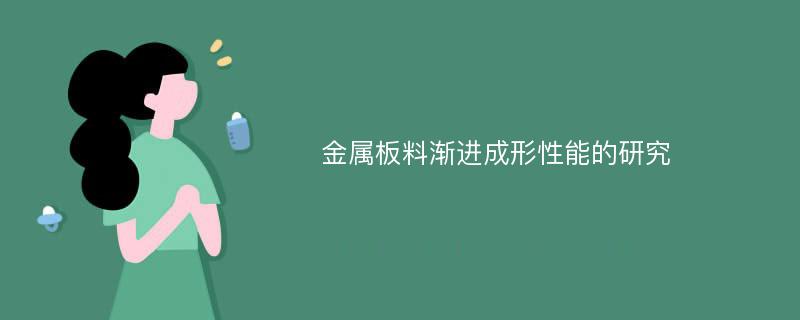
论文摘要
单点渐进成形技术(SPIF,single point incremental forming)是一种新型钣金加工技术,适用于小批量生产和样件加工。本课题主要研究对象为金属板料在渐进成形中的成形性能,提出了一种测试板料最大成形极限角的新方法。新方法使用一个成形角沿深度方向变化的零件,在工具头的作用下,板料以余弦规律变薄,即加工后的板料厚度等于其原始厚度乘以该处成形角的余弦值。试样在减薄率达到极限值时破裂,破裂处的成形角为0°到90°之间的某一数值,这一数值即可看作是试样材料在单点渐进成形工艺中的最大成形极限角。这种方法可以用单个试件计算出最大成形极限角。而传统的测试方法要使用一系列成形角不同的零件来确定最大成形极限角。这种新测试方法的三个几何参数(即试样零件的口径、零件几何体母线的曲率半径和最初成形角)及试样形状对成形性能的影响已通过实验的方法做了研究。实验结果表明,在特殊的范围内,试样的成形性能随上述三个参数中前两个参数的增大而提高,随第三个参数的增大而降低。在形状方面,实验表明零件的拐角对成形性能是有影响的。以上发现有助于试件的标准化设计。除最大成形角外,成形极限曲线也可以用来描述单点渐进成形的成形性能。本论文中提出了几种测试FLC的新方法,与原有方法的结果做了比较,并指明了原有测试方法的不足,实验发现新方法测出的成形性能要好于原有方法,所以新方法测得的FLC更加精确。在完善了新的测试方法后,研究了工具头半径、加工步长、成形速度和板厚等工艺参数对成形性能的影响。参数的变化范围要远远大于先前的研究。以前的研究中,没有考虑到两个参数的交互作用对成形性能的影响,本课题第一次使用响应面法对交互作用的影响做了研究。在研究纯钛板的成形性能时,提出了一种新的润滑工艺,在钛板表面覆盖一层孔径特定的多孔氧化膜以容纳固体润滑剂,避免工具头与钛板的黏着。研究发现,两个参数的交互作用对成形性能是有影响的,其中工具头半径和加工步长的交互作用、工具头半径和板厚的交互作用对成形性能的影响是非常明显的。为了获得材料的最大成形性能,必须从交互作用的层次去选择参数,例如板厚的增加并非总能提高成形性能,还应当考虑到工具头半径的影响。有限元分析表明,使用小工具头时,接触力和接触应力随板厚的增加而增加,造成了成形性能的降低。成形速度对成形性能的影响是因材料而异的,对于钢板和钛板,成形速度在不同的范围内,对成形性能有积极或消极的作用,但对于铝板,成形性能没有受到成形速度较为明显的影响。一系列经验公式的提出,有助于预测冲压和渐进成形的成形性能。为了确定对成形性能影响最大的材料性能参数,实验对大量的材料进行了实验。实验发现,同之前的观点不同,材料的单拉断面收缩率是与成形性能最相关的参数,并且可以用来评定材料的成形性能。此外,本课题中对比了渐进成形与冲压工艺在成形性能上的区别,渐进成形提高了材料的成形性能,提高的比率随破裂处厚向真应变的增加而增加。最后阐述了成形缺陷可能会造成的影响,首次研究了成形缺陷与成形性能的关系。定义了挤出飞边、向内褶皱和底部凸包三种缺陷,发现三种缺陷的出现均会对成形性能造成影响。对工具头半径、板厚、加工步长、成形角、屈服应力和加工硬化指数等参数对成形缺陷的影响程度做了计算。结果发现挤出飞边和向内褶皱在使用小工具头加工厚板的时候容易出现,其程度随成形角、加工步长和屈服应力的增长而增大。有限元分析结果表明,挤出飞边现象的加剧是由于工具头轴向上的接触力和压应力增加造成的。加工硬化指数是产生底部凸包现象相关性最大的因素,上凸的高度随加工硬化指数、板厚和加工步长的增加而增加,随成形角的增加而减小。有限元分析结果表明,上凸高度随成形角的增加而减小、随板厚的减小而减小是应归因于工具头周围的Von-Mises应力分布。进一步的研究表明,板料的过早破坏是由于成形缺陷和工具头尺寸间存在密切的关系,且在工具头半径很小时易发生。为了避免这种失效,本论文中提出了一个以板厚、加工步长、成形角和屈服应力为变量的经验公式,以计算工具头半径的最小值。
论文目录
摘要AbstractList of figuresList of tablesList of symbols1. Introduction1.1 History of incremental forming1.2 Classes of incremental forming processes1.2.1 Conventional incremental forming processes1.2.2 Modern incremental forming processes1.3 Merits of single point incremental forming1.4 Terminology and process parameters of single point incremental forming1.5 Literature review on single point incremental forming1.5.1 Equipment and tooling1.5.2 Surface quality1.5.3 Forming forces1.5.4 Process accuracy1.5.5 Forming limits and mechanics1.5.6 Applications and innovations1.6 Challenges in single point incremental forming1.7 Problem statement and contributions of this thesis1.8 Methodology1.8.1 CAD/CAM1.8.2 Equipment1.8.3 Tools and materials1.8.4 Lubrication1.8.5 Printing and measurement of strain grids1.8.6 Wall thickness measurement1.8.7 Tensile testing and microscopy1.8.8 Design of experimental plans1.8.9 Finite element analysis1.9 Organization of the dissertation2. Testing formability: A–A novel test to evaluate maximum wall angle2.1 Basic concept of new test2.2 Test geometry and mathematical formulations2.3 Definition of maximum wall angle and the name of test2.4 Evaluating maximum wall angle employing newly proposed test2.4.1 Test conditions2.4.2 Test results2.5 The effect of variation in the geometrical parameters of test geometry upon the VWACF test results2.5.1 The effect of variation in the horizontal curvature radius upon the test results2.5.2 The effect of variation in the initial wall angle upon the test results2.5.3 The effect of variation in the generatrix radius upon the test results2.6 The effect of variation in the generatrix type upon VWACF test results2.7 Comparison between VWACF test and existing test2.8 Summary and conclusions3. Testing formability: B–Effect of change in the shape of test geometry upon the test results3.1 Testing formability with changed test geometry3.1.1 The shape and geometrical parameters of the new test geometry3.1.2 Test conditions3.1.3 Test results3.2 Comparison between VWAPF and VWACF tests–Effect of sheet formability3.3 The effect of variation in the geometrical parameters of the test geometry upon the VWAPF test results3.3.1 The effect of variation in the half-side length3.3.2 The effect of variation in the initial wall angle3.4 Sheet stiffness and formability3.4.1 Testing sheet stiffness3.4.2 Correlation of blank stiffness with half-side length of pyramid3.4.3 The effect of sheet stiffness upon formability3.4.4 Finite element analysis3.5 Standardization of test specimen3.6 Summary and conclusions4. Testing formability: C–New methods to determine forming limit curves4.1 Determination of FLC4.1.1 Description of new approaches4.1.2 Definition of FLC4.2 Comparison between FLCs from new approaches4.3 Comparison between FLCs of new approaches and straight groove test4.4 The effect of wall angle upon the position and shape of FLC4.5 Summary and conclusions5. Process parameters and formability: A–Aluminum and steel sheets5.1 The effect of operating parameters upon the formability5.2 Material nature and the effect of forming speed upon formability5.3 The effect of sheet thickness upon formability5.4 The interactive effect of sheet thickness and tool size upon formability5.4.1 Experimental analysis5.4.2 Finite element analysis5.5 The effect of blank size and blank holding force upon formability5.6 Summary and conclusions6. Process parameters and formability: B–Titanium sheet6.1 Tool and lubrication for incremental forming of titanium sheet6.1.1 Experimental investigations for tool6.1.2 Experimental investigations for lubricant6.1.3 Effectiveness of lubricant and lubrication method6.1.4 Characterization of the film used for lubrication6.2 The effect of operating parameters upon formability6.3 Comparison between the incremental and conventional formability6.4 Summary and conclusions7. Material properties and formability7.1 Correlations of material properties with formability in single point incremental forming7.2 Correlations of material properties with improvement in formability caused by single point incremental forming7.2.1 Measure of improvement in sheet formability7.2.2 Correlations of improvement in sheet formability with material properties7.3 Summary and conclusions8. Forming defects and formability8.1 Kinds of forming defects and their relevance with formability and material properties8.1.1 Metallic wall8.1.2 Fold-in8.1.3 Bulge8.2 The effect of process parameters upon forming defects8.2.1 Test plan8.2.2 Quantification of forming defects8.2.3 Test geometry8.2.4 Regression analyses8.3 Analytical modeling of the forming defects8.4 Minimum tool radius and premature sheet failure due to simultaneous effect of forming defects8.4.1 Design of experiments8.4.2 Significance of parameters and empirical model to predict minimum tool radius8.5 Summary and conclusions9. Conclusions and recommendations9.1 Important conclusions9.1.1 A new formability test9.1.2 New methods to determine forming limit curves9.1.3 The effect of process parameters upon formability9.1.4 The effect of material properties upon formability9.1.5 The effect of forming defects upon formability9.1.6 Lubrication method for incremental forming of pure titanium sheet9.2 Recommendations9.3 Proposals for future researchList of referencesAppendix 1List of publicationsAcknowledgements
相关论文文献
- [1].超声弯曲工具头的动态特性仿真与实验研究[J]. 轻工机械 2014(02)
- [2].超声塑化注射系统环形间隙的设计与仿真[J]. 中国机械工程 2017(15)
- [3].大尺寸立方体开槽超声塑料焊接工具头的优化设计[J]. 声学技术 2010(01)
- [4].带工具头变幅杆的优化修整及其振动性能试验[J]. 工具技术 2013(01)
- [5].带工具头超声变幅杆节点定位偏差问题分析[J]. 声学技术 2013(03)
- [6].带有成形工具头的超声抛光变幅杆研究[J]. 机械制造与自动化 2013(02)
- [7].NUM推出新型工具头NUMcut[J]. 机床与液压 2011(12)
- [8].复杂地质条件下大直径钢顶管顶进入海技术[J]. 城市道桥与防洪 2020(07)
- [9].一种通用超声工具头的设计与钻削试验[J]. 工具技术 2012(05)
- [10].点压渐进成形工具头运动轨迹形成方法研究[J]. 锻压技术 2015(03)
- [11].板料数控渐进成形过程金属变形行为分析[J]. 中国工程机械学报 2014(02)
- [12].基于ANSYS Workbench的超声振动系统设计与优化[J]. 锻压技术 2015(11)
- [13].数控渐进成形工艺参数对表面质量的影响[J]. 机械制造与自动化 2016(03)
- [14].顶管地下对接工艺及过程控制[J]. 建筑施工 2008(01)
- [15].工具头转速对TRIP钢板渐进成形微观组织的影响[J]. 模具工业 2019(03)
- [16].液压拆除机器人发展现状研究[J]. 机械工程与自动化 2018(04)
- [17].基于6R机器人的自动脱模系统总体设计[J]. 组合机床与自动化加工技术 2017(10)
- [18].基于数值模拟的方锥件渐进成形规律研究[J]. 热加工工艺 2013(01)
- [19].超声珩磨工具头横向辐射声场的建模与仿真[J]. 陕西师范大学学报(自然科学版) 2018(03)
- [20].超声波对污泥脱水性能的影响因素研究[J]. 吉林农业科技学院学报 2015(02)
- [21].基于核环境下应急机器人机械臂结构分析与优化设计[J]. 机械设计与制造 2015(07)
- [22].临海地区大口径顶管施工技术[J]. 建筑施工 2010(02)
- [23].超声加工微结构工艺试验与分析[J]. 航空精密制造技术 2008(06)
- [24].超声处理铝硅合金过程中的溢出现象(英文)[J]. Transactions of Nonferrous Metals Society of China 2013(11)
- [25].基于神经网络与遗传算法的方锥件渐进成形扭曲位移优化[J]. 模具工业 2017(12)
- [26].硬质材料超声波微孔加工装置研究[J]. 农机使用与维修 2019(07)
- [27].手机屏幕磨料冲击加工声学系统设计[J]. 机电工程 2012(12)
- [28].三点渐进式无模成形分析与数值模拟[J]. 轻工机械 2011(04)
- [29].基于声子晶体位错理论的二维超声塑料焊接系统[J]. 物理学报 2020(18)
- [30].35CrMo钢超声波铸造的导波系统模态分析及实验研究[J]. 铸造 2016(04)
标签:单点渐进成形论文; 成形性能论文; 几何参数论文; 工艺参数论文; 材料性能论文; 成形缺陷论文;