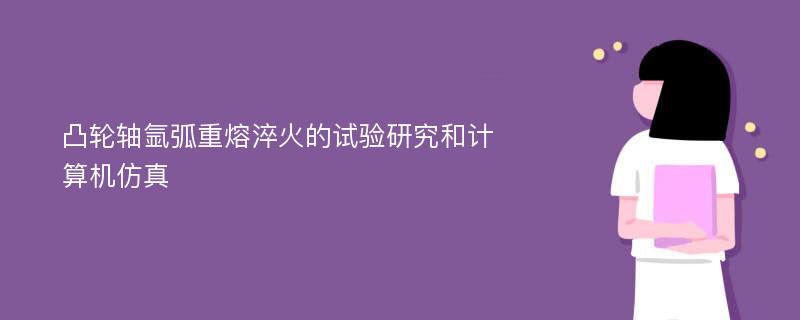
论文摘要
钨极氩弧重熔淬火技术在显著提高发动机铸件表面硬度和耐磨性的同时,也存在值得研究和亟待解决的工艺缺陷和难点。本文运用计算机仿真和温度测试方法并结合传热学和材料学基本理论,提出改进凸轮轴重熔淬火硬化技术的具体工艺优化方案和技术改进措施。 本文在所建立的凸轮轴重熔淬火温度模型基础上,利用Matlab工程软件计算得到凸轮表面淬火区域中具有代表性的点的热循环曲线和淬火表面局部温度分布,并通过改变模型参量得到主要工艺参数对重熔淬火温度变化的影响趋势,以此来验证传热学理论对分析淬火过程的指导作用。 结合淬火温度计算机仿真,利用红外测温设备对重熔淬火预热区温度和重熔区冷却温度作测试研究。重点论述了重熔淬火实测温度中的技术难点、温度定标、测试步骤和方法。受实际重熔淬火时的高温弧光和工件旋转以及具体设备工况条件限制,从对凸轮轴重熔淬火工艺缺陷所作的理论研究进行补充的角度出发,对利用红外测温仪测得的凸轮表面冷却温度数据作冷却温度变化率的趋势分析和对温度数据作溯源处理,得到近似真实淬火温度值,为研究凸轮轴重熔硬化技术提供了新的手段。 结合温度计算机仿真结果和实际测试结果,进一步通过对重熔工艺参数间关系的梳理,得到重熔电流强度、重熔热量、重熔速度、保护气体流量与预热温度等关键工艺参数间的内在联系;通过定性研究工艺参数对熔池熔深和熔宽的影响、金相组织对淬火质量的影响,得出造成重熔淬火工艺缺陷的本质原因。 在此基础上,依据生产实际情况,本文从改进淬火参数、调整金相参数和优化设备参数三方面对凸轮轴钨极氩弧重熔淬火技术提出了较为具体的工艺优化和技术改进方案,其中主要是在可调范围内对工艺参数提出具体的改进意见,并最大限度地把主要工艺缺陷综合起来考虑,以求得事半功倍的理想效果。
论文目录
摘要ABSTRACT第1章 绪论1.1 研究课题的来源和背景1.2 国内外研究的历史和现状1.3 课题研究的内容和技术方案第2章 凸轮轴氩弧重熔淬火技术研究2.1 凸轮轴表面硬化处理技术2.2 凸轮轴氩弧重熔淬火机理分析2.3 凸轮轴重熔淬火工艺缺陷和技术难点2.3.1 重熔淬火主要质量缺陷2.3.2 重熔淬火工艺改进中的技术难点2.3.3 重熔淬火工艺改进与淬火温度场的关系第3章 凸轮轴重熔淬火温度测试和分析3.1 常用温度测试方法的比较3.2 重熔淬火温度测试要求和技术难点3.3 红外测温原理和温度定标3.3.1 红外测温原理3.3.2 重熔淬火测试温度的标定3.4 凸轮轴重熔淬火温度测试方案和步骤3.4.1 测试设备和仪器3.4.2 具体测试步骤3.5 温度测试结果分析3.5.1 预热温度测试结果分析3.5.2 淬火区局部温度测试结果分析3.5.3 凸轮淬火区温度溯源计算第4章 凸轮轴氩弧重熔淬火温度计算机仿真4.1 凸轮轴氩弧重熔淬火温度数值模型的建立4.1.1 凸轮轴重熔淬火温度数值计算模型4.1.2 凸轮轴重熔淬火温度数值计算模型修正4.2 凸轮轴重熔淬火温度的计算机仿真4.2.1 计算机仿真的参数设定4.2.2 凸轮轴重熔淬火温度热循环曲线4.2.3 凸轮轴重熔淬火局部温度场4.2.4 热流密度对淬火温度分布的影响4.2.5 重熔速度对淬火温度分布的影响第5章 凸轮轴重熔淬火参数研究和工艺优化5.1 重熔淬火工艺参数关系研究5.1.1 重熔电流与电弧热量的关系5.1.2 重熔速度与工件线热量的关系5.1.3 淬火预热温度的研究5.1.4 保护气体流量的研究5.2 重熔淬火主要工艺参数与重熔质量关系研究5.2.1 重熔淬火主要工艺参数与熔池特性的关系5.2.2 重熔淬火主要工艺参数与重熔层特性的关系5.3 凸轮轴金相组织参数研究5.3.1 凸轮轴毛坯金相组织分析5.3.2 合金元素对铸铁金相组织的作用5.4 凸轮轴重熔淬火工艺缺陷分析5.4.1 淬火表面缩孔缺陷的研究5.4.2 淬火表面石墨析出的研究5.4.3 其他质量缺陷的研究5.5 重熔淬火主要工艺参数的调整优化5.5.1 重熔电流相位与转角的校正5.5.2 重熔电流衰减速率的调整5.5.3 预热温度与凸轮淬火工步的优化5.5.4 其他辅助工艺参数的优化5.6 凸轮轴金相组织参数的优化5.7 凸轮轴淬火工艺设备的调整和改进5.7.1 钨极棒的修磨和提高耐用度5.7.2 淬火凸轮塌边缺陷的消减5.8 本章小结第6章 总结和课题展望6.1 总结6.2 重熔淬火硬化技术的展望致谢参考文献个人简历 在读期间发表的学术论文与研究成果
相关论文文献
标签:计算机仿真论文; 温度测试论文; 工艺参数论文; 金相结构论文; 缺陷论文; 优化论文;