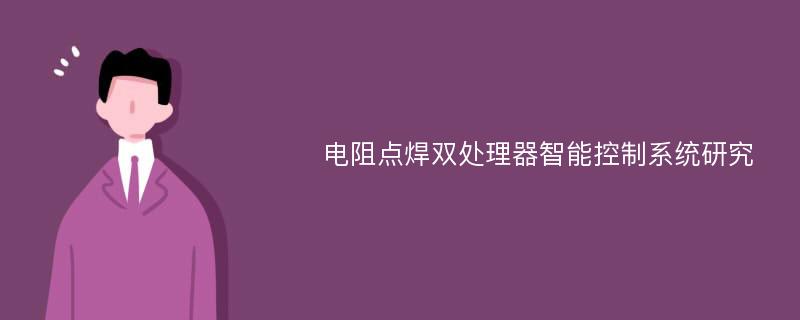
论文摘要
电阻点焊是一种重要的焊接方法,广泛应用于汽车、航空航天等工业。随着电阻点焊应用领域的不断扩展和深入,对电阻焊控制系统提出了更高的要求。但由于电阻点焊是一个高度非线性、多变量和强耦合的复杂过程,点焊质量受到多种因素的影响,传统的采用单一参数反馈质量控制方法存在很大局限性。基于此本文设计了一种以89C51单片机为核心的双处理器微机控制系统,合理分配并细化微处理器的任务,提高系统的实时控制能力,为多参数综合质量监控以及智能控制的实现奠定基础。设计了双处理器的硬件电路及控制系统,对时钟电路模块、A/D、D/A转换电路模块、键盘及显示电路模块等进行了详细分析,并编写了焊接主程序、双机通讯程序、键盘及显示程序、AD/DA转换程序、焊接电流PID控制算法等程序。设计了电极位移测控系统,利用体积小、分辨率高的光栅传感器对点焊过程的电极位移进行实时检测;利用峰值角法计算电流有效值。以RBF神经网络为基础,建立了以焊接电流、焊接时间、电极压力、板厚作为神经网络的输入,熔核直径作为输出的神经网络模型,实现了对点焊工艺参数的优化设定。采用正交试验方法,针对生产中常用的板材低碳钢在不同的焊接参数下进行等厚双板焊接,通过多组试验获得了点焊工艺参数的最优组合,并对所建立的神经网络模型进行了验证。点焊试验结果表明,神经网络模型对熔核尺寸的预测误差小于8%,说明建立的神经网络模型是正确的,预测结果准确可靠。对熔核尺寸的预测精度可以满足实际生产的要求,对于提高点焊质量具有一定的理论与实际应用价值。
论文目录
摘要Abstract1 绪论1.1 课题的目的及研究意义1.2 国内外研究进展与现状1.2.1 电阻点焊过程质量监控方法的研究进展1.2.2 微机控制技术研究现状1.3 课题研究的内容2 电阻点焊双处理器的硬件设计2.1 主电路的组成及工作原理2.2 电阻点焊双处理器控制系统的原理2.3 电阻点焊双处理器的电路模块2.3.1 晶闸管触发电路模块2.3.2 A/D转换电路模块2.3.3 D/ A转换模块2.3.4 键盘及显示模块2.3.5 电磁气阀驱动电路2.3.6 报警电路2.3.7 电流采样电路3 电阻点焊双处理器的控制系统3.1 双处理器的软件程序设计3.1.1 主机系统主程序设计3.1.2 从机系统主程序设计3.2 控制系统程序设计3.2.1 双机串行通讯3.2.2 PID控制系统程序3.3 系统程序调试3.3.1 系统的设备及开发环境3.4 电阻点焊位移测控系统4 神经网络模型的建立4.1 神经网络简介4.1.1 神经网络的特点4.1.2 神经网络在焊接领域的应用4.2 RBF神经网络模型结构4.2.1 径向基函数网络模型4.2.2 RBF网络的数学基础4.2.3 RBF网络的学习过程4.3 点焊的 RBF神经网络模型的建立4.3.1 点焊工艺参数对熔核直径的影响4.3.2 点焊工艺参数的合理匹配5 点焊工艺试验5.1 试验条件5.1.1 试验材料5.1.2 试验设备5.2 试验方案设计5.2.1 正交表5.2.2 正交试验设计的基本步骤5.2.3 试验过程5.3 熔核尺寸与焊接工艺参数模型的建立5.3.1 多元线性回归方程5.3.2 建立数学回归模型5.4 神经网络模型的验证6 结论6.1 论文总结6.2 研究展望参考文献在学研究成果致谢
相关论文文献
标签:双处理器论文; 智能控制论文; 光栅传感器论文; 神经网络论文; 正交试验论文;