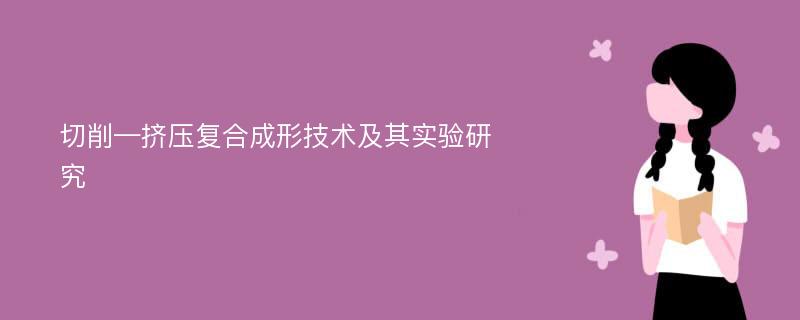
论文摘要
翅片管在工业生产中有着广泛的应用,如何获得具有良好传热特性的翅片结构是工程界广泛关注的问题。本文提出了一种利用普通机床和特殊刃磨的刀具,通过对切削用量和刀具几何参数的精确匹配,使传统切削加工中的切屑翻转、变形并竖立在基体上而形成螺旋式整体翅片结构,具有切削和挤压特性的复合成形新技术。以圆翅片管和平面翅片结构为对象,研究了切削-挤压复合成形过程的运动关系和刀具结构特点,获得了成形过程原理和几何模型。以此为基础,提出了把切削-挤压成形过程分为切削、挤压翻转、弯曲成形三个阶段的观点,建立了翅片结构尺寸与工艺参数之间的理论计算公式。分析了影响翅片结构和尺寸的因素,系统研究了切削用量和刀具角度与翅片结构尺寸之间的相互关系,获得了翅片成形的条件及结构尺寸的变化规律;提出了切削-挤压复合成形中刀具的设计原则和几何角度的合理取值范围,为实际应用提供了依据。以刚塑性有限元分析方法为基础,建立了翅片切削-挤压整体成形工艺的三维有限元分析模型,并对仿真过程中的屑-体分离准则、网格畸变等关键问题进行了分析;采用Ansys有限元方法进行了静力分析,得到了翅片内部应力、应变分布规律,获得了翅片脱落的判据;采用Deform-3D有限元方法,对三维翅片成形过程进行了模拟,获得了与理论分析相一致的翅片结构和尺寸的模拟结果,以及应力、应变场的变化规律,为实验研究提供了重要的参考。在理论分析和数值模拟的基础上,针对直翅片结构,在不同切削用量与刀具几何参数条件下,通过单因素和多因素实验研究,获得了工艺参数对翅片几何尺寸的影响规律和翅高、翅厚的经验公式,得到了紫铜和铝材在不同工艺条件下的翅片成形范围;并分析了翅片的实际翅尖结构和理想形状的差异及产生翅片堆积、翅片弯曲、翅尖直立的原因,从而获得了切削-挤压成形过程完整的工艺参数和参数匹配方法。通过对理论与实验分析,建立了切削-挤压力的分析模型,获得了紫铜和铝材切削-挤压力的经验公式。结果表明:采用该方法加工时三个方向分力比普通切削时要大,挤压力起着重要作用,并且轴向力的方向与普通切削时相反,这对刀具设计及设备调整有很好的指导意义。对切削-挤压翅片管换热器进行了模拟计算和实验研究;分析了翅片管结构参数、翅片管内外流体对换热效果的影响,获得了翅片间距、厚度、高度以及翅片管外不同流体对换热效果的影响规律,并通过实验验证了数值模拟的正确性,为翅片管结构参数优化和指导切削-挤压成形过程参数选择提供了依据。
论文目录
摘要Abstract1 绪论1.1 课题来源及其研究意义1.2 翅片管加工现状1.3 切削模拟研究现状1.3.1 金属切削机理研究1.3.2 有限元技术的发展1.3.3 切削过程有限元模拟技术的发展现状1.4 主要研究内容2 切削-挤压复合成形原理2.1 切削-挤压成形过程2.2 翅片的几何形状2.2.1 切削层参数的影响2.2.2 翅片几何尺寸的理论计算2.2.3 变形对翅形的影响2.2.4 翅片表面积计算2.3 切削-挤压复合成形刀具设计2.3.1 刀具的设计原则2.3.2 刀具的几何角度2.4 翅型结构分析2.4.1 副切削刃刃形的影响2.4.2 翅型结构的归类2.5 特殊翅形结构2.5.1 双向翅片结构2.5.2 螺纹表面的加工2.6 本章小结3 切削-挤压过程的刚塑性有限元求解3.1 刚塑性有限元原理3.1.1 刚塑性材料边值问题3.1.2 刚塑性材料不完全广义变分原理3.1.3 基于修正罚函数法的刚塑性有限元基本原理3.2 刚塑性有限元求解3.2.1 刚塑性有限元基本方程3.2.2 初始速度场的确定3.2.3 离散化及位移模式的选择3.2.4 应变矩阵计算3.2.5 单元刚度矩阵计算3.2.6 切削力计算3.3 本章小结4 切削-挤压成形过程仿真4.1 有限元分析方法4.2 切削-挤压过程中的关键技术问题4.2.1 切削-挤压过程中的摩擦4.2.2 切屑-基体分离准则4.2.3 网格畸变问题4.3 切削-挤压过程的有限元静力分析4.3.1 有限元静力分析模型4.3.2 应力应变数值模拟4.3.3 翅片加工失效判据4.4 切削-挤压过程的成形模拟4.4.1 有限元分析模型的建立4.4.2 模拟计算结果分析4.5 刀具应力分析4.5.1 前、后刀面应力分析4.5.2 主、副切削刃应力分析4.6 本章小结5 工艺参数对翅片结构参数的影响5.1 实验条件5.2 翅片几何尺寸的单因素实验5.2.1 切削深度对翅片几何尺寸的影响5.2.2 进给量对翅片几何尺寸的影响5.2.3 切削速度对翅片几何尺寸的影响5.2.4 主偏角对翅片几何尺寸的影响5.2.5 实验结论5.3 翅片几何尺寸的多因素实验5.3.1 数学模型的建立5.3.2 翅片几何尺寸的多因素实验5.4 翅片的有效成形范围5.4.1 紫铜翅片的有效成形范围5.4.2 铝翅片的有效成形范围5.5 翅片的翅尖结构5.6 本章小结6 切削-挤压成形的切削力研究6.1 切削-挤压力6.2 切削-挤压力实验6.2.1 实验条件6.2.2 切削用量对切削-挤压力的影响6.2.3 切削用量及主偏角对切削-挤压力的影响6.2.4 实验结果分析6.3 切削-挤压力有限元仿真6.3 本章小结7 切削-挤压成形翅片管换热特性研究7.1 翅片管换热器模型的建立7.1.1 CFD概述7.1.2 几何模型的建立7.1.3 格的划分7.1.4 湍流模式选择7.2 数值计算结果分析7.2.1 翅片管外流体速度与温度的分布7.2.2 翅片管结构参数优化7.2.3 内、外流体对换热效果的影响7.3 翅片管换热特性的实验研究7.3.1 实验原理及装置7.3.2 实验对象及结果分析7.3.3 数值模拟与实验结果对比分析7.4 本章小结8 结论与展望8.1 研究结论8.2 发展与展望致谢参考文献攻读博士学位期间发表论文及参与研究项目
相关论文文献
标签:切削挤压复合成形论文; 翅片论文; 刀具角度论文; 工艺参数论文; 数值模拟论文;