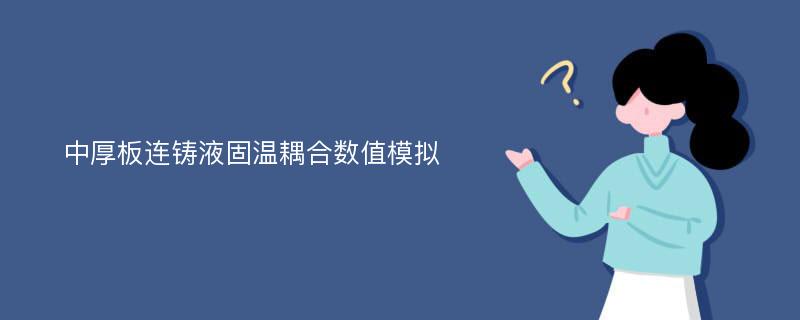
论文摘要
连铸结晶器是连铸设备中的关键部件,被称为连铸机的“心脏”,是连铸坯大多数表面缺陷和内部质量问题的发源地。而连铸过程是一个同时包含凝固、传热、流体流动等涉及到高温和复杂的物理化学现象的综合过程,到目前为止尚无有效手段进行精确地现场动态测试。因此,对连铸过程进行数学模拟就成为预测连铸相关现象、优化连铸生产工艺的有效手段。以唐山中厚板材有限公司连铸工艺和结晶器参数为研究对象,对中厚板结晶器内钢液流动、液面波动和钢水凝固状况等复杂物理现象进行研究,1)利用ANSYS软件提供的六种湍流数值模型,建立流场-温度场耦合模型;2)采用水模型试验对流场进行验证,从而提高模拟的准确性和可靠性;3)利用优化耦合模型,研究连铸和水口工艺参数对中厚板结晶器内钢液行为的影响规律,给出中厚板连铸工艺参数和水口优化工艺参数。研究结果:利用ANSYS软件建立了流场-温度场耦合数学模型,该模型的模拟结果与水模模型试验结果一致。水口浸入深度、拉速、水口出口倾角对流场和温度场有很大影响。随着水口浸入深度的增加,钢液下部回流增强,对结晶器内的下部坯壳冲刷严重,造成坯壳厚度不均,同时结晶器上部液面稳定,不利于保护渣熔化。拉速越大,液面湍动能相应增加,不利于夹杂物上浮和坯壳的形成。水口倾角过大,对初生坯壳的生长不利,水口倾角太小会减缓结晶器上部钢液的流动,造成保护渣熔化不良。合理的中厚板连铸工艺参数:水口浸入深度取0.1400.150m;拉速取1.201.40m/min;水口出口倾角取10°15°。
论文目录
摘要Abstract引言1 文献综述1.1 中厚钢板生产的发展概况1.1.1 世界中厚板生产技术的发展1.1.2 我国中厚钢板生产的发展1.2 连铸技术概述1.3 连铸过程研究中应用的模拟技术1.4 结晶器在连铸生产过程中的作用和要求1.4.1 结晶器在连铸生产过程中的作用1.4.2 结晶器在连铸生产过程中的要求1.5 连铸结晶器内钢液流场分析1.5.1 结晶器内流场的特点1.5.2 结晶器内流场数值模拟的研究现状1.6 结晶器内钢液传热行为及其影响因素的研究1.6.1 结晶器传热的特点1.6.2 结晶器内温度场和凝固壳数值模拟的研究现状1.7 课题背景及研究内容2 中厚板结晶器内钢液行为数学模型的建立和求解2.1 中厚板结晶器内钢液流场数学模型描述2.1.1 中厚板结晶器流动现象分析2.1.2 中厚板结晶器内钢液流动的基本状况与模型的基本要求2.1.3 中厚板结晶器内流场的假设及其依据2.1.4 控制方程2.1.5 多孔介质运动源项的处理2.2 中厚板结晶器内钢液传热现象分析2.2.1 中厚板结晶器内坯壳形成2.2.2 中厚板结晶器的传热机理2.2.3 控制方程2.2.4 传热参数的处理2.3 ANSYS 软件中的FLOTRAN CFD 简介2.4 数学模拟过程与结果验证2.4.1 基本假设2.4.2 模型求解参数2.4.3 求解区域和边界条件2.4.4 模型的求解结果3 中厚板结晶器内流场模拟结果验证3.1 中厚板结晶器水模型的实验设备3.2 实验流量计算3.3 结晶器内流体的流场3.4 小结4 中厚板结晶器内流场和温度场数学模拟结果分析4.1 数学模拟方案制定4.2 流场和温度场的影响因素4.2.1 水口浸入深度对流场、温度场的影响4.2.2 拉速对流场、温度场的影响4.2.3 水口出口倾角对流场、温度场的影响结论参考文献致谢导师简介作者简介学位论文数据集
相关论文文献
标签:中厚板论文; 结晶器论文; 数值模拟论文; 流场论文; 温度场论文;