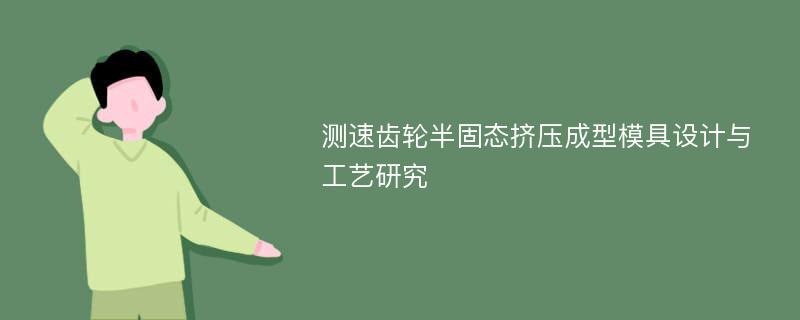
论文摘要
随着现代铁路交通运输向着高速、重载方向发展,机车车辆普通碳钢铸钢零件已明显不能满足使用要求,正在逐步被低合金钢和轻金属所取代。铸钢材质升级后,传统的砂型铸造工艺在生产中暴露出了一系列问题。为了解决这些问题,本文首次提出采用半固态流变挤压铸造成形工艺进行机车车辆关键铸钢件测速齿轮的研究,并以材料7075(LC9)铝合金作为研究材料,利用自制专用测速齿轮流变挤压模具,从半固态浆料制备、成形质量的控制、铸件组织与性能等方面对该工艺进行了系统的实验与理论研究。通过采用斜坡冷却法对7075铝合金进行半固态浆料制备,制备出了适宜于半固态流变挤压铸造成形的细小的蔷薇形非枝晶组织浆料,并用平均等积圆直径定量分析了非枝晶组织特征,得出了最佳的工艺参数值:斜坡的最佳长度为400mm、角度为60°。在此工艺参数条件下,7075铝合金非枝晶组织的平均等积圆直径为40.5μm,圆整度达到0.8。在最佳工艺参数下制备出的半固态浆料,利用流变挤压铸造成形方法研制机车车辆件测速齿轮,并且对7075铝合金半固态流变挤压铸造成形质量进行了研究。结果表明:半固态流变挤压成形工艺优势的获得,需要正确的工艺参数来保证。当工艺参数选择不合理时,铸件易出现表面冷隔、皮下气孔、热裂纹等缺陷。在最佳工艺条件下,利用模拟软件ProCAST和ANSYS分别对普通铸造和流变挤压成形过程进行模拟,通过对计算结果分析与实验结果相比较,得出最佳成形工艺参数:在模具预热温度为180~220℃,凸、凹模拔模斜度为1°,成形比压为69.1MPa,保压时间为5s时,挤压出了内、外质量良好的测速齿轮挤压件。
论文目录
致谢中文摘要ABSTRACT1 绪论1.1 选题依据与研究意义1.2 半固态流变挤压铸造原理与工艺特点1.2.1 半固态流变挤压铸造原理1.2.2 半固态流变挤压铸造工艺特点1.3 半固态流变挤压铸造工艺的分类1.4 半固态流变挤压铸造技术的关键1.4.1 加压设备1.4.2 半固态浆料的制备1.4.2.1 外场作用下枝晶破碎球化技术1.4.2.2 合金内部物理化学作用下的枝晶抑制生长技术1.4.3 半固态浆料定量浇注1.4.4 模具设计1.4.5 工艺过程的自动控制1.5 论文研究目标和内容1.5.1 研究目标1.5.2 研究内容2 测速齿轮模具设计2.1 零件工艺分析2.2 成形方案2.2.1 加工余量2.2.2 分型面位置2.2.3 模具设计有关参数及计算2.2.3.1 投影面积、体积及压力中心2.2.3.2 流变挤压力2.2.3.3 脱模力2.2.3.4 孔隙率的减小2.3 模具设计2.3.1 模具整体结构2.3.2 拔模斜度2.3.3 配合间隙2.3.4 模具主要零件设计2.3.4.1 凹模2.3.4.2 凸模2.3.4.3 镶块2.4 本章小结3 测速齿轮成型工艺研究3.1 半固态浆料制备3.1.1 浆料组织特征3.1.2 斜坡冷却法的研究现状3.1.3 实验方法3.1.4 实验结果3.2 成型质量控制研究3.2.1 实验材料及装置3.2.2 模用涂料3.2.3 成型影响因素3.2.4 实验过程3.2.5 实验结果3.3 本章小结4 测速齿轮模拟与工艺优化4.1 砂铸工艺模拟4.1.1 ProCAST软件介绍4.1.2 三维实体造型与有限元网格划分4.1.3 模拟参数的设定4.1.4 结果与分析4.2 流变挤压工艺过程模拟4.2.1 ANSYS软件介绍4.2.2 三维实体造型建模4.2.3 网格的划分4.2.4 约束设置及加载情况4.2.5 求解及分析4.3 铸件缺陷形成机理与分析4.3.1 冷隔4.3.2 皮下气孔4.3.3 热裂纹4.4 控制缺陷的工艺措施4.5 小结5 结论参考文献作者简历学位论文数据集
相关论文文献
标签:半固态论文; 流变挤压论文; 铝合金论文; 斜坡冷却法论文; 成形质量论文; 组织论文;