粒及其分布模型(Abrasive Grains and the Distribution Model)4.1.1 工件材料的磨削过程(Removing Processes of Workpiece Material)4.1.2 磨粒的初始参量(Initial Parameters of Grains)4.1.3 磨粒分布模型(Distribution Model of Grains)4.2 单颗磨粒切削机理(Cutting Mechanism of A Single Grain)4.2.1 单颗磨粒的能量消耗(Energy Cost of A Single Grain)4.2.2 砂轮修整对磨粒的影响(Dressing Effect to Grains)4.2.3 单颗磨粒的磨削力(Grinding Force of A Single Grain)4.3 切削机理的验证(Verification of the Grain Cutting Mechanism)4.4 本章小结(Chapter Summary)5 外圆磨削表面强化过程中的磨削热模型5.1 磨削过程的热源模型(Heat Source Model of Grinding)5.1.1 热源模型的理论基础(Theoretical Basis)5.1.2 磨削热的产生(Generation of Grinding Heat)5.1.3 外圆磨削表面强化的热源模型(Heat Source Model of External Surface Grind-hardening)5.1.4 基于复合热源模型的磨削温度场(Temperature Field of Compound Heat Source Model)5.2 磨削热分配比例(Distribution Rate of Grinding Heat)5.2.1 磨削热量的传递(Conduction of Grinding Heat)5.2.2 热量分配比例模型(Model of Heat Distribution Rate)5.2.3 影响因素分析(Analysis of Influencing Factors)5.3 本章小结(Chapter Summary)6 外圆磨削表面强化过程的动态仿真研究6.1 磨削温度场的数学模型(Mathematic Model of Grinding Temperature Field)6.1.1 三类边界条件(The Three Kinds of Boundary Conditions)6.1.2 基于有限元法的仿真数学模型(Mathematic Model of Simulation Based on Finite Element Method)6.2 强化过程仿真的预处理(Pre-processing of Grind-hardening Simulation)6.2.1 边界条件的确定(Definition of Boundary Conditions)6.2.2 工件模型的建立与网格划分(Modeling and Meshing of the Workpiece)6.2.3 复合热源模型的加载(Loading of the Compound Heat Source Model)6.3 仿真结果及分析(Results and Analysis of Simulation)6.3.1 磨削温度场的动态分布(Dynamic Distribution of Grinding Temperature Field)6.3.2 单点温度的变化过程(Temperature Changing of Single Points)6.3.3 仿真结果的验证(Verification of Simulation Results)6.4 本章小结(Chapter Summary)7 结论参考文献作者简历学位论文数据集
相关论文文献
- [1].外圆磨削表面淬硬试验与动态仿真[J]. 中国机械工程 2009(23)
- [2].磨削强化中磨削用量的优化设计[J]. 机械强度 2016(03)
- [3].外圆磨削强化中的磨削力研究[J]. 制造技术与机床 2008(05)
- [4].外圆磨削强化技术及其磨削力的研究[J]. 机械设计与制造 2008(12)
- [5].40Cr钢的磨削淬硬层与磨削参数的关系[J]. 矿冶工程 2008(01)
- [6].磨削液参数对磨削强化表面微结构损伤的影响[J]. 东北大学学报(自然科学版) 2015(10)
- [7].小切深条件下磨削表面完整性变化机理[J]. 东北大学学报(自然科学版) 2012(09)
标签:磨削强化论文; 外圆磨削论文; 表面热处理论文; 磨削力论文; 磨削热论文;