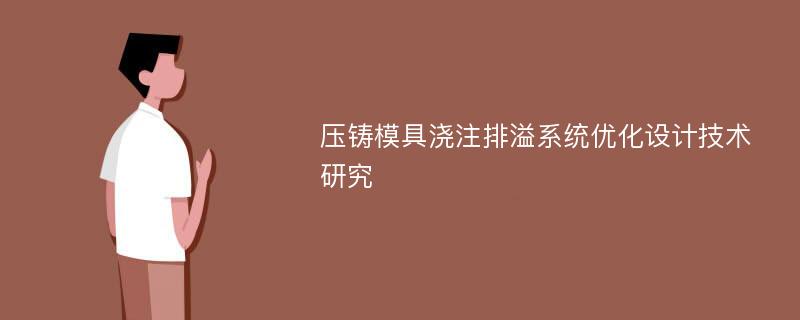
论文摘要
随着机械、电子、汽车及航空航天等工业的发展,特别是近年来我国汽车工业的蓬勃发展,为金属压铸件的应用提供了广阔的空间。压铸成型虽具有高效益、高效率等优点同时也是废品率高、产品质量不易保证的成型工艺。生产实际表明,压铸模具浇注排溢系统的设计是决定压铸产品质量的关键因素之一。模具设计时,如何根据不同结构类型的压铸件设计出合理的浇注排溢系统结构形式,是模具设计技术研究的重要内容之一。本文在对压铸成型金属填充理论和压铸模具设计技术发展现状深入分析的基础上,针对压铸模具浇注排溢系统设计的实际过程,应用现代优化设计技术和CAE分析技术相结合的方法,进行了压铸模具浇注排溢系统优化设计的研究。通过对金属液在不同结构类型模具型腔中的填充流动过程分析,以金属液到达模具型腔各处的流程最短为目标,构建了薄壁平板型和薄圆盘类压铸件的模具浇口位置优化设计模型,并通过细长型扳手压铸件模具浇注排溢系统的优化设计过程,表明了采用优化设计方法获得的浇注排溢系统结构方案压铸时,金属液的填充流态和铸件质量,明显优于未采用优化设计方法时的浇注排溢系统方案。通过应用PROCAST软件模拟仿真,也表明了优化模型的有效性,并可减少数值模拟的次数,提高设计效率。本文研究的浇口位置优化设计方法,对进一步实现压铸模具浇注排溢系统的整体优化设计,提供了有效的参考。
论文目录
摘要Abstract1 绪论1.1 压铸技术国内外发展概况1.2 压铸模具设计技术概况1.2.1 压铸模具设计技术现状1.2.2 浇注排溢系统设计发展趋势1.3 课题研究的意义和主要内容1.3.1 课题的意义和应用价值1.3.2 课题的主要研究内容2 压铸模具浇注排溢系统设计理论及CAE分析技术2.1 金属压铸充型相关理论2.1.1 金属压铸填充理论2.1.2 压铸填充过程中金属流的类型2.2 压铸模具CAE分析技术2.2.1 压铸充型过程数学模型2.2.2 压铸凝固过程温度场模拟数学模型2.2.3 压铸CAE的数值计算方法2.2.4 凝固过程缩孔、缩松分析3 浇注排溢系统的设计内容3.1 压铸件分析3.2 内浇口设计3.3 横浇道设计3.4 直浇道设计3.5 排溢系统设计2图优化压铸系统匹配'>3.6 PQ2图优化压铸系统匹配2图的实质'>3.6.1 PQ2图的实质2图优化浇注系统设计'>3.6.2 PQ2图优化浇注系统设计4 压铸模具浇口位置优化模型的建立4.1 最优化理论及应用4.1.1 最优化问题基本模型4.1.2 最优化问题实现4.2 浇口位置优化数学模型4.2.1 无约束优化4.2.2 有约束优化5 浇注排溢系统优化设计5.1 压铸件结构分析5.2 分型面的选择5.3 浇口位置优化设计5.4 浇口面积优化5.5 浇注排溢系统设计形式5.6 CAE模拟分析5.6.1 有限元模型的建立5.6.2 模拟参数设置5.6.3 充型过程模拟结果及分析5.6.4 凝固模拟结果及分析5.7 扳手压铸件质量分析5.7.1 宏观质量分析5.7.2 微观质量分析5.8 其它结构类型铸件压铸模具浇注排溢系统优化设计5.8.1 薄板类压铸件5.8.2 圆盖类压铸件5.8.3 圆盘类压铸件5.8.4 壳类压铸件结论参考文献攻读硕士学位期间发表学术论文情况致谢
相关论文文献
标签:压铸模具论文; 浇注排溢系统论文; 优化设计论文; 分析论文;