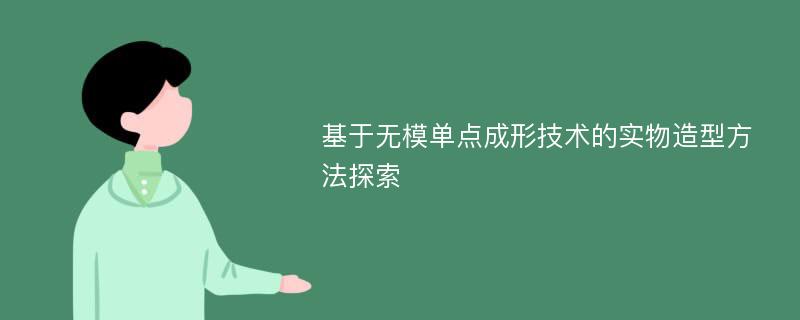
论文摘要
板壳类三维曲面成形是国内外长期以来研究的一个课题,有旋压成形、数控锤成形、多点成形和数控单点成形等。这些成形方法都是面向制造的工艺手段。而快速成型技术的出现,为机械产品设计和工业造型设计提供了一种全新的设计方法。本课题正是基于这样一种理念,提出了一种面向设计的基于主从式异构输入输出系统和单点渐进成形技术的薄壳类曲面成形方法。单点渐进成形是在数控机床上通过计算机程序控制形状简单的成形工具,利用其运动轨迹对金属板料进行连续局部塑性成形的加工方法,在板类零件成形领域有着广泛的应用前景。该成形方法涉及到塑性力学、数控技术、计算机技术,采用了“降维”的思想,将一个物理实体的制造由复杂的三维成形离散成一系列简单的二维层进行加工本文着重探讨单点渐进成形工艺对板料塑性成形质量的影响。总结了国内外关于单点渐进成形的研究现状;对单点渐进成形机理进行了分析,建立了成形过程的数学模型;探讨了成形轨迹的设计原则,实现了较为理想的无模单点渐进成形。本文探讨了无模单点渐进成形的成形过程以及力学模型,采用显式动力有限元方法—LS—DYNA软件对板料单点渐进成形过程进行了数值模拟研究。研究了工艺参数对单点渐进成形过程的影响,包括成形工具球头半径、垂直进给量、水平进给速度和摩擦条件,为进行单点渐进成形实验作了大量的准备工作。分析了数值模拟结果的板料成形性能,探讨了成形过程中拉裂、起皱等缺陷产生的原因及抑制方法,分析了在单点渐进成形过程中“层”变形特点包括板料不同区域的应变历史以及厚度变化趋势。研究工作表明,用有限元方法对单点渐进成形过程进行数值模拟,可以为单点渐进成形工艺参数的确定和成形性的判断提供重要依据。本文最后初步探索了基于带力反馈的主从式异构输入输出装置和单点成形系统的曲面造型技术,包括空间坐标映射和曲面加工轨迹几何定义,提出了基于无模单点成形技术的交互式薄壳曲面造型方法。
论文目录
摘要ABSTRACT第1章 绪论1.1 课题来源1.2 板料成形方法简介1.3 单点成形技术的国内外现状1.3.1 渐进成形原理1.3.2 半模单点成形1.3.3 无模单点成形1.4 板料成形的数值模拟现状1.4.1 板成形数值模拟发展及算法简介1.4.2 板成形数值模拟软件的应用1.4.3 数值模拟软件LS-DYNA及其功能简介1.5 面向实物的交互式操作的研究现状1.6 选题意义和研究内容1.6.1 选题意义1.6.2 主要研究内容1.7 小结第2章 单点成形成型机理分析2.1 前言2.1.1 最小阻力定律2.1.2 失稳理论2.2 单点成形的应力应变状态2.2.1 古布金应力应变状态2.2.2 单点成形过程的应力应变分布2.3 单点成形过程的数学模型2.3.1 厚度分析与减薄率计算2.3.2 成形力计算2.4 单点渐进成形的特点2.5 小结第3章 单点成形试验装置本体设计3.1 前言3.2 试验相关参数的预测3.2.1 成形力预测及加工板材参数选择3.2.2 工具头速度预测3.3 试验材料准备3.4 试验装置总体设计框架3.5 试验装置主要部分参数设计3.5.1 提高试验样机的结构刚度3.5.2 提高样机结构的抗振性3.5.3 减小运动件的摩擦和消除间隙3.6 输入装置设计3.7 定标器设计3.8 进给伺服系统设计3.9 小结第4章 成形过程实验4.1 前言4.2 厚度和减薄率分析4.3 起皱和表面质量分析4.4 回弹和轮廓精度分析4.4.1 回弹机理分析4.4.2 试验结果4.4.3 回弹控制方案4.5 小结第5章 成形过程数值模拟5.1 前言5.2 有限元模型建立5.2.1 本构方程和材料模型5.2.2 数值分析方法选择5.2.3 有限元模型的建立5.2.4 接触算法5.2.5 边界条件和加载方式5.2.6 成形工艺参数5.3 厚度和减薄率分析5.4 起皱和表面质量分析5.5 成形力分析5.6 回弹和轮廓精度分析5.7 小结第6章 实物造型方法的初步探索6.1 前言6.2 空间坐标映射6.2.1 总体坐标系6.2.2 系统原点6.2.3 工件坐标系6.2.4 手控器坐标系6.2.5 定标器坐标系6.2.6 空间坐标映射6.3 工具头轨迹定义6.3.1 工件曲面参考坐标系的定义6.3.2 工具头加工轨迹的确定6.4 曲面实物造型的简单实验6.5 实物造型的优越性6.6 小结第7章 总结和展望参考文献攻读硕士学位期间的其他研究工作致谢
相关论文文献
标签:单点渐进成形论文; 成形机理论文; 工艺参数论文; 主从异构论文; 坐标映射论文; 实物造型论文;