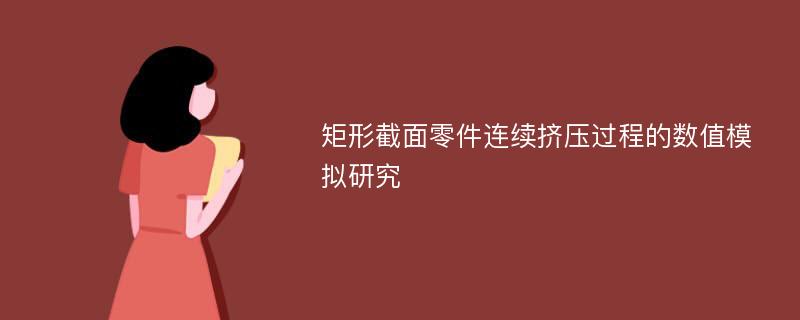
论文摘要
连续挤压利用挤压轮和压下轮的摩擦力,将金属坯料源源不断地拽入挤压通道,并最终从挤压模口处流出而成为零件。整个生产过程属于无间断连续成形,且将摩擦力作为变形的驱动力,避免了在常规塑性成形中摩擦的有害作用,具有生产效率高、节能效果强,且制件成形质量好等优点,因此在线材、管材及包覆材料成形等方面得到了广泛的应用。但由于连续挤压变形过程的复杂性,若工艺参数和模具型腔尺寸选择不当,则容易造成挤压产品的质量问题。为此,本文针对矩形截面铝母线,采用数值模拟的方法,对其连续挤压过程中的变形流动规律进行研究,为工艺及模具的设计奠定理论基础。针对连续挤压的变形特点,本文将连续挤压变形过程划分为轧制、弯曲、挤压和挤出四个阶段。然后,借助有限元分析软件对矩形截面铝母线的连续挤压变形过程进行了数值模拟,获得了坯料在各阶段的变形信息,以及挤压通道的填充情况。同时,为了掌握挤压轮槽不同位置处坯料从非稳态到稳态的变形历史及轮槽填充的变化过程,本文还通过节点追踪、截面分析及挤压轮扭矩分析等方法,实现了对坯料总体变形流动规律的把握。研究结果表明:坯料脱离压下轮后,在挤压轮槽摩擦力的作用下将产生弯曲,并与轮槽底部脱离,从而造成该处的压应力和摩擦力消失;坯料在挤压通道内的填充分布不均匀,靠槽封块一侧填充较满,靠挤压轮一侧填充较差,这种差别在靠近堵头位置处更为明显;坯料接触堵头后,堵头附近金属在挤压轮摩擦力作用下将产生镦粗,使得坯料与挤压轮的接触面积及接触压力迅速上升,并在模口附近形成了一条剪切变形带,但堵头及模口变形阻力的影响范围仅局限在堵头及模口附近区域;当坯料流过模具减径带时,由于速度分布不均,使得坯料有向上偏转的运动趋势,但随后该趋势在定径带的作用下被逐渐削弱并最终消失。
论文目录
摘要ABSTRACT第一章 绪论1.1 引言1.2 连续挤压工作原理1.3 连续挤压的工艺特点及其优势1.4 连续挤压技术国内外研究概况1.4.1 连续挤压技术国内外应用概况1.4.2 连续挤压理论和实验研究概况1.4.3 连续挤压数值模拟研究概况1.5 连续挤压的发展趋势1.6 主要研究内容第二章 数值模拟过程中若干技术问题的处理2.1 模具和坯料的几何建模2.2 模具和坯料的材料模型2.3 网格划分及畸变网格重划2.3.1 网格划分2.3.2 网格重划的判据2.3.3 频繁网格重划的防止措施2.4 摩擦模型的选取2.5 数值模拟过程中体积损失的处理2.5.1 体积损失的影响因素2.5.2 体积损失的处理2.6 模具运动条件的设置及动态边界条件的处理2.7 迭代方法及时间步长的确定2.8 本章小结第三章 变形阶段的划分及总体研究思路3.1 变形阶段的划分3.2 总体研究思路3.3 本章小结第四章 连续挤压变形前期的金属流动规律4.1 模拟条件4.1.1 坯料和模具的几何模型4.1.2 坯料和模具材料模型4.1.3 模具运动情况及工艺参数的确定4.2 轧制阶段的变形过程4.2.1 坯料与轮槽表面的接触情况4.2.2 等效应变分布4.2.3 等效应变速率分布4.3 弯曲阶段的变形过程4.3.1 坯料与轮槽表面的接触情况4.3.2 等效应变分布4.4 挤压阶段的变形过程4.4.1 坯料与轮槽表面的接触情况4.4.2 等效应变分布4.5 本章小结第五章 挤出阶段的变形特征5.1 坯料与轮槽及模具表面的接触情况5.2 速度场分布5.3 等效应变速率分布5.4 等效应变分布5.5 本章小结第六章 轮槽不同位置处的变形和填充历史6.1 挤压轮扭矩曲线6.2 坯料流动前沿追踪6.3 轮槽横截面上的填充过程6.4 坯料横截面上等效应变的分布及变化特点6.5 本章小结结论参考文献致谢个人简历攻读硕士学位期间发表的学术论文
相关论文文献
标签:连续挤压论文; 数值模拟论文; 变形规律论文; 变形阶段论文; 截面分析论文;