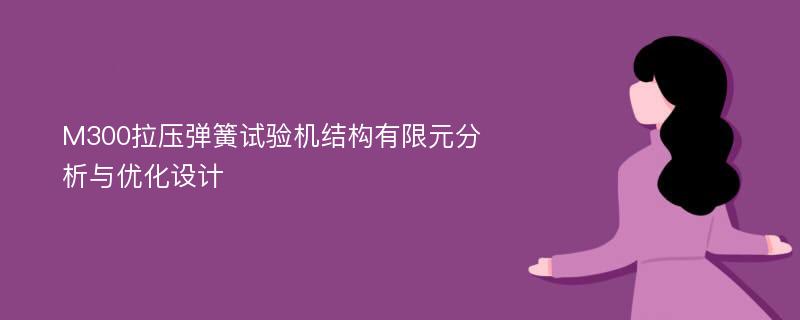
论文摘要
弹簧试验机是通过被测弹簧在已知载荷作用下的变形量来测试其刚度的。为提高M300拉压弹簧试验机的测试精度,满足广大用户的需求,首要任务就是提高试验机的结构刚度,减小其横梁结构在工作载荷作用下的挠度。在导师陈树勋教授的指导下,本文作者完成了该试验机结构的有限元分析与优化设计,为本试验机结构设计质量的提高提供了理论依据。M300拉压弹簧试验机采用门式结构,最大拉压工作载荷为300kN。由于试验机结构为多个零部件组成的装配结构,各零部件之间既非刚接又非铰接,而是通过紧固螺栓、轴承等方式连接,各零部件之间存在大量接触问题。这就使该结构分析变成复杂的接触非线性分析问题,需要采用接触副单元并进行大量迭代计算;另外本试验机结构分析还存在螺栓连接的预紧力施加以及轴承连接的等效刚度、等效弹性模量等问题。本文研究成功的解决了以上问题,完成了该弹簧试验机有限元分析的建模工作。并利用有限元分析软件ANSYS对该试验机的2种最大试验载荷工况成功地进行了结构有限元分析,得到各工况下结构应力的分布和应力较大的危险点及各横梁的Y向变形量,即各横梁的挠度,为该试验机的结构优化奠定了基础。对本试验机的结构优化,厂方要求在试验机外围尺寸不变的前提下,寻求试验机内部结构的设计方案,以尽可能降低其横梁结构的挠度,为此,笔者根据结构不同部位尺寸对横梁挠度的影响以及结构应力分布选择合适的设计变量、约束条件及目标函数,建立该结构的优化设计数学模型;采用ANSYS与导重法相结合的结构优化方法,完成了试验机结构的构件尺寸优化设计。在结构重量不变和满足材料许用应力的前提下,试验机满载压力试验时,横梁、压盘Y向变形量由原来的0.320mm下降到0.199mm,下降37.8%;试验机满载拉力试验时,横梁、压盘Y向变形量由原来的1.372mm下降到0.290mm,下降78.9%。优化效果十分显著,成功完成了该弹簧试验机的优化设计任务。
论文目录
摘要Abstract第一章 绪论1.1 前言1.2 结构有限元分析概述1.3 结构优化设计概述1.4 现代结构优化计算方法的发展与现状1.4.1 数学规划法和优化准则法1.4.2 序列数学规划法与近似概念1.5 本文的研究内容1.5.1 问题的提出1.5.2 本文的工作第二章 拉压弹簧试验机的概述2.1 M300拉压弹簧试验机的总体构成2.2 M300拉压试验机工作原理2.3 M300拉压试验机主机组成第三章 优化前M300拉压弹簧试验机结构有限元分析3.1 弹簧试验机结构有限元分析的建模3.1.1 网格单元选取与材料特性3.1.2 几何模型的建立3.1.3 网格划分3.1.4 接触副3.1.5 螺栓预紧力3.1.6 轴承等效弹性模量3.1.7 加载与约束3.2 优化前试验机结构有限元分析3.2.1 工况1—最大压力试验工况3.2.2 工况2—最大拉力试验工况3.3 本章小结第四章 弹簧试验机结构调优4.1 机械结构设计基本准则4.2 试验机结构调优4.2.1 上横梁结构改进4.2.2 移动横梁结构改进4.2.3 底座结构改进4.3 改进后试验机结构有限元分析4.3.1 工况1—最大压力试验工况4.3.2 工况2—最大拉力试验工况4.4 本章小结第五章 结构优化数学模型处理、导重法与敏度分析5.1 结构优化设计的数学模型5.2 结构优化设计的数学模型处理5.2.1 归一化处理2.2.2 均方根包络函数2.2.3 数学模型的最终形式5.3 导重法5.3.1 重量约束结构优化设计的导重准则法5.3.2 导重的意义与迭代控制方法5.3.3 单约束最轻设计导重准则法5.3.4 库恩—塔克乘子的求法5.4 灵敏度分析5.4.1 灵敏度分析方法5.4.2 结构特征应力的敏度计算第六章 试验机结构尺寸优化设计6.1 结构尺寸优化设计的数学模型6.2 设计变量的选取6.3 约束条件6.4 结构尺寸优化方法—以ANSYS为分析器的结构优化导重法6.4.1 参数化语言APDL与ANSYS优化过程介绍6.4.2 以ANSYS为分析器的结构优化导重法6.5 试验机结构尺寸的优化迭代计算6.6 优化后试验机结构有限元分析6.6.1 工况1—最大压力试验工况6.6.2 工况2—最大拉力试验工况6.7 本章小结第七章 总结与展望7.1 总结7.2 展望参考文献致谢攻读学位期间发表的学术论文目录
相关论文文献
标签:拉压弹簧试验机论文; 导重法论文; 结构有限元分析论文; 结构优化设计论文;