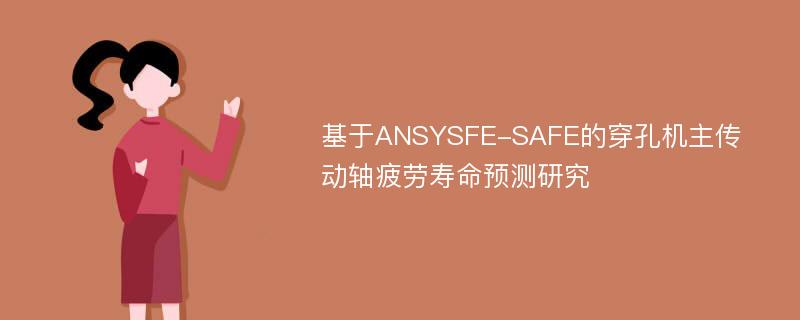
论文摘要
近些年,随着我国经济的迅猛发展,国内钢材供不应求。钢铁企业在不断扩建的同时,开足马力拼设备以追求产量最大化。在此背景下,重型轧机尤其是穿孔机的主传动轴及万向接轴断裂事故时有发生。基于上述问题,本文对某集团公司无缝穿孔机主传动轴及万向接轴的疲劳强度及疲劳寿命进行了研究。首先,使用ANSYS有限元分析软件对主传动轴和万向接进行了静强度分析。建模时采用ANSYS直接建模。根据传动轴及万向接轴的实际支撑和所受扭矩对其施加了约束和扭矩载荷。分析与讨论了主传动轴及万向接轴在920MPa扭矩载荷作用下的应力结果值和应力分布规律,同时找到了其静强度薄弱区域。更重要的是,单位载荷的静强度分析应力结果是疲劳分析的必要基础数据,它涵盖传动轴及万向接轴应力分布状况及特征。其次,疲劳强度分析另一个重要环节就是疲劳计算中使用的扭矩载荷谱。冲击扭矩载荷时间历程是影响穿孔机主传动轴及万向接轴疲劳强度及疲劳寿命的重要因素。所以,本文实测了不同工况下传动轴的扭矩载荷时间历程,并使用雨流计数法和概率统计法对实测扭矩载荷时间历程进行载荷谱编制。编制后的扭矩载荷谱更加逼近主传动轴及万向接轴的实际载荷,因此,穿孔机主传动轴及万向接轴的疲劳分析更加准确。最后,本文基于疲劳分析理论,将单位载荷静强度分析应力结果和编制的扭矩载荷谱导入ANSYS FE-SAFE疲劳分析软件中计算了主传动轴及万向接轴的疲劳强度,并预测了疲劳寿命。预测得到的穿孔机主传动轴及万向接轴的疲劳寿命与企业实际使用的主传动轴及万向接轴寿命基本相一致,证明此疲劳分析方法和疲劳寿命预测法是切实可行的。为了实时监测穿孔机主传动轴及万向接轴的扭矩载荷值并统计出造成主传动轴及万向接轴疲劳的载荷谱,更为了实时监测其疲劳交变应力及其对应的疲劳循环次数从而算出主传动轴的剩余疲劳寿命,本文设计了一套长期在线监测主传动轴扭矩载荷的扭矩传感器。由于此扭矩传感器避免了直接在传动轴上粘贴电阻应变片的诸多缺点(如,现场安装时间仓促、环境恶劣、尤其是无法实施长期牢固粘贴应变片所进行的加热与保温及密封等工艺措施)所以,其具有安装方便、测量准确、可提前标定、并可长期使用等特点。由于实验条件有限,本文没能用实验的方法标定此扭矩传感器,而是使用ANSYS软件对其进行静力学分析,得出其应力应变关系与实测应力应变数值相一致的结论,证明其设计合理。
论文目录
摘要Abstract引言1 绪论1.1 国内外穿孔机主传动轴疲劳研究的历史及现状1.1.1 国外穿孔机主传动轴疲劳研究的历史及现状1.1.2 国内穿孔机主传动轴疲劳研究的历史及现状1.2 课题研究内容和方法1.3 课题研究的目的和意义及创新点2 疲劳分析理论基础2.1 疲劳概述2.2 金属疲劳的破坏机理2.3 疲劳累积损伤理论2.3.1 线性疲劳累积损伤理论2.3.2 双线性疲劳累积损伤理论2.3.3 非线性疲劳累积损伤理论2.4 疲劳寿命分析的方法2.4.1 局部应力应变法2.4.2 名义应力法2.4.3 场强法2.5 影响传动轴疲劳强度的因素2.5.1 应力集中的影响2.5.2 尺寸效应的影响2.5.3 表面状态的影响2.5.4 使用条件的影响2.6 本章小结3 穿孔机主传动轴静强度分析3.1 有限元法理论3.1.1 有限元法的基本思想和数理概念3.2 穿孔机主传动轴静强度分析3.2.1 主传动轴及万向接轴建模及网格划分3.2.2 万向接轴接触定义3.2.3 主传动轴及万向接轴约束和荷载施加3.2.4 有限元结果及结果分析3.3 本章小结4 实测穿孔机主传动轴扭矩载荷与载荷谱编制4.1 实测传动轴扭矩载荷时间历程4.2 扭矩载荷谱编制4.2.1 编制载荷谱的要求4.2.2 载荷谱编制的基本理论4.2.3 疲劳破环的累积损伤法4.3 载荷谱编制过程4.3.1 随机载荷的统计处理4.3.2 载荷谱编制4.3.3 穿孔机主传动轴实测载荷时间历程的编制4.4 本章小结5 传动轴疲劳寿命预测5.1 ANSYS FE-SAFE 软件介绍5.1.1 ANSYS FE-SAFE 功能介绍5.1.2 软件使用流程5.2 传动轴疲劳寿命预测5.2.1 关于寿命预测方法的一般要求5.2.2 寿命预测方法分类5.2.3 随机载荷作用下的疲劳寿命估算5.2.4 材料疲劳性能参数5.2.5 载荷谱导入5.3 疲劳寿命计算结果及分析5.3.1 寿命计算5.3.2 寿命结果分析5.4 本章小结6 传动轴扭矩实时监测与寿命估计6.1 传动轴扭矩测量6.1.1 传感器设计6.1.2 传感器载体的有限元分析6.1.3 传感器的标定6.2 传动轴扭矩实时监测与寿命估计6.3 本章小结结论参考文献在学研究成果致谢
相关论文文献
标签:传动轴论文; 疲劳寿命论文; 扭矩传感器论文;
基于ANSYSFE-SAFE的穿孔机主传动轴疲劳寿命预测研究
下载Doc文档