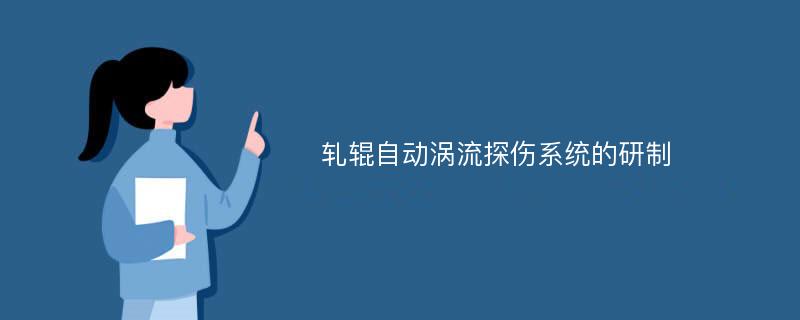
论文摘要
轧辊是轧钢厂非常重要的生产部件。如果轧辊表面带有裂纹上机使用,那么在带钢轧制过程中很容易引发轧辊工作层局部剥落,甚至发生断辊事故。为了防止轧辊事故的发生,我们在轧辊上机前要对其表面进行无损探伤。涡流探伤是我们目前最常用的一种检测方式。宝钢热轧厂磨辊车间的轧辊数控磨床上装备有自动涡流探伤仪,主要用于轧辊表面的无损检测。该探伤仪是1995年从美国ASKO公司引进,其操作软件在DOS系统上运行,功能比较简单,由于其设计上存在缺陷,已无法满足生产的要求。本课题研究的目的就是为了解决目前探伤仪上存在的问题,重新设计新的轧辊自动涡流探伤系统,来满足生产的需要。论文从第二章开始,系统地阐述了涡流产生的原理以及涡流的特性,在此基础上运用等效电路分析的方法揭示了涡流探伤的实质是对涡流线圈阻抗变化量的测量,并且分析了引起涡流线圈阻抗变化的诸多因素。本章还阐述了涡流线圈阻抗变化量测量的原理以及缺陷信号调制和解调的过程。论文的第三章主要介绍安装在轧辊磨床上的自动涡流探伤仪的基本结构和性能特点,重点阐述了引起探头和辊面之间间隙变化的主要因素,并提出了补偿间隙变化的主要方法。该章节还对目前我们所使用的涡流探伤仪存在的问题进行详细地分析,并提出了解决方案。论文的第四章和第五章分别论述了新的轧辊涡流探伤系统的硬件设计和软件设计。在硬件设计中,重点论述了涡流探伤仪的探头系统、信号处理单元以及轧辊坐标采集系统的设计。在软件设计中,主要论述了探伤仪单片机子系统和工控机子系统的软件设计、探伤仪与磨床控制系统之间通讯功能的实现以及工控机操作软件界面的设计。论文的第六章以实验数据为基础,从探伤的稳定性和缺陷定位的准确性两个方面对新的轧辊自动涡流探伤系统的性能进行综合测试。论文最后对轧辊自动探伤技术的未来发展方向进行展望,提出了多种探伤技术相结合的复合探伤方式将是未来轧辊自动探伤技术的发展方向,并且随着生产规模的不断扩大,多台探伤仪的集中监控技术和数据联网共享技术也会在轧辊自动化探伤领域得到越来越广泛地应用。
论文目录
摘要ABSTRACT1 引言1.1 轧辊自动涡流探伤系统研制的意义和背景1.2 本课题研究的主要内容1.3 本章小结2 涡流探伤概述2.1 涡流探伤原理2.2 涡流线圈阻抗分析2.2.1 涡流线圈的阻抗2.2.2 接近导体材料的涡流线圈阻抗及归一化2.2.3 引起线圈阻抗变化的主要因素2.3 涡流线圈阻抗变化量的测量原理2.4 缺陷信号的调制和解调2.4.1 缺陷信号的调制2.4.2 缺陷信号的解调2.5 涡流探伤的优缺点2.5.1 涡流探伤的优点2.5.2 涡流探伤的缺点2.6 本章小结3 轧辊自动涡流探伤仪3.1 轧辊自动涡流探伤仪基本结构3.2 轧辊涡流探伤特点3.3 影响探伤稳定性的主要因素3.3.1 提离效应3.3.2 探伤间隙波动的主要因素及补偿方法3.4 探伤结果的显示3.5 轧辊坐标的采集3.6 探伤过程的控制3.7 本章小结4 轧辊自动涡流探伤系统的硬件设计4.1 轧辊自动涡流探伤系统的组成结构及功能4.1.1 系统组成4.1.2 各组成部分的功能4.1.3 系统工作过程简述4.2 涡流探头系统设计4.2.1 涡流线圈结构设计4.2.2 多个涡流线圈的组合4.2.3 线性接近开关4.2.4 探头驱动机构设计4.3 下位机主要电路板设计4.3.1 振荡检测板4.3.2 滤波板4.3.3 探头逻辑控制板设计4.3.4 CPU 板4.4 轧辊坐标采集系统设计4.4.1 轧辊周向坐标采集4.4.2 轧辊轴向坐标采集4.5 本章小结5 轧辊自动涡流探伤系统的软件设计5.1 自动涡流探伤系统控制软件结构5.2 单片机子系统软件5.2.1 下位机 CPU 板单片机控制程序5.2.2 探头逻辑控制板单片机控制程序5.3 工控机子系统软件5.4 下位机、工控机、磨床之间的通讯5.4.1 串口通讯控制的实现5.4.2 两种探伤方式下的数据交换5.5 探伤仪操作软件设计5.5.1 系统参数设定5.5.2 系统校准5.5.3 轧辊检测5.5.4 探伤过程显示5.5.5 档案查看5.5.6 管理员入口界面5.5.7 表格显示图谱5.6 本章小结6 轧辊自动涡流探伤系统性能测试和评估6.1 轧辊自动涡流探伤系统性能测试6.1.1 探伤稳定性测试6.1.2 缺陷定位准确性考核6.2 轧辊涡流探伤仪的技术展望6.2.1 复合探伤技术6.2.2 直观的图谱显示6.2.3 探伤数据的管理6.3 本章小结参考文献致谢攻读硕士学位期间已发表或录用的论文
相关论文文献
标签:涡流探伤论文; 探头论文; 线圈论文; 裂纹论文; 软点论文; 轧辊论文;