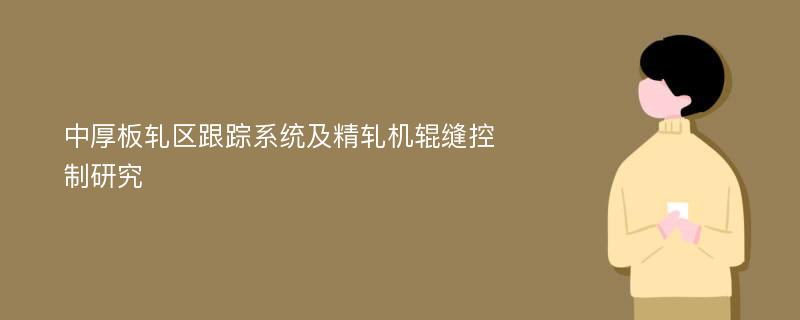
论文摘要
.本文依托作者研究生期间参与的实际工程项目,对中厚板生产线上轧区微跟踪系统的准确性和鲁棒性、轧区过程级宏跟踪设计与优化、精轧机辊缝控制以及相应系统的平台建设做了以下研究:1.微跟踪系统采取计算为主、实测数据修正为辅的方法,为实现热检故障自动检测与报警、自动评估热检信号准确性、自动辨识单块钢触发和多块钢触发、自动删除错误跟踪轧件等,跟踪系统设置了“软报警阀”机制、“同步窗口”机制、“长度裁判”机制和“队列自动删除”机制;跟踪模块检测工作辊速度和运用高精度前滑模型,进行轧制过程中的轧件跟踪,并利用此跟踪模块进行轧件长度的软测量;分析了轧机推床处轧件的横向跟踪和控制。2.为减小过程机系统对生产线检测设备的依赖性,通过合理划分宏跟踪区域,合理布置跟踪队列,数据信号的设计和采集,进行严密的辊缝和轧制力推理,采用数据传输触发机制,实现了单、双机架下手动或者自动轧制模式的区域宏跟踪,并可稳定匹配一定方式的控制轧制模式。3.为减小成品头部厚差,在基础自动化系统中编程实现头部数据自动采集,分析发现由于咬钢时电动压下回缩而液压补偿滞后引起头部辊缝增大,对此进行补偿后取得较好的效果。4.编制程序自动测量了某2800mm中厚板精轧机刚度,发现轧机刚度非线性较强,轧机传动侧和非传动侧刚度差异较大,给基础自动化和过程机控制提供了准确的刚度曲线;为增强辊缝控制能力,末几道次摆辊缝方式需要根据轧制条件选择全液压或者电液联摆方式,并改进液压预摆辊缝和液压带载调节时的同步控制策略。5.对中厚板轧线上常用检测仪表的检测方式方法做了一定阐述,为相关设备的选择提供参考;对微跟踪系统、基础自动化和过程机控制系统的硬件和软件做了相关阐述。
论文目录
摘要ABSTRACT第一章 绪论1.1 国内外中厚板生产概述1.1.1 国内外中厚板生产装备水平和技术现状1.1.2 国内中厚板生产技术发展趋势1.2 中厚板生产自动控制系统1.2.1 液压AGC.系统及自动控制1.2.2 全自动轧制技术1.2.3 轧制线跟踪系统概述1.3 本文研究的意义和内容第二章 轧区微跟踪设计与应用2.1 轧区轧件微跟踪意义及实现方法2.1.1 轧件微跟踪意义2.1.2 实现方法2.2 轧区轧件微跟踪设计2.2.1 跟踪框架设计2.2.2 跟踪过程逻辑2.2.3 跟踪系统在区域内的常规处理方法2.3 轧区微跟踪系统优化2.3.1 轧件头部位置更新2.3.2 HMD报警及处理2.3.3 跟踪同步控制2.3.4 区域平滑过渡设计2.3.5 轧机推床处轧件位置横向微跟踪2.4 轧制过程的轧件位置微跟踪2.4.1 纵向位置微跟踪模型2.4.2 长度软测量2.5 本章小结第三章 轧区宏跟踪设计与应用3.1 轧区宏跟踪概述3.1.1 轧件的区域宏跟踪说明3.1.2 实际现场情况3.1.3 轧区模型触发及区域划分3.2 轧区宏跟踪整体设计3.3 数据触发机制3.3.1 平均实测数据消息触发机制3.3.2 轧机末道次信号触发机制3.3.3 PDI数据传送触发机制3.3.4 轧件跟踪异常处理3.4 本章小结第四章 中厚板精轧机辊缝设定控制4.1 液压摆辊缝和电动摆辊缝比较分析4.1.1 电动压下和液压压下速度4.1.2 压下系统位置控制精度4.1.3 全液压轧制和液压缸下装式轧制4.2 液压压下同步控制4.2.1 常规同步控制方法4.2.2 同步控制方法优化4.3 头部厚差分析4.3.1 头部沉入现象分析4.3.2 辊缝沉入的危害4.3.3 辊缝沉入的解决方案4.4 绝对AGC4.4.1 绝对值AGC实际应用问题4.4.2 绝对值AGC的改进4.5 刚度影响分析4.5.1 两侧刚度差异4.5.2 轧机刚度M的修正4.6 本章小结第五章 系统平台建设5.1 微跟踪及基础自动化系统5.1.1 硬件设计与选择5.1.2 控制系统软件5.2 轧区宏跟踪系统平台5.2.1 硬件5.2.2 软件5.3 本章小结第六章 结论参考文献硕士期间完成的工作致谢
相关论文文献
标签:中厚板论文; 微跟踪论文; 宏跟踪论文; 软测量论文; 同步控制论文; 头部沉入论文;