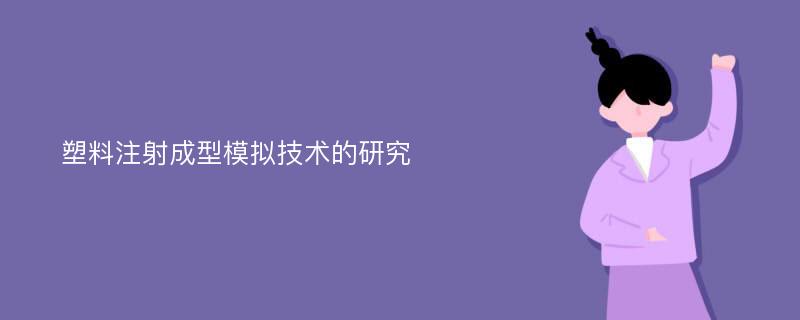
论文摘要
20世纪70年代,在世界范围内开始了注塑成型数值模拟技术的研究。到目前为止,成熟的商业注塑成型数值模拟软件较多,澳大利亚MOLDFLOW公司的Moldflow软件和美国AC-Tech公司的C-Mold软件是其中的优秀代表。本文以注塑成型CAE软件Moldflow中的MPI模块为工作平台,结合Pro/E软件,进行其应用研究。通过对打印机喷头注塑件成型的流动模拟分析,对注塑件的浇注系统、注塑工艺参数等各方面进行优化,取得比较满意的优化结果,得出一些切实可行的解决方案。本文是基于表面模型的流动分析,通过引入表面模型取代传统的“中面”模型,在简要介绍注塑成型模拟技术的发展概况之后,主要对注塑成型CAE如下几个方面进行了详细的研究:①基于模具设计的基础理论,对CAE分析的一般步骤作了简要的介绍,探讨了注塑成型过程中经常出现的缺陷和解决方法;②给出了描述塑料熔体充填流动的数学模型,主要包括型腔内流动数学模型以及浇注系统的控制方程,并假设流动模拟的边界条件;③利用MPI模块对该注塑件进行了最佳浇口位置、充填等方面分析,提出了对欠注、熔接痕等缺陷的改进措施,并结合实际情况改进了浇口的位置和数量;④完成了流动、保压、翘曲过程的分析模拟,利用正交实验方法对翘曲变形量进行了优化计算,并结合单因素翘曲量分析最终得到了最优工艺参数;⑤利用Pro/e等工具对该模具进行了设计,并将模拟结果和实际工艺参数进行对比,验证流动模拟的正确性和有效性。
论文目录
摘要ABSTRACT1 概论1.1 引言1.2 注塑成型模拟(CAE)概况和发展现状1.2.1 注射成型CAE 概况1.2.2 Moldflow 软件简介1.2.3 注射成型模拟发展现状1.3 本文研究的目的和意义1.4 本文研究的内容2 注射成型中常见的缺陷及解决方案2.1 注塑制品几种常见的缺陷2.2 欠注2.3 气穴2.4 熔接痕2.5 翘曲2.6 本章小结3 Moldflow 设计原理及塑料制件的 CAD 模型设计3.1 注射成型原理3.1.1 注射成型工艺条件3.1.2 注射成型过程3.2 打印机喷头架流动分析的一般步骤3.3 注塑过程的数字描述3.3.1 型腔内流动数学模型3.3.2 浇注系统的控制方程3.4 注塑制件的CAD 模型设计3.4.1 注塑模CAD/CAE/CAM 系统组成3.4.2 塑件的几何形状与测绘3.5 本章小结4 塑料制件的CAE 分析4.1 CAD 模型的导入及有限元网格的划分4.1.1 CAD 模型格式的转换4.1.2 项目创建及模型的导入4.1.3 模型网格划分及修改4.2 最佳浇口位置的分析4.2.1 浇口的设计原则4.2.2 浇口的选择4.2.3 材料的选择4.2.4 工艺过程参数的设定4.2.5 最佳浇口位置的分析计算4.3 填充分析及结果阐述4.3.1 填充分析结果4.3.2 修改参数后分析结果的阐述4.3.3 增加加热系统后的分析4.4 制品翘曲变形正交实验的研究4.4.1 正交实验原理4.4.2 实验设计变量及其取值范围的确定4.4.3 正交实验方案的设计及模拟实验4.4.4 工艺参数对翘曲量的影响分析4.4.5 单个因素的影响的试验4.5 本章小结5 打印机喷头座的模具设计5.1 浇注系统的设计5.2 模具结构的确定5.2.1 模具结构方案的确定5.2.2 脱模机构的设计5.2.3 抽芯机构的设计5.2.4 温度调节系统的设计5.3 模具的装配及实际效果5.4 本章小结6 论文总结及今后的工作6.1 主要结论6.2 后续研究工作的展望致谢参考文献附录
相关论文文献
标签:注塑成型论文; 分析论文; 正交实验论文; 工艺参数论文;