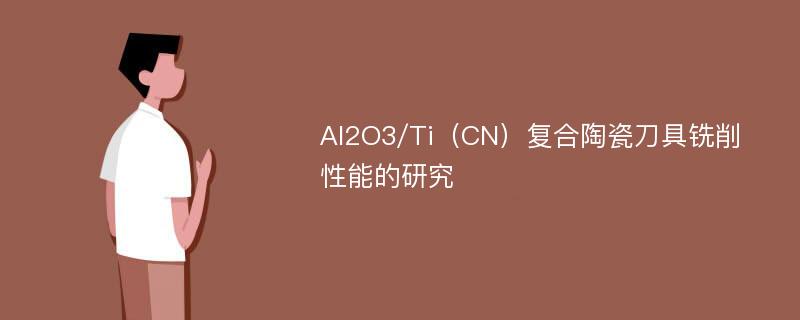
论文摘要
在机械加工中,切削加工是最基本而又可靠的加工手段,而刀具材料的性能对切削加工的效率、工件表面质量、刀具耐用度有着决定性影响。在现代切削加工中,陶瓷刀具材料以其优异的耐热性、耐磨性和化学稳定性,在高速切削领域和切削难加工材料方面起着重要作用,脆性是限制其使用的主要因素。我校成功得研制出断裂韧性达9.1MPa的复合陶瓷刀具材料,在本次论文中重点研究这种复合陶瓷刀具材料铣削35CrMo时所表现的铣削加工性能。本文综合运用材料学和切削加工的相关知识,以单因素试验和正交试验为基础,探索铣削速度、进给速度、铣削深度对切削力、工件表面粗糙度、刀具后刀面磨损宽度的影响;建立对应的切削力模型、工件表面粗糙度模型、后刀面磨损量宽度模型,并且验证模型的显著性;探索工件表面粗糙度成型机理、单齿面铣刀铣削力成型机理以及刀具失效机理;应用有限元软件Deform进行铣削加工仿真,建立铣削模型,在一定的切削用量下预测铣削力的大小和切屑形貌。试验结果发现随着铣削速度的增加,铣削力呈现先减小后增大的趋势,在190m/min时铣削力趋于最小;随着进给速度的增加,切削力先减少后增大,在8mm/min附近处切削力最小;随着切削深度的增加,X、Y、Z方向上的力逐步增加。正交试验发现:铣削深度对铣削力的影响最大、进给速度次之,铣削速度影响最小。同理,铣削深度越小工件表面粗糙度越小,随着铣削速度的增加,工件表面粗糙度先增大后减小,当速度等于175m/min,时工件表面粗糙度值最大,随着进给速度的增加,工件表面粗糙度值增加;进给速度对工件表面粗糙度值影响最大,铣削速度次之,铣削深度影响最小。通过正交试验发现:该刀具失效的形式大部分为磨损失效,这是由于刀具材料的断裂韧性有显著提高。在本文中通过理论研究、试验、仿真等三个环节,发现该陶瓷刀具有很大的优越性,与普通的陶瓷刀具有很大的区别,总之结合本次论文和以往研究可以得知该种陶瓷刀具适合高速加工高硬度材料,在加工过程中尽量避免震动。
论文目录
摘要Abstract第1章 绪论1.1 引言1.2 陶瓷刀具材料简述1.2.1 陶瓷刀具材料的性能1.2.2 陶瓷刀具材料的切削加工特性1.2.3 陶瓷刀具材料的现状与发展趋势1.2.4 试验所用陶瓷刀具材料增韧机理1.3. 切削加工性能概述1.3.1 工件表面粗糙度研究进展1.3.2 刀具磨损与寿命的研究进展1.3.3 铣削力的研究进展1.4 本课题研究的主要内容第2章 陶瓷刀具铣削力的研究2.1 铣削力试验2.1.1 工件基本概述2.1.2 刀具基本概述2.1.3 其他试验条件2.2 单齿面铣刀铣削力模型的建立2.3 单因素试验及结果分析2.4 正交试验及结果分析2.4.1 多元回归数学模型2.4.2 铣削力模型系数的确定2.4.3 切削力模型显著性检验2.5 本章小结第3章 工件表面粗糙度的研究3.1 表面粗糙度成型机理3.1.1 表面粗糙度几何模型3.1.2 弹塑性变形模型3.1.3 综合几何变形和弹塑性变形3.2 单因素试验及结果分析3.3 正交试验及结果分析3.3.1 表面粗糙度经验模型的建立3.3.2 参数的最小二乘估计3.3.3 工件表面粗糙度预测模型的显著性检验3.3.4 回归系数显著性检验3.4 本章小结第4章 陶瓷刀具磨损与破损机理的研究4.1 刀具磨损概述4.1.1 刀具磨损的形式4.1.2 陶瓷刀具磨损的过程4.1.3 陶瓷刀具磨损的原因4.2 刀具破损概述4.2.1 陶瓷刀具破损的形式4.2.2 刀具破损的原因4.2.3 减少破损应该注意的事项4.3 陶瓷刀具断续切削试验研究4.3.1 试验条件4.3.2 刀具磨损与破损检测的方法4.4 本章小结第5章 金属切削有限元仿真5.1 概述5.2 陶瓷刀具铣削35CrMo过程前处理5.2.1 三维几何模型简化5.2.2 刀具材料模型的确定5.2.3 网格划分5.2.4 初始条件5.3 陶瓷刀具铣削模拟结果与试验对比5.3.1 铣削力模拟结果与试验对比5.3.2 切屑的仿真与试验对比5.4 本章小结第6章 结论与展望6.1 结论6.2 展望参考文献致谢
相关论文文献
标签:陶瓷刀具论文; 铣削加工论文; 铣削力论文; 工件表面粗糙度论文; 刀具磨损论文;
Al2O3/Ti(CN)复合陶瓷刀具铣削性能的研究
下载Doc文档