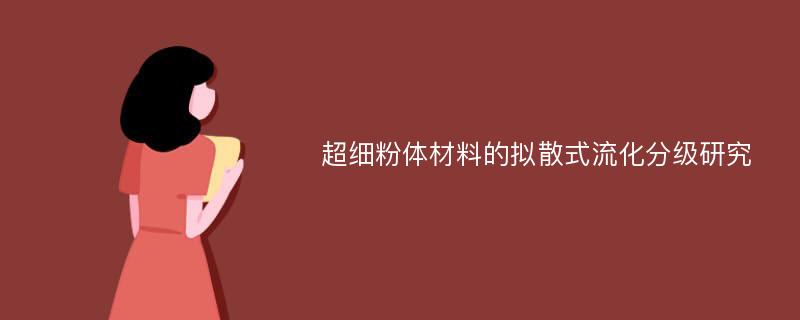
论文摘要
在微细粒级粉体加工技术中,颗粒分级是得到合格粒度产品的关键步骤,现代工业对细粒度、窄级别提出了越来越高的要求。目前,各种干式分级技术都难以达到湿式分级的精度。本文根据湿式分级与散式流化的类似性,提出了拟散式流化的分级方式,通过强化颗粒分散和气体均布,提高干式分级的分级效率。依据气固两相流理论设计了拟散式流化分级装置,利用CFD软件对其结构和操作参数进行了优化设计,通过实验研究获得了该装置的分级性能数据。所作的主要研究工作如下:(1)对新型布料装置内颗粒的各种受力进行分析比较,建立了颗粒团聚概率方程。理论计算表明气速为3m/s的气流产生的剪切应力能将干燥物料充分分散的概率为99.99%,保证了颗粒在分级区域中达到良好的分散,实现“拟散式”的目的。通过推导分级器内颗粒运动的理论公式,计算得到其结构的大致参数,为数值模拟提供了几何模型。(2)利用FLUENT6.2对不同结构下的气相流场进行了模拟,优选了进气方式和整流内构件,使流场得到规整。在气相流场模拟的基础上,用相间耦合的随机轨道模型预测了不同粒径颗粒的运动轨迹,并对布料装置进行了结构改进。结合理论计算结果,得到了拟散式流化分级器的最终结构。(3)单级分级实验考察了表观气速、进料量对粒级分配效率和分级精度的影响,结果表明,分级精度随表观气速的增大和进料量的减小而提高,大气速下得到的粒级效率曲线中“鱼钩效应”有所改善。对于特定的分级任务,难以达到清晰切割,粗产品中仍含有大量细颗粒,仅靠单级分级装置无法实现精密分级。(4)实验进行了颗粒物料的循环分级,发现循环五次可将原料中1μm颗粒的含量降低到一次分级的1/10。据此改进了实验设备,实验结果表明,随着分离时间的增加,粗产品中细颗粒含量降低,“鱼钩”越来越小,分级精度得到提高。(5)拟合实验数据,得到了描述粒级效率的模型方程,对模型曲线和实验效率曲线作图并计算方差,可知模型与实验数据吻合较好。
论文目录
摘要ABSTRACT前言1 文献综述1.1 颗粒分级研究进展1.1.1 分级的概念和类别1.1.2 超细分级设备的发展和研究概况1.2 流化分级的概念1.2.1 流态化现象1.2.2 流化形成的条件和流态化体系的特征1.2.3 流态化分级原理1.3 本研究的目的、意义和内容1.3.1 项目研究的目的和意义1.3.2 课题的研究内容1.3.3 本研究的创新之处2 超细粉体分级装置的初步设计2.1 分级系统的设计构思2.1.1 研究范围2.1.2 干式分级机存在问题的理论分析2.1.3 拟散式流化分级技术2.2 分级关键问题的解决2.2.1 分级的关键问题2.2.2 分散的解决方案2.2.3 分离的解决方案2.3 其它部件的设计2.3.1 匀风板设计2.3.2 旋风除尘器设计2.4 本章小结3 超细粉体分级器的CFD 模拟3.1 物理模型与控制方程3.1.1 物理模型的选用3.1.2 计算控制方程3.2 计算区域与网格划分3.3 气相流场的数值模拟3.3.1 数值模拟方法的选择3.3.2 设计模拟方案3.3.3 模拟结果与讨论3.3.4 分级器内流场分布分析3.4 颗粒运动轨迹的数值模拟3.4.1 模拟方法的选择3.4.2 布料装置的模拟与改进3.4.3 分级器内颗粒运动轨迹模拟3.5 本章小结4 实验研究4.1 单级分级实验测试4.1.1 实验装置4.1.2 实验流程4.1.3 实验步骤4.1.4 实验物料分析4.1.5 分级性能计算方法4.1.6 结果分析与讨论4.2 多次分级效果实验4.3 循环式分级效率实验4.3.1 循环式分级4.3.2 实验方法4.3.3 结果分析4.4 分级效率数学模型4.4.1 回归数学模型4.4.2 误差分析4.5 分级器性能评价4.6 本章小结结论参考文献附录1 原料粒度测试结果附录2 改变表观气速后粒度测试数据附录3 改变进料速率后粒度测试数据附录4 改变分离时间后粒度测试数据致谢攻读硕士学位期间发表的学术论文目录
相关论文文献
标签:颗粒分级论文; 数值模拟论文; 拟散式流化论文; 气固两相流论文;