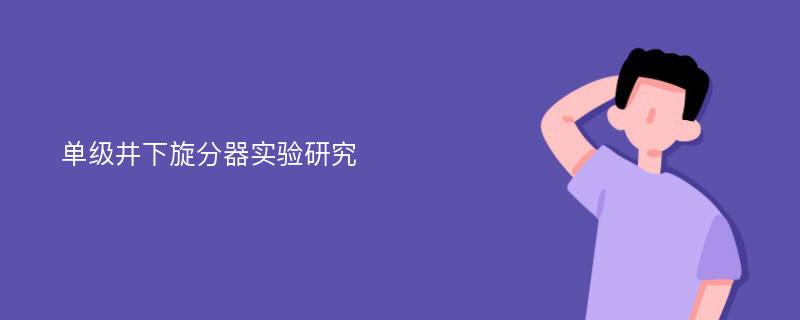
论文摘要
论文介绍了水力旋分器的发展、旋分器在油田上的应用、井下旋流分离器特点及旋流分离器应用于井下的工艺技术前景。井下油水分离系统采用螺杆泵与旋流分离器相结合的形式,是一种上采下注抽吸结构模式的新型油水处理方法,解决采出液含水高,地面油水处理量大等问题。经过对井下油水旋分器结构参数及操作参数的分析与研究,确定了井下旋分器的主要结构参数。利用FLUENT数值模拟软件对井下旋分器进行仿真研究,并最终确定最佳的分流比范围,为课题的研究节省了实验时间和实验经费。研究表明,入口含油量在一定范围内变化时,其分离效果没有明显变化。为了保证整个系统的安全性及较长的使用寿命,本文对主要管柱零件进行了受力分析。完成了在不同分流比下井下旋分器的室内实验,结果表明,旋分器在分流比为25%时,分离效率和综合分离效率最高,分离效率可达99.7%(平均值)。最后,进行了油田现场实验。从系统在井下连续运行的数据来看,实施同井注采后,采出液的含水率下降了7个百分点,生产实践149天中,累计减少采出水量14115.81m~3。该项技术的应用可以解决高含水油田开发过程中油井采出液含水量高、分离工作量大的问题,解决因注水带来的巨大经济损失和能量消耗,是一项很有前途的技术工艺。
论文目录
摘要ABSTRACT创新点摘要第一章 绪论1.1 本文研究背景1.2 旋分器的发展1.3 旋分器在油田上的应用1.4 井下旋流分离器特点1.5 井下旋流分离器的展望1.6 本文主要研究内容及应用价值第二章 井下油水分离系统组成2.1 井下油水分离系统组成及工作原理2.1.1 螺杆泵井下油水分离系统2.1.2 潜油电泵井下油水分离系统2.1.3 柱塞泵井下油水分离系统2.2 井下油水分离器系统注意事项2.2.1 回注层的选取2.2.2 驱动装置日常维护与保养2.2.3 对系统的监控小结第三章 分离系统的选择及旋分器设计3.1 井下油水分离系统的选定3.2 井下旋分器的主要结构参数对其工作影响3.2.1 主直径对旋分器的影响3.2.2 溢流管的长度及直径对旋分器的影响3.2.3 长度及锥角度对旋分器的影响3.2.4 尾管长度对旋分器的影响3.2.5 尾管结构对旋分器的影响3.3 井下水力旋分器的主体结构设计3.3.1 设计方法3.3.2 入口结构设计3.3.3 溢流嘴结构设计3.3.4 旋流腔长度的确定3.3.5 锥角α及θ的确定3.3.6 尾管长度的确定3.3.7 底流口直径的确定3.3.8 大锥段长度及小锥段长度的优选3.3.9 动密封装置的选用3.3.10 总体设计3.4 井下用旋分器的制造技术要求3.4.1 内部表面粗糙度要求3.4.2 要有足够的位置精度和形状精度3.4.3 耐磨及耐腐蚀要求3.4.4 制造方法尽量简单,经济评估合理小结第四章 井下油水旋分器及系统重要部件的数值模拟4.1 控制方程4.2 井下实态条件下数值模拟4.2.1 模拟井井况及介质物性参数4.2.2 模型简化及网格划分4.2.3 数值解法4.2.4 边界条件设定4.2.5 多相流模型的选择4.3 旋分器不同工况条件下数值模拟结果对比分析4.3.1 不同分流比油相浓度分布对比4.3.2 不同入口液含油浓度油相浓度分布对比4.4 系统部件使用寿命计算及受力模拟4.4.1 轴承寿命计算4.4.2 部件受力校核小结第五章 井下旋分器室内实验研究5.1 实验装置建立5.1.1 实验系统5.1.2 实验样机5.1.3 实验物料5.2 室内实验方案5.2.1 实验方案5.2.2 实验流程5.2.3 实验方法及规范5.3 井下旋分器的最佳分流比的确定5.4 井下旋分器入口液含油量不同对分离效率的影响5.5 井下旋分器入口液乳化对分离效率的影响小结第六章 井下油水分离同井注采系统现场应用6.1 现场实施井的选择6.2 现场井况分析6.3 工艺流程6.4 油田现场应用效果小结结论参考文献发表文章目录致谢论文摘要
相关论文文献
标签:井下旋分器论文; 结构设计论文; 数值模拟论文; 同井注采论文; 分离效率论文;