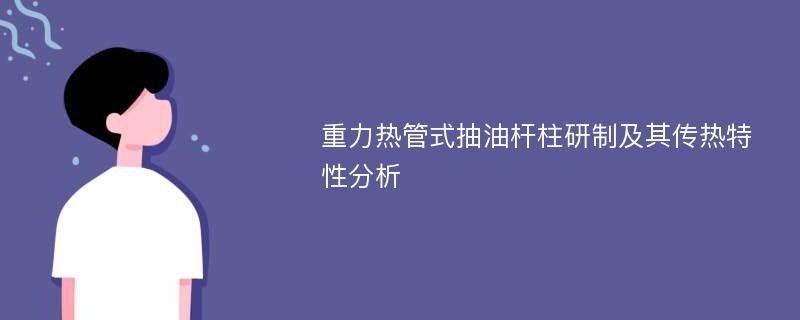
论文摘要
由于原油的粘温特性,原油从井底流向井口的过程中,因散热、降温致使其粘度急剧增加,流动性变差,影响了油井正常生产。为此,需要对油井井筒进行加热以改善原油流动效果。目前广泛采用的电加热方法能耗大、存在电加热抽油杆故障、电缆故障、控制柜故障等问题,循环热流体加热井筒及加化学剂方法不仅增加生产成本,而且使采油井下作业工艺变得复杂。近年来,为了解决这些生产问题,人们提出将热管原理用于改善油井井筒的温度分布。但是,应用重力热管原理采油还有许多问题需要解决。本文针对这一现状,对重力热管式抽油杆柱开展了深入的研究:1.分析并指出了应用热管原理采油亟待解决的重要问题是:①液池过深,沸腾条件苛刻;②蒸汽流速过高,管径过小,携带极限小;③蒸汽流动路径过长,流动阻力过大问题。2.系统地分析了热管内发生的自然现象的机理和影响因素,为重力热管式抽油杆柱设计与制造提供了理论依据。3.进行了重力热管式抽油杆柱传热计算和热工设计研究,提出了由空心抽油杆制成的重力热管的传热计算方法。计算结果表明,由空心抽油杆制成的重力热管的传热功率大约占原油进口热焓的25-30%,大约占向地层散热量的80%,井口原油温度与井底油温之比大于70%,与文中实验结果一致,证明了本文提出的重力热管传热计算方法的正确及合理性。4.研制了重力热管式抽油杆柱壳体杆件。提出了重力热管壳体专用空心抽油杆的制造技术参数和加工工艺技术;成功生产了定型产品抽油杆,产品型号为FTG。通过室内实验,证明本文研制的重力热管壳体专用空心抽油杆抗拉强度达到910MPa,承载扭矩达到3785Nm,杆体强度大大提高;在≥20MPa条件下,保压5min无渗漏,密封性能好。现场试验表明:本文研制的专用杆组成的壳体杆柱断脱率明显降低,无机械强度和密封问题,正常运转时间长,可以作为优先选用的重力热管壳体专用杆件。5.指出了采油用重力热管式抽油杆柱传热与典型重力热管传热之间的差异是地层流出的原油既是热源又是冷源、蒸发段与冷凝段的分界点不固定、通过管壁的热流密度随所处井深不同而不同等。在此基础上形成了室内实验装置设计思路,建立了重力热管式抽油杆柱传热室内实验装置;提出了实验方法,解决了热管充液与排气等工艺和技术问题。6.分析比较了水和本文复配的A液两种备选工质的物性参数、沸腾条件、蒸汽流动阻力和携带极限等重要性能。结果表明,本文复配的A液优于水,确定A液可做为重力热管式抽油杆柱工质,并提出工质充液量为热管内部容积的1520%为宜。7.提出了重力热管式抽油杆柱实验装置冷/热水换热实验操作和分析方法。经过实验,确定热水流量控制值为0.1kg s、冷/热水间换热量为710kw时,可使热水温降达到2030°C ,可满足热管正常运行要求。8.传热实验结果证明,本文研制成功了重力热管式抽油杆柱,热管工作效果良好:①热流体在入口处的0~4米段,温度发生了突然的下降,说明在入口段,热管内的沸腾换热极为强烈,换热强度很大,热管吸收并带走了热流体的可观的热量。②热流体在温度达到最低点以后,温度出现了逐渐的回升现象,然后是平缓地下降,这与冷热水循环系统试验结果形成了鲜明对比,证明热管工作正常。③之后热管内部温度也随之出现波浪型的变化,在入口段急剧下降后,又逐渐回升,并在两曲线交点处超越热流体温度,表明热管能够向热管外油管内的热流体传热。④实验结果表明,热管的工质选择A液是正确、适用的,A液工质避开了常规工质(水)的一系列缺点,不会出现流动阻塞及压降过大的现象。并且经实验可知热管冷凝段与蒸发段的温度之比大于0.7,即表明油井使用热管可使井口原油温度值高于井底油温的70%以上。9.探讨了重力热管式抽油杆柱的实施技术。根据采油现场情况、热管制造技术和本文成功的室内实验经验,对在采油现场制作重力热管式抽油杆柱施工工艺进行了初步研究,提供了具体的操作步骤与方法。本文研究成果为应用热管原理采油提供了可行思路和实用技术,具有一定的应用价值和指导意义。
论文目录
摘要ABSTRACT创新点摘要前言问题的提出热管及其分类热管产生和发展概况石油工程领域热管研究进展及存在问题分析本文拟研究内容第一章 热管基本理论及分析1.1 热管内部的压力平衡c'>1.2 毛细压头ΔPc1.2.1 表面张力1.2.2 润湿现象1.2.3 毛细现象1.2.4 热管毛细压头L'>1.3 吸液芯内的液体压力损失ΔPLL'>1.3.1 用圆管内流动的规律求ΔPLL'>1.3.2 用渗透率求ΔPLV'>1.4 管内蒸汽流动压力损失ΔPV1.4.1 径向雷诺数较小的情况1.4.2 径向雷诺数较大的情况g'>1.5 液体重力ΔPg1.6 热管的吸液极限1.7 热管的携带极限1.7.1 汽液界面相互作用的特点1.7.2 影响因素分析1.7.3 本文推荐的计算公式1.8 热管的声速极限1.9 热管的沸腾极限1.10 本章小结第二章 重力热管式抽油杆柱传热计算和热工设计2.1 传热系统的热平衡分析2.1.1 热平衡的特点及假设2.1.2 传热计算的步骤2.2 设计参数及技术条件2.3 井中原油和热管工质的轴向温度分布定性分析2.4 热管传热量的计算1及Q2 的计算'>2.5 油井中原油与地层之间散热量Q1及Q2的计算2.5.1 简化及假设条件2.5.2 热阻计算2.6 热平衡计算结果总汇out 的计算'>2.7 未采用热管时原油出口温度Tout的计算2.7.1 物理模型2.7.2 计算方法2.7.3 向地层中的散热量的传热计算2.8 本章小结第三章 重力热管式抽油杆柱壳体杆件研制3.1 大庆油田常用的空心抽油杆失效原因分析3.1.1 摩擦焊接式空心抽油杆断脱原因分析3.1.2 镦锻式防脱空心抽油杆断脱原因分析3.1.3 解决问题的思路3.2 重力热管壳体专用抽油杆设计3.2.1 抽油杆安全系数的确定3.2.2 杆体尺寸的确定3.2.3 抽油杆材料优选3.2.4 抽油杆结构设计3.3 重力热管壳体专用抽油杆的加工3.3.1 原材料外观及成分检验3.3.2 杆体接头锻造成型及接头锻造质量检验3.3.3 专用杆整体调质处理3.3.4 杆体缺陷检验3.3.5 杆体校直处理3.3.6 加工与检验3.3.7 杆体防护处理3.4 重力热管壳体专用抽油杆强度及密封性能室内试验3.4.1 插接结构专用抽油杆常规力学性能检验3.4.2 插接结构专用抽油杆的抗扭性能检验3.4.3 锥螺纹结构专用抽油杆室内试验结果分析3.5 重力热管壳体专用抽油杆强度及密封性能现场试验3.5.1 专用抽油杆应用情况3.5.2 专用杆损坏情况统计3.5.3 专用杆失效原因分析3.5.4 事故率对比3.6 采油重力热管壳体抽油杆定型与生产3.7 本章小结第四章 重力热管式抽油杆柱室内实验装置建立4.1 实验装置设计4.1.1 装置设计思路4.1.2 装置构成4.2 室内实验用重力热管式抽油杆柱制造4.2.1 热管壳体4.2.2 充液量确定4.2.3 充液温度条件4.2.4 排气前的准备工作4.2.5 充液和排气工艺4.3 本章小结第五章 重力热管式抽油杆柱传热室内实验研究5.1 热管工质的选择5.1.1 工作温度5.1.2 热阻5.1.3 工质与管材的相容性及自身稳定性5.1.4 其他要求5.1.5 工质的确定及分析5.2 重力热管式抽油杆柱的充液量5.3 重力热管式抽油杆柱实验装置冷/热水换热实验5.3.1 实验目的5.3.2 实验操作步骤5.3.3 实验结果及分析5.4 重力热管式抽油杆柱传热实验5.4.1 实验目的5.4.2 实验设备和仪表5.4.3 实验方法和步骤5.4.4 实验结果及分析5.5 本章小结第六章 重力热管式抽油杆柱实施技术探讨6.1 施工油井的事前热工设计和计算6.2 抽油杆的内部清洗6.3 抽油杆的井下安装6.4 热管顶段的制造及安装6.5 充液准备6.6 充液和排气工艺6.7 本章小结结论参考文献攻读博士学位期间发表的学术论文及科研工作情况发表论文科研工作致谢详细摘要
相关论文文献
标签:重力热管论文; 抽油杆论文; 研制论文; 传热实验论文; 采油工程论文;