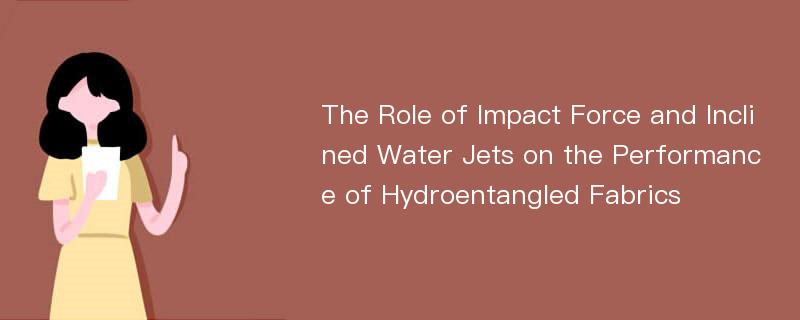
论文摘要
Hydroentangling is a mechanical bonding process involving the interlocking of fibers in a web structure using fine,closely spaced,high-pressure water jets.The main objective of this research was to investigate the role of impact force and inclined water jets for improve on mechanical performance of hydroentangled fabrics.An experimental apparatus was designed with different inclination angles(-200,-100,00,+100,+200).The simulation using Phoenics,version 3.4 CFD software was conducted to verify impact force experimental data of water jets flow.The predicted CFD impact force has good agreement with experimental data compared to calculated impact force.The 60 gsm and 100 gsm fiber webs of bicomponent fibers(PET/COPET,PA6/COPET and PA6/PET)were manufactured and tested for their mechanical performance as well as evaluating fiber splitting within fiber webs.The results show that with increases of water jets inclination angle,impact force,and water jets pressure,the mechanical performance and fiber splitting of hydroentangled fabrics were enhanced.The water jets inclination angles of-100& +100 shows higher mechanical performance followed,by -200&+200 and the last 00,while PA6/PET was highly split followed by PA6/COPET(split without dissolution of the sea) and PET/COPET did not split.It can be concluded that the combination of impact force and inclined water jets with low inclination angles in appropriate conditions improved the mechanical performance.The One Way of Analysis of Variance(ANOVA)and the Multicompare Analysis using MATLAB were used for statistical data analyses.This research work addresses issues that are not dealt with in previous publications.
论文目录
ABSTRACTSACKNOWLEDGEMENTNOMENCLATURECHAPTER ONE:INTRODUCTION1.1 Application of Hydroentanglement1.1.1 Hydroentangled Non-wovens Properties1.1.2 Fiber Application in Hydroentanglement1.2 Bicomponent Fibers.1.2.1 Splittable Bicomponent Fibers1.2.2 Application of Splittable Bicomponent Fiber1.3 Splitting Methods1.4 Hydroentanglement Development1.4.1 Hydroentanglement Machines Development1.5 Previous Research Work1.5.1 Hydroentanglement Water Jets/Nozzle Geometry1.5.2 Specific Energy and Jet Pressure1.5.3 Fiber Types1.5.4 Forming Wire1.5.5 Impact Force1.6 Shortcomings of Previous Research1.7 Research Objectives1.8 Research OutlinesCHAPTER TWO:DESIGNING OF EXPERIMENTAL APPARATUS2.1 Introduction2.2 Statement of Operation2.3 Designing Consideration2.3.1 Path Distance Consideration2.3.2 Velocity Consideration2.4 Designing of Apparatus Components2.4.1 Designing of jet plates2.4.2 Designing of Pressure Water Tank2.4.2.1 Calculation for Checking Stress of Tank Shell2.4.2.2 Calculation for Checking Stress of Top Cover and Bottom Cover2.5 Components Selection2.6 Force Sensor and Personal Computer2.7 Assembled of Designed Experimental Apparatus2.8 Advantages and Limitation of the Apparatus2.9 Summary and ConclusionCHAPTER THREE:THEORETICAL ANALYSIS OF IMPACT FORCE3.1 Impact force3.1.1 Flow characteristics in the nozzle orifice3.1.2 Calculation of outlet water jet velocity at nozzle orifice3.1.3 Impact Force Calculation on the Upper Surface of the Web3.1.4 Impact force calculation on the individual fibers within fiber web during hydroentanglement process3.2 ConclusionCHAPTER FOUR:NUMERICAL SIMULATION AND IMPACT FORCE EXPERIMENTS4.1 Introduction4.2 CFD-Phoenics Software Package4.3 Physical Model4.3.1.Boundary Conditions4.3.2 Initial Conditions4.4 Numerical Simulation and Grid System4.4.1 Governing Equations4.5 Numerical Results and Discussion4.5.1 Velocity Distribution Depending on Standoff Distance4.5.2 Pressure Distribution Depending on Standoff Distance4.5.3 Impact Force Measurement4.5.3.1 Influence of Water Jet Pressure on Impact Force4.5.3.2.Influence of Water Jet Inclination Angle on Impact Force.1)on Impact Force.'>4.5.3.3 Influence of Standoff Distance(L1)on Impact Force.4.5.4.Influence of Basis Web Weight on Impact Force4.5.5 Prediction Errors4.6 ConclusionCHAPTER FIVE:MATERIALS AND METHODOLOGY5.1 Materials5.1.1 Testing of Fiber Properties5.1.1.1 Tensile Properties5.1.1.2 Fiber Friction Properties5.1.1.3 Fiber Length5.1.1.4 Fiber Diameter5.1.1.5 Linear Density5.1.1.6 Specific Resistance5.1.1.7 Number of Crimps5.1.1.8 Fiber Properties Summary5.2 Equipment5.2.1 Fiber Web Formation5.2.2 Experimental Apparatus5.2.3 Hydroentanglement Unit5.2.4 Web Support5.3 Impact Force5.3.1 Sensor calibration5.3.2 Impact force measurement5.3.3 Apparatus for Impact Force Measurement5.4 Testing of Hydroentangled Fabrics5.4.1 Mechanical Properties5.4.1.1 Tensile Strength5.4.1.2 Tear Strength5.4.1.3 Bursting Strength5.4.1.4 Basis Weight5.5 Images5.5.1 Fabric Images5.5.2 Water jets imagesCHAPTER SIX:INFLUENCE OF PROCESSING VARIABLES ON FIBER SPLITTING6.1 Objective6.2 Fiber Splitting Evaluation6.3 Fiber Splitting Before Hydroentanglement6.4 Fiber Splitting After Hydroentanglement(Based on Designed Apparatus)6.4.1 Fiber splitting of PA6/PET6.4.2 Fiber splitting of PET/COPET6.4.3 Fiber splitting of hydroentangled fabrics(PA6/PET,PA6/COPET and PET/COPET)based on 10 bars with different inclination angles6.5 Fiber Splitting After Hydroentanglement(Hydroentanglement Machine)6.5.1 Fiber splitting of PA6/PET(Based on Hydroentanglement Machine)6.5.2 Fiber splitting of PET/COPET(Based on Hydroentanglement Machine)6.5.3 Fiber splitting of PA6/COPET(Based on Hydroentanglement Machine)6.6 ConclusionCHARPTER SEVEN:ROLE OF PROCESSING VARIABLES ON MECHANICAL PERFORMANCE OF HYDROENTANGLED FABRICS7.1 Experimental Approach Based on Preliminary Experiment on Designed Apparatus7.2 Objectives of Preliminary Experiment on Designed Apparatus7.3 Results and Discussions of Preliminary Experiment7.3.1 Tensile Strength of Hydroentangled Fabrics.7.3.2 Bursting Strength7.3.3 Tear Strength7.4 Conclusion of Preliminary Experiments on designed apparatus7.5 Main Experiments on Designed Apparatus and Industrial Machine7.5.1 Experimental Approach of Main Experiments7.5.1.1 Materials7.5.1.2 Processing Parameters Based on Main Experiment7.5.2 Experimental Results,Data Analysis and Discussion of Main Experiments7.5.2.1 The Effects of Water Jets Inclination angle,Fiber Types on Tensile Strength7.5.2.2 The Effects of Water Jets Pressure,Fiber Types on Tensile Strength7.5.2.3 The Effects of Impact Force,Fiber Types on Tensile Strength7.5.2.4 The Effects of Impact Force,Fiber Types on Strain at Break7.5.2.5 The Effects of Water Jets Inclination Angle,Fiber Types on Strain at Break7.5.2.6 The Effects of Water Jets Pressure,Fiber Types on Elongation at Break7.5.3 Stress-Strain Curve7.6 ConclusionCHAPTER EIGHT:SUMMARY,CONCLUSION AND FUTURE WORK PROSPECTIVE8.1 Summary and Conclusions8.1.1 Theoretical Analysis,Numerical Simulation and Impact Force Experiments8.1.2 Effects of Processing Variables on Mechanical Performance8.1.3 Influence of Water Jet Pressure,Inclination Angle,and Fiber types on Fiber Splitting8.2 Future Work ProspectiveReferencesAppendix
相关论文文献
The Role of Impact Force and Inclined Water Jets on the Performance of Hydroentangled Fabrics
下载Doc文档