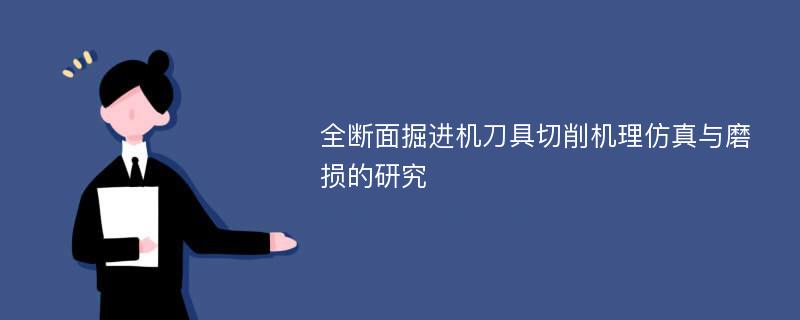
论文摘要
全断面掘进机是一种集光、机、电、液、传感、信息技术于一体的专用隧道掘进机械。刀盘和刀具是全断面掘进机最关键的工作部件。在全断面掘进机掘进过程中,刀盘刀具直接与岩土接触并构成一个完整的切削系统,主要起到开挖岩土的作用。全断面掘进机在复杂的地质条件下施工时,工况极其复杂,刀盘刀具磨损严重,开舱换刀频繁,加大了施工风险和工程费用。因此,对盾构机刀具的切削机理及其磨损情况进行研究,并根据工程实际提出适当的刀具磨损模型,对预测复杂地质条件下刀具的寿命是十分必要的。本文首先利用ABAQUS软件分别对切刀切削粘土和软岩进行了有限元仿真,得出了切深和安装前角对切削力的影响。从粘土和岩石的第一主应力和塑性变形的分布以及变化情况出发,分析了粘土和软岩两种材料失效机理的异同。文章在线切割实验的基础上,对盘形滚刀破岩进行了仿真研究。分别对一定刀间距时和单刀破岩时的仿真结果进行分析,得出了切深与滚刀受力之间的关系、滚刀刃形对受力的影响以及磨损对受力的影响。从岩石破碎面的等效应力以及剪切应力的分布特点出发,对岩石的破碎机理进行了分析。对于滚刀的表面力学性能,主要分析了滚刀破岩过程中,破岩点的应力变化以及接触区域接触压强与切削参数的关系,为研究滚刀磨损奠定了一定的基础。针对刀具的磨损问题,本文对刀具的磨粒磨损进行了有限元仿真,分析了磨损过程中刀具表面金属的应力分布和塑性变形情况。基于滚刀的破岩弧长,对滚刀磨损与刀具参数及破岩参数之间的关系进行了一系列的研究,得出了切深、滚刀直径以及刀间距与磨损之间的关系。文章采用刀具布置的等寿命原则对某土压平衡盾构刀盘不同安装半径处切刀的安装数量进行了优化。并讨论了刀盘辐条数量和刀具宽度对刀盘上切刀的布置数量和磨损的影响。基于滚刀破岩比能理论对滚刀刀间距进行了优化,并研究了刀盘上滚刀的布置规律,在此基础上,对某泥水平衡刀盘上滚刀的布置进行了改进,为刀盘的设计和施工参数的选择提供适当的参考。
论文目录
摘要Abstract目录第1章 绪论1.1 课题研究的背景及意义1.2 全断面掘进机刀具介绍1.2.1 全断面掘进机切削刀具1.2.2 盘形滚刀1.3 全断面掘进机刀具工作机理的研究现状1.3.1 切削刀具工作机理的研究1.3.2 滚刀具破岩机理的研究现状1.4 课题来源及论文的研究内容1.4.1 课题来源1.4.2 论文的研究内容第2章 切刀切削机理仿真研究2.1 切刀切削岩土的力学模型2.1.1 切刀切削软土的力学模型2.1.2 切刀切削软岩的力学模型2.2 ABAQUS中的Drucker-Prager本构模型2.2.1 ABAQUS软件简介2.2.2 Drucker-Prager本构模型2.3 切刀切削岩上的仿真研2.3.1 切刀切削粘土仿真2.3.2 切刀切削软岩仿真2.3.3 粘上和软岩切削机理比较2.4 本章小结第3章 盘形滚刀破岩机理仿真研究3.1 盘形滚刀的破岩机理及力学模型3.1.1 盘形滚刀的破岩机理3.1.2 盘形滚刀破岩受力的预测模型3.2 盘形滚刀破岩仿真3.2.1 线切割实验3.2.2 基于线切割实验的盘形滚刀破岩仿真3.2.3 滚刀破岩机理仿真分析3.2.4 滚刀表面力学性能分析3.3 本章小结第4章 全断面掘进机刀具磨损机理研究4.1 盾构刀具切削岩土过程中的磨损机理分析4.1.1 材料磨损的基础理论4.1.2 盾构刀具磨损过程分析及影响因素4.2 盾构刀具磨粒磨损仿真研究4.2.1 仿真模型与算法4.2.2 仿真结果分析4.3 基于破岩弧长的盘形滚刀磨损研究4.3.1 盘形滚刀破岩轨迹的计算4.3.2 盘形滚刀磨损的计算4.4 本章小结第5章 全断面掘进机切刀的布置规律研究5.1 切削刀具布置的原则5.1.1 切刀的布置曲线5.1.2 刀盘上切刀的布置数量5.2 基于等寿命原则的某盾构刀盘刀具安装数量的优化5.2.1 原刀盘刀具布置5.2.2 刀具数量的优化5.3 刀盘辐条数量和刀宽对刀具布置的影响5.3.1 刀盘辐条数量对刀具布置的影响5.3.2 刀宽对刀具布置的影响5.4 本章小结第6章 滚刀刀间距优化及其布置方法研究6.1 基于比能的滚刀刀间距优化6.1.1 临界刀间距的确定原则6.1.2 滚刀破岩的比能理论6.1.3 岩石破碎面积的计算6.1.4 滚刀破岩刀间距的优化6.2 滚刀的布置原则6.2.1 盘形滚刀所受的外力6.2.2 刀盘的力学平衡方程6.3 某泥水平衡盾构刀盘滚刀布置优化6.3.1 原刀盘滚刀布置参数介绍6.3.2 刀盘滚刀布置优化6.4 本章小结第7章 结论与展望7.1 结论7.2 展望参考文献致谢
相关论文文献
标签:全断面掘进机刀具论文; 切削机理论文; 仿真论文; 磨损论文; 布置规律论文;