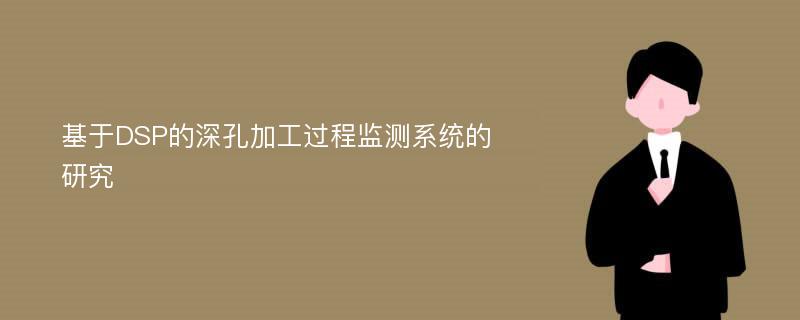
论文摘要
深孔加工是机械加工中的一个重要分支,随着深孔加工自动化技术的日益发展,研究深孔加工过程中刀具磨损和排屑状态的实时监测具有十分重要的实际意义。本文以BTA深孔钻床为研究对象,针对深孔加工过程的特点,提取了功率和油压作为监测信号,建立了基于DSP的深孔钻削过程刀具磨损与排屑状态的在线实时监测系统。根据监测系统的实时性需要,采用TMS320F2812 DSP芯片作为监测系统硬件平台的中央处理单元,完成了实时监测系统硬件设计,该系统能够实现工况信号采集、分析以及工况识别等功能,通过串行接口可以将采集的信号传输到计算机上做进一步分析和处理。监测系统的硬件采用模块化设计,监测系统的硬件模块包括:时钟电路、电源电路、复位电路、存储器设计、数据采集电路、串行通信和仿真接口。在CCS集成开发环境下,完成了监测系统的基本配置。针对BTA系统的复杂性以及油压信号和功率信号的非平稳性,采用自适应噪声抵消消噪思想来实现油压信号和功率信号中的背景噪声的消噪。讨论了自适应噪声的原理,给出了消噪算法,并以机床空载时的油压和功率信号作为自适应滤波器的参考信号对加工时的油压信号和功率信号进行了消噪实验,结果表明使用该方法具有很好的非平稳随机噪声消噪效果,为监测信号特征的提取奠定了基础。根据油压信号时域特征与排屑状态之间的密切联系,提取了油压信号的峰值、方差、峰值因子、脉冲因子和油压变化率五种特征参数作为油压信号的特征向量来判断深孔钻削过程中排屑状态;对刀具磨损的监测采用功率信号各频段的细节信号能量、二阶累积量、三阶累积量、四阶累积量和双谱在敏感频段的能量七种特征参数作为功率信号的特征向量来判断刀具的磨损状态。针对特征向量与工况之间关系的复杂性与不确定性,采用模糊识别的思想建立了深孔钻削过程排屑与刀具状态的模糊C均值识别方法,实验结果表明该方法能够准确地识别深孔钻削过程中的的排屑状态和刀具磨损状态。
论文目录
摘要Abstract1 绪论1.1 课题来源及其研究意义1.2 国内外实时监测方面的研究现状1.3 实时监测技术存在的问题与发展趋势1.4 本文主要研究内容2 BTA深孔钻削过程状态监测系统的方案建立2.1 BTA深孔钻床的原理与构成2.1.1 BTA深孔钻床的原理2.1.2 BTA深孔钻床的构成2.2 深孔钻削中的常见故障及工况信号分析2.2.1 深孔钻削中的常见故障2.2.2 工况信号分析2.3 深孔钻削过程状态监测系统的建立2.3.1 功率监测法2.3.2 油压监测法2.3.3 基于DSP的深孔钻削状态监测系统2.4 本章小结3 DSP监测系统的硬件组成3.1 TMS320F2812简介3.2 DSP监测系统的硬件电路3.2.1 时钟电路模块设计3.2.2 电源电路模块设计3.2.3 复位电路模块3.2.4 存储器模块设计3.2.5 数据采集电路模块设计3.2.6 串行通信模块设计3.2.7 仿真接口模块3.3 本章小结4 深孔加工过程监测的系统程序4.1 CCS简介4.1.1 CCS代码生成工具4.1.2 CCS集成开发环境4.1.3 COFF公共目标文件格式4.2 监测的系统程序开发4.2.1 系统初始化模块4.2.2 中断向量4.2.3 系统启动的引导模式4.3 数据采集模块软件4.3.1 初始化ADC寄存器4.3.2 事件管理器模块4.4 串行通信4.5 本章小结5 深孔加工过程中的状态监测信号自适应消噪5.1 自适应噪声抵消技术5.1.1 自适应滤波5.1.2 自适应噪声抵消5.1.3 自适应滤波器算法5.2 仿真信号的自适应消噪5.3 监测信号的自适应消噪5.3.1 油压信号自适应消噪5.3.2 功率信号自适应消噪5.4 本章小结6 BTA深孔钻削排屑与刀具状态的模糊识别6.1 模糊C均值(FCM)聚类算法6.1.1 模糊划分6.1.2 数据标准化6.1.3 FCM算法6.2 油压信号的FCM聚类6.2.1 油压信号的特征参数6.2.2 油压信号的FCM模糊识别6.3 功率信号的FCM聚类6.3.1 功率信号的特征参数6.3.2 功率信号的FCM模糊识别6.4 本章小结7 结论与展望7.1 结论7.2 发展与展望致谢参考文献攻读硕士学位期间发表论文及参与项目
相关论文文献
标签:深孔钻削论文; 数字信号处理论文; 实时监测论文; 自适应噪声抵消论文; 模糊均值论文;