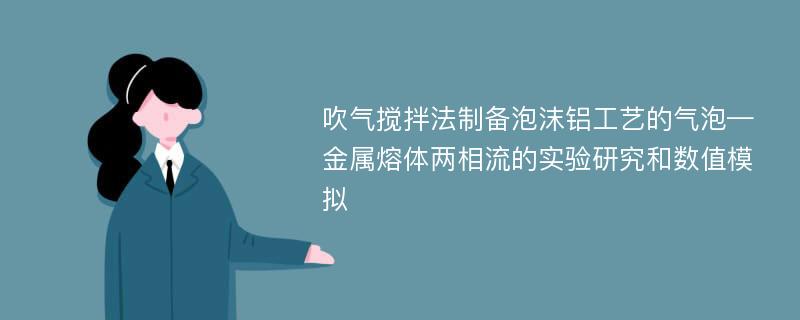
论文摘要
闭孔泡沫金属是一种内部结构含有大量孔隙的新型功能材料。它具有独特的结构和性能,工业中有着重要的应用和广阔的发展前景。制备泡沫金属的方法很多,其中吹气发泡法因为设备简单、成本低、可以连续生产等特点,更适用于规模化生产。在制备泡沫金属过程中,如何控制气泡的尺寸及其均匀度是该项工艺的核心问题。由于影响泡沫尺寸及其分布的因素众多,为了寻求能够对生产过程和产品性能进行科学控制的有效手段,需要对泡沫形成过程中的各个影响因素进行全面、系统的研究。本文采用实验研究和数值模拟相结合的方法对泡沫铝发泡特性及发泡过程中气泡一熔体两相流动过程进行了系统的研究。主要研究内容包括以下几个方面: 在自制井式炉内进行吹气发泡法制备泡沫铝的实况工艺实验。研究不同工艺参数对泡沫铝成品结构和性能的影响。并以泡沫铝的空气发泡过程为研究对象,依据相似原理进行水模拟(聚乙烯醇水溶液)实验,实验采用静态和动态两种形式。静态实验模拟在无涡流场状态下进行,通过改变入射压缩空气的压力与流量、聚乙烯醇水溶液的黏度以及通气孔的直径,对入射空气在聚乙烯醇水溶液中形成气泡的过程以及气泡在水溶液中的运动和变化规律进行研究。动态实验模拟是在强旋涡流场条件下,主要考虑搅拌速度、发泡室尺寸以及搅拌轴位置等因素对铝泡沫尺寸和分布的影响,探讨气泡在涡流场中的行为和变化规律。 气泡直径是影响泡沫铝性能的非常重要的因素。本文应用动力学平衡半经验关系式,分析气体通过锐孔在静止黏性液体中形成气泡的过程,预测气泡直径,确定影响气泡尺寸的主要因素。计算结果表明,在一定物性及一定锐孔直径的情况下,流量是影响气泡大小的重要因素。随着流量的增加,气泡直径增大。相同气体流量下,表面张力系数越大,锐孔直径越大,得到的气泡直径越大。液体密度的影响表现得较为复杂,当流量较小时,气泡体积随液体密度的增大而减小;当流量增加时,液体密度的影响便减小。 应用双流体模型及两相κ-ε湍流模型分别描述气体在静止液态金属中单孔射流及多孔射流两相流动,在总结和分析文献中气泡—液体双流体模型的基础上,提出虚拟入口的方法以简化孔口气泡形成过程,对气液相问作用力模型及湍流模型进行改进,通过与实验数据的比较,表明气液相间作用力修正对气液体系流体动力学行为有重要影响,改进的模型具有较好的预测能力。考察了液相密度、液相黏度、气泡直径、熔池尺寸、通气孔的数目及位置对气含率分布、气泡上升速度和液速的影响。单孔条件下两相流中液相物性会影响
论文目录
摘要Abstract1 绪论1.1 课题背景及意义1.2 泡沫金属的研究现状1.2.1 泡沫金属的结构参数1.2.2 泡沫金属的性能及应用1.2.3 泡沫金属的制备方法1.3 气泡动力学1.3.1 单气泡的形成1.3.2 连续气体射流1.3.3 气泡的变形1.4 气泡在金属熔体中运动的研究现状1.4.1 基本数理模型1.4.2 流体模型1.4.3 数值解法1.4.4 静止液体中吹气过程数值模拟1.4.5 旋转流场中吹气过程数值模拟1.5 个体总数(气泡数)平衡模型1.5.1 模型描述及输运方程1.5.2 气泡聚合和破碎模型1.6 本文研究内容2 吹气发泡法制备闭孔泡沫铝的实验研究2.1 泡沫铝发泡实验2.1.1 实验设备及过程2.1.2 测量方法2.1.3 实验结果2.2 静态水模拟实验2.2.1 实验设备2.2.2 不同参数对液体表面气泡直径的影响2.3 动态水模拟实验中各参数对气泡直径的影响2.3.1 发泡熔体黏度2.3.2 发泡室容积2.3.3 压缩空气压力2.3.4 压缩空气流量2.3.5 通气孔直径2.3.6 搅拌速度2.3.7 搅拌轴位置3 静止黏性液体中气泡的形成及其尺寸的计算3.1 气泡的形成过程3.1.1 膨胀过程3.1.2 气泡的脱离3.1.3 气泡的上升3.2 计算结果及分析3.2.1 计算值与实验值的比较3.2.2 影响气泡尺寸的因素3.3 本章小结4 气泡—熔体两相流动数学模型及数值解法4.1 双流体模型4.1.1 基本方程组4.1.2 相间作用力4.1.3 湍流模型4.2 控制方程离散4.2.1 网格的划分4.2.2 初始条件和边界条件的离散4.3 FLUENT软件简介5 无搅拌作用下等直径气泡—金属熔体两相流的数值模拟5.1 Wood金属中底吹氦气过程中气泡特性5.1.1 网格划分及边界条件5.1.2 模拟结果分析及讨论5.2 静止Wood金属中底吹氮气过程中气泡特性5.2.1 网格划分及求解方法5.2.2 模拟结果分析及讨论5.3 液态铝中单孔底吹空气过程的气泡特性5.3.1 流动特性及气泡分布特性5.3.2 影响气泡分布的因素5.4 多孔喷吹流动模拟5.4.1 两孔靠近中心分布5.4.2 两孔靠近壁面分布5.4.3 四孔均布5.4.4 六孔均布5.5 本章小结6 搅拌作用下等直径气泡—旋转熔体两相流的数值模拟6.1 模型的确定6.1.1 桨叶的模拟6.1.2 湍流模型6.1.3 气泡初始直径的预测6.1.4 求解方法6.2 水平轴搅拌作用下的两相流动6.2.1 网格划分及数值求解方法6.2.2 液相流动特性6.2.3 气体流动特性和气泡分布特性6.3 垂直轴搅拌作用下的两相流动6.3.1 准三维模型6.3.2 边界条件6.3.3 数值模拟结果与讨论6.4 倾斜轴作用下的两相流动6.4.1 模拟工况6.4.2 液相流动特性6.4.3 气泡分布特性6.5 本章小结7 倾斜轴搅拌作用下气泡尺寸分布的三维数值模拟7.1 气泡聚合与破碎模型7.2 模拟工况及边界条件7.3 数值模拟结果与讨论7.3.1 液相流动特性7.3.2 气泡分布特性7.4 影响气泡尺寸的因素7.4.1 发泡熔体黏度7.4.2 发泡室容积及气体流率7.4.3 通气孔直径7.4.4 搅拌速度7.4.5 搅拌轴位置7.5 本章小结结论参考文献攻读博士学位期间发表学术论文情况创新点摘要致谢大连理工大学学位论文版权使用授权书
相关论文文献
标签:泡沫铝论文; 气液两相流论文; 金属熔体论文; 气泡尺寸分布论文; 数值模拟论文; 气含率论文; 多重参考系法论文;
吹气搅拌法制备泡沫铝工艺的气泡—金属熔体两相流的实验研究和数值模拟
下载Doc文档