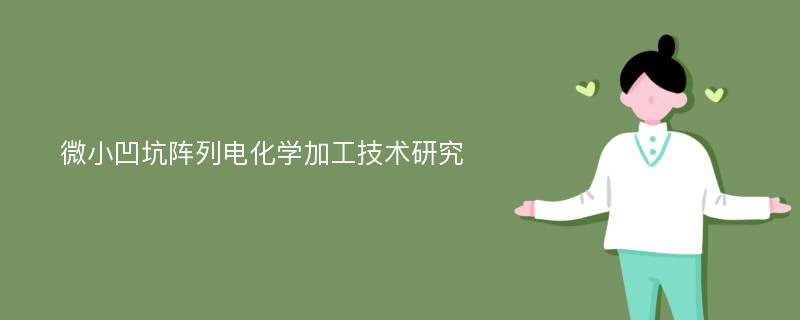
论文摘要
研究表明,微小凹坑阵列结构对于改善摩擦副表面的润滑状况,减少摩擦磨损起着非常重要的作用。因此,微小凹坑阵列结构的加工已成为研究热点。在所有微坑加工方法中,电解加工(Electrochemical Machining, ECM)具有加工效率高,成本低,无需二次加工等优点,吸引了很多研究人员的关注。电解加工是利用金属在电解液中可以发生阳极溶解的原理,将工件加工成形的一种技术。由于电解加工中,阴极和工件是非接触进行加工的,无应力变形,另外材料的减少过程以离子的形式进行,因此这种微溶解去除方式使得电解加工技术在微细制造领域有着很大的发展潜力。本文进行了电解加工微小凹坑阵列结构的研究,论文完成的主要工作如下:(1)通过有限元分析了毛细管电极电液束加工微小凹坑中工件表面被加工区域的电流密度的分布情况,结果表明,该方法适合半球形微小凹坑的加工。(2)搭建出毛细管电液束加工微小凹坑的加工系统,开展了毛细管电极电液束加工微小凹坑的试验,研究了电流密度、电解液压力和加工间隙对单个凹坑形状的影响,以及毛细管间距、电解液压力和加工间隙对凹坑阵列形状的影响。(3)提出了电解转印加工微小凹坑阵列结构的方法。利用有限元分析了不同阴极类型、不同阴极胶膜厚度以及不同阴极小孔间距对凹坑阵列形状的影响。(4)研究了脉冲频率、占空比、阴极胶膜厚度和阴极平板小孔间距对电解转印加工微小凹坑阵列形状的影响。结果表明脉冲频率越高,凹坑尺寸越小;占空比越大,凹坑尺寸越大。当光刻胶膜厚度为60μm时,所加工凹坑形状好,尺寸也较小。(5)当采用1kHz脉冲频率,0.1占空比,58A/cm2平均电流密度,60μm阴极光刻胶膜厚度的经过优化的加工参数进行加工时,获得了直径为200μm,深度10μm的凹坑阵列,凹坑阵列尺寸均匀,无翻边和毛刺。
论文目录
摘要Abstract第一章 绪论1.1 课题背景1.2 微小凹坑阵列加工技术的发展现状1.2.1 自激振动加工方法1.2.2 激光珩磨方法1.2.3 电火花加工方法1.2.4 超声冲击加工方法1.2.5 机械冲击加工方法1.2.6 低频振动刮削方法1.3 课题的研究意义及主要内容1.3.1 课题的研究目的及意义1.3.2 本文研究的主要内容第二章 电解加工理论基础2.1 电解加工的基本原理和特点2.1.1 电解加工的基本原理2.1.2 法拉第定律2.1.3 电解加工的特点2.2 电解加工基本理论2.2.1 阳极极化2.2.2 电解加工间隙的电场特性2.3 照相电解加工2.4 电液束加工第三章 毛细管电极电液束加工微小凹坑的试验研究3.1 毛细管电极简介3.2 毛细管电极电液束加工微小凹坑的机理分析3.2.1 试验原理3.2.2 电场分析3.3 毛细管电极电液束加工系统的建立3.3.1 微细电解加工机床3.3.2 电解液循环系统3.2.3 毛细管电极夹具头的设计及装夹方式的选择3.2.4 毛细管电液束加工对刀系统的设计3.3 毛细管电极电液束加工微小凹坑试验及分析3.3.1 电流密度对凹坑的影响3.3.1.1 电流密度对凹坑直径的影响3.3.1.2 电流密度对凹坑表面质量的影响3.3.2 电解液压力对凹坑形状的影响3.3.3 加工间隙对凹坑形状的影响3.4 毛细管阵列电极加工凹坑阵列结构的试验及分析3.4.1 阵列电极装夹系统的构建3.4.2 电液束加工凹坑阵列结构试验及分析3.4.2.1 毛细管间距对凹坑阵列形状的影响3.4.2.2 电解液压力对凹坑形状的影响3.4.2.3 加工间隙对凹坑形状的影响3.4.3 毛细管阵列电极电液束加工凹坑阵列结构3.5 本章小结第四章 电解转印法加工微小凹坑阵列结构试验研究4.1 电解转印法基本原理4.2 电解转印法加工微小凹坑阵列结构的电场分析4.2.1 阴极平板不同胶膜厚度有限元电场分析4.2.2 阴极平板小孔间距对凹坑阵列影响的有限元电场分析4.3 电解转印法阴极平板的制作4.3.1 基片前处理4.3.2 光刻4.4 电解转印法加工系统的建立4.4.1 供电系统及控制系统的建立4.4.2 夹具的设计和制作4.4.3 电解液循环系统的建立4.4.4 检测系统4.5 电解转印法加工微小凹坑阵列试验及分析4.5.1 脉冲电源频率对加工结果的影响4.5.2 脉冲占空比对加工结果的影响4.5.3 阴极胶膜厚度对加工结果的影响4.5.4 阴极平板小孔间距对凹坑阵列的影响4.6 本章小结第五章 总结与展望5.1 本文的主要结论5.2 对本课题研究的展望参考文献致谢在学期间的研究成果及发表的学术论文
相关论文文献
标签:微小凹坑论文; 电解加工论文; 电液束论文; 电解转印论文; 有限元论文; 光刻论文;