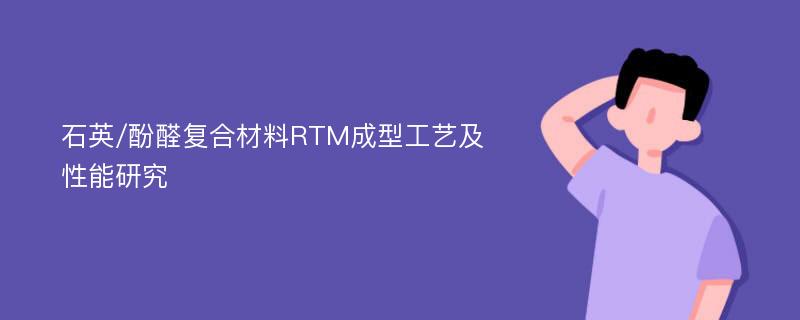
论文摘要
本文针对RTM工艺成型耐烧蚀锥形壳体的要求,开展了酚醛树脂及其固化物性能研究、石英/酚醛复合材料平板件及典型构件的RTM工艺及力学性能和烧蚀性能研究。通过DSC分析和凝胶时间实验研究了钡酚醛、氨酚醛、苯并噁嗪和酚醛型氰酸酯四种酚醛树脂的固化特性;考察了四种酚醛树脂固化物的力学性能、热性能及微观形貌;通过树脂的动态粘度特性、等温粘度特性研究了树脂的流变特性,并建立了树脂的化学流变模型,对树脂的RTM工艺窗口进行了预报。研究表明:钡酚醛和苯并噁嗪树脂具有较大的低粘度范围和较长的低粘度保持时间,力学性能和耐烧蚀性能优良,可以作为RTM成型耐烧蚀复合材料的基体材料。采用RTM工艺制备了石英/钡酚醛和石英/苯并噁嗪复合材料平板试件,研究了注射压力、纤维体积含量、制件厚度对复合材料的孔隙率、力学性能、烧蚀性能的影响。结果表明:注射压力对RTM石英/酚醛复合材料的性能影响显著,理想的注射方式是先低压后高压;随纤维体积含量增加,复合材料的孔隙率降低、力学性能提高;制件厚度几乎不影响复合材料的孔隙率和烧蚀性能;石英/苯并噁嗪复合材料的性能较高,在纤维体积含量为50%时,其拉伸强度、弯曲强度、压缩强度、层剪强度、冲击强度和质量烧蚀率分别为600MPa、691MPa、480MPa、64MPa、497kJ·m-2和0.0527g·s-1。以某防热结构头锥壳体为实际背景,采用依模缝合技术制备了纤维预成型体,解决了变厚度复杂锥形壳体的成型难题,通过RTM工艺制备了石英/钡酚醛复合材料头锥壳体。结果表明:成型的复合材料壳体尺寸精度高、表观质量优良、均一性好,壳体各部分的孔隙率与平板复合材料的相接近,壳体整体性能优良。
论文目录
表目录图目录摘要ABSTRACT第一章 绪论1.1 引言1.2 耐烧蚀酚醛基复合材料1.2.1 酚醛基复合材料烧蚀防热机理1.2.2 耐烧蚀酚醛基复合材料体系1.2.3 酚醛基复合材料的成型工艺1.3 RTM 工艺方法1.3.1 RTM 工艺简介1.3.2 RTM 工艺技术特点1.3.3 RTM 工艺适用的树脂体系1.4 论文选题依据及研究内容1.4.1 选题依据1.4.2 研究内容第二章 RTM 酚醛树脂性能研究2.1 RTM 酚醛树脂固化工艺研究2.1.1 树脂固化温度的确定2.1.2 树脂固化时间的确定2.2 RTM 酚醛树脂固化物性能研究2.2.1 树脂固化物力学性能2.2.2 树脂固化物热性能2.2.3 树脂固化物微观形貌分析2.3 RTM 酚醛树脂的流变特性研究2.3.1 树脂的动态粘度特性2.3.2 树脂的等温粘度特性2.3.3 树脂化学流变模型的建立2.3.4 树脂的RTM 工艺窗口预测2.4 本章小结第三章 石英/酚醛复合材料平板件的RTM 工艺及性能研究3.1 主要工艺条件对石英/酚醛复合材料孔隙率的影响3.1.1 孔隙率的测定方法3.1.2 注射压力对复合材料孔隙率的影响3.1.3 纤维含量对复合材料孔隙率的影响3.1.4 制件厚度对复合材料孔隙率的影响3.1.5 石英/酚醛复合材料孔隙率比较研究3.2 主要工艺条件对石英/酚醛复合材料力学性能的影响3.2.1 注射压力对复合材料力学性能的影响3.2.2 纤维含量对复合材料力学性能的影响3.2.3 制件厚度对复合材料力学性能的影响3.2.4 石英/酚醛复合材料力学性能比较研究3.3 主要工艺条件对石英/酚醛复合材料烧蚀性能的影响3.3.1 注射压力对复合材料烧蚀性能的影响3.3.2 纤维含量对复合材料烧蚀性能的影响3.3.3 制件厚度对复合材料烧蚀性能的影响3.3.4 石英/酚醛复合材料烧蚀性能比较研究3.4 本章小结第四章 石英/酚醛复合材料典型构件的RTM 工艺研究4.1 典型构件的结构分析4.2 构件预成型体的制备4.2.1 整体铺层设计4.2.2 依模缝合制备头部预成型体4.2.3 纤维增强体铺覆4.3 树脂注射充模的工艺控制4.3.1 充模过程的影响因素4.3.2 头锥充模的工艺控制过程4.4 构件的性能考核4.4.1 表观质量4.4.2 结构尺寸4.4.3 纤维含量和孔隙率4.5 本章小结第五章 结论致谢参考文献附录
相关论文文献
标签:复合材料论文; 酚醛树脂论文; 耐烧蚀复合材料论文; 工艺论文;