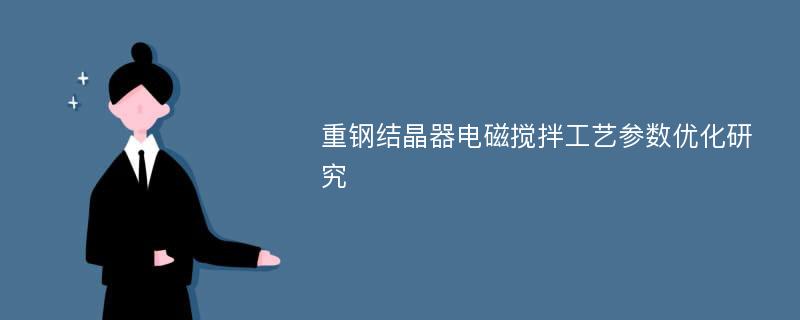
论文摘要
电磁搅拌是将电磁能转换为钢水的旋转动力,推动钢水旋转运动,实现对钢水凝固组织、结晶状态、夹杂物、皮下气泡、晶间及中心偏析的有效控制,从而提高连铸坯质量。重钢炼钢厂在1#、5#方坯连铸机上采用了结晶器电磁搅拌技术,电磁搅拌工艺参数的设定,主要来源于电磁搅拌技术提供厂家,随着1#、5#铸机生产的品种数量增加,产量扩大,拉速提高,电磁搅拌工艺参数如何与连铸工艺相配合,更好地满足铸坯质量要求,有待进一步研究。该项目在对现150mm×150mm、150mm×210mm两断面磁感应强度实测的基础上,分析了保证代表类钢种浇注所须的电磁搅拌工艺参数范围,并通过现场工业性试验,优化出了为保证铸坯皮下质量、合理的结晶组织的优化工艺参数,研究结果为重钢结晶器电磁搅拌技术的合理应用提供了理论及实践基础。对重钢两断面电磁搅拌磁场测试结果表明,两个断面的磁感应强度最大值均位于距结晶器上口H=500mm位置,即结晶器中心位置附近。在距结晶器顶端100mm(弯月面处),两个断面的磁感应强度均<50 Gs,搅拌电流及频率的变化,对其影响微弱。150mm×210mm断面在结晶器的上半部,对应的磁感应强度增加趋势大于150mm×150mm小断面,在离顶端200mm处,即距弯月面下100 mm位置,150mm×210mm断面的磁感应强度可以达到400Gs左右,150mm×150mm断面在离顶端300mm处磁感应强度仅为150Gs。结晶器壁面处磁感应强度值略大于对应中心处的值,随磁感应强度的增大,差值也在增大。两个断面获得最大电磁力的频率匀为4Hz。研究利用数值模拟分析了电磁力场作用下流体速度场的分布特征。通过在重钢生产现场对不同电磁搅拌工艺参数条件下的铸坯质量分析得出,在电流频率为4Hz条件下,代表钢种优化工艺参数为:70钢合适电流为360A;40Cr、45A的电流为320A; 20CrMnTi的最佳电流应在280A; AM3钢的电流应控制在230A。
论文目录
摘要ABSTRACT1 绪论1.1 连铸技术发展概述1.1.1 国外连铸技术发展概述1.1.2 国内连铸技术发展概述1.2 结晶器在连铸生产中的作用和地位1.3 电磁搅拌技术1.3.1 电磁搅拌技术的发展历史1.3.2 电磁搅拌的原理1.3.3 结晶器内电磁搅拌过程的理论解析1.3.4 电磁搅拌种类与冶金效果1.4 课题研究的目的意义及主要内容1.4.1 课题研究的目的意义1.4.2 研究内容1.5 本章小结2 结晶器电磁搅拌磁感应强度测试与分析2.1 测试实验方案2.2 测试结果与分析2.2.1 结晶器高度方向上磁感应强度分布特征2.2.2 结晶器壁面与中心位置磁感应强度比较2.2.3 电流与磁感应强度的关系2.2.4 频率与磁感应强度的关系2.2.5 结晶器高度方向上电磁搅拌力分布特征2.2.6 搅拌频率的确定2.3 本章小结3 电磁搅拌条件下结晶器内流体流动特征3.1 无电磁搅拌时结晶器内钢液流动的数学模型3.1.1 基本方程3.1.2 数学模型基本方程的边界条件3.2 有电磁搅拌时结晶器内钢液流动的数学模型3.2.1 基本方程3.2.2 边界条件INLET)与入口湍动能的计算'>3.3 水口入口速度(VINLET)与入口湍动能的计算3.4 连铸结晶器电磁搅拌过程计算机模拟3.4.1 FLUENT 程序的结构3.4.2 FLUENT 求解步骤3.4.3 有限体积法3.5 流场模拟计算结果与分析3.5.1 方坯结晶器内钢液流场的基本特征3.5.2 EMS 下结晶器内速度场特征3.5.3 有无EMS 时结晶器纵向中心对称面的速度场特征比较3.5.4 结晶器内不同横断面流场分布特点3.5.5 电流强度与搅拌速度的关系3.5.6 施加EMS 时不同断面横断面流场特征比较3.5.7 EMS 对液面扰动的影响3.6 本章小结4 电磁搅拌工艺参数优化工业性实验4.1 现行搅拌工艺参数评价4.2 电磁搅拌工艺参数优化方案的建立4.3 MEMS 参数优化铸坯质量检验方法4.3.1 实验钢种特点及其与质量关系的分析4.3.2 铸坯质量检测方法4.4 MEMS 优化实验结果及分析4.4.1 实验条件4.4.2 铸坯低倍检验结果4.5 结果分析4.5.1 电磁搅拌电流与中心疏松的关系4.5.2 搅拌电流对中心缩孔的影响4.5.3 搅拌电流对方坯凝固组织的影响4.5.4 搅拌电流对中心偏析的影响4.5.5 搅拌电流对铸坯非金属夹杂的影响4.6 小结5 结论致谢参考文献
相关论文文献
标签:结晶器论文; 电磁搅拌论文; 铸坯质量论文;