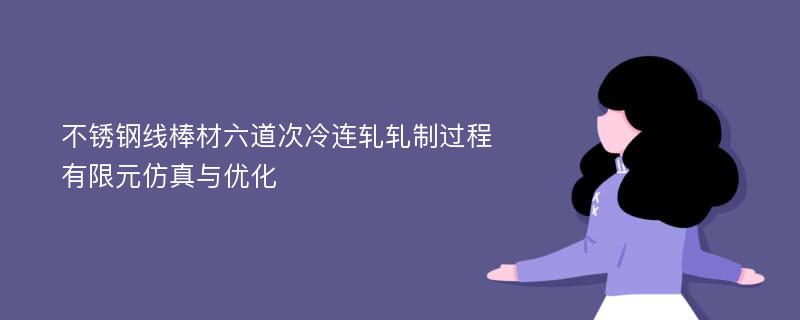
论文摘要
随着计算机技术的迅速发展和市场竞争的日益激烈,人们对线棒材尺寸精度、力学性能、产品质量、生产成本以及开发周期要求的不断提高,应用计算机仿真技术模拟线棒材连轧的全过程,预报产品的可制造性及产品精度已成为钢铁产业增强自身市场竞争力的必需手段。在采用先进设计方法的基础上,我们可以不断优化孔型设计参数,通过计算机模拟结果来指导线棒材的生产,进而减少因设计不合理以及试生产造成的浪费,达到增强企业竞争力的目的。对于不锈钢线棒材轧制过程理论研究,目前所见的文献不多,对于冷连轧过程的数值模拟则更少。本文是以大山公司棒线材冷连轧生产线的现有装备水平为研究基础,依据原材料及最终产品形状尺寸要求,采用两种设计方案,对原有的六道次冷连轧孔型进行了优化设计,在保证产品质量的前提下减少过渡孔型个数,从而减少轧制道次,达到节约能源的目的。并使用ANSYS/LS-DYNA有限元软件对该线棒材连轧变形过程进行显式动力弹塑性有限元数值模拟,探讨不同孔型参数下所对应的各道次变形过程中金属流动规律、宽展变化、轧制力曲线及等效应力、应变分布等的变化,通过与原有孔型下轧制结果进行对比,最终确定了适用孔型。模拟宽展与实际宽展吻合较好。表明这一工作具有一定的理论价值和实际意义,为企业应用更低的成本生产更高质量的产品提供了参考依据。
论文目录
摘要ABSTRACT第一章 绪论1.1 引言1.2 研究背景及意义1.2.1 课题的背景1.2.2 课题的意义1.3 研究目标及内容1.3.1 研究目标1.3.2 技术路线1.3.3 研究方案1.3.4 研究内容1.4 研究难点1.5 本章小结第二章 文献综述2.1 引言2.2 不锈钢简介2.2.1 不锈钢的定义与分类2.2.2 不锈钢的应用与发展2.3 国内外关于轧制过程数值模拟的研究现状2.3.1 板带、型材的轧制模拟研究2.3.1.1 采用有限差分法(FDM)模拟2.3.1.2 采用刚塑性有限元法模拟2.3.1.3 采用弹塑性有限无法模拟2.3.1.4 采用显式动力学弹塑性有限元法模拟2.3.2 棒线材轧制过程的有限元模拟2.4 孔型设计的基本原则2.4.1 连轧机的孔型设计2.4.1.1 连续轧制的基本概念2.4.1.2 连轧孔型设计原则2.4.2 孔型设计方法2.5 数学模型的建立2.5.1 宽展模型的建立2.5.1.1 宽展的分类2.5.1.2 宽展变形的理论分析2.5.1.3 宽展模型2.5.2 轧制压力的数学模型的建立2.6 有限元分析方法2.6.1 有限元概念2.6.1.1 刚塑性有限元法2.6.1.2 弹塑性有限元法2.6.2 弹塑性有限元法中显式动力学与隐式静力学的差别2.6.2.1 静力学与动力学的理论及其积分方法的差别2.6.2.2 隐式静力和显式动力弹塑性有限元的计算比较2.7 本章小结第三章 有限元软件简介及"方案一"中有限元模型的建立3.1 引言3.2 ANSYS及ANSYS/LS-DYNA软件简介3.2.1 ANSYS软件基本功能3.2.2 ANSYS软件的特点3.2.3 ANSYS/LS-DYNA软件及其功能3.2.4 ANSYS/LS-DYNA分析的单元类型3.2.5 质量缩放3.3 孔型优化设计3.4 有限元模型的建立3.4.1 坯料、轧辊的材质及材料属性定义3.4.2 建模过程及网格划分3.4.2.1 建模方式的选择3.4.2.2 网格划分3.4.3 加载及约束添加3.4.3.1 加载3.4.3.2 添加约束3.4.4 轧件与轧辊运动速度的确定3.5 本章小结第四章 K1′、K2′孔型下线棒材轧制过程的有限元仿真4.1 引言4.2 K1′孔型轧制模拟结果分析4.2.1 不同阶段的轧件变形分析4.2.2 K1′孔型下轧件横截面变形分析4.2.3 K1′孔型轧制后轧件横截面各向应力应变分析4.2.4 孔型圆弧半径对轧件横截面应力应变及宽展的影响4.2.4.1 不同孔型圆弧半径下轧件横截面应力应变分析4.2.4.2 不同孔型圆弧半径对轧件宽展的影响4.2.5 孔型高度对轧件横截面应力应变及宽展的影响4.2.5.1 不同孔型高度下轧件横截面变形分析4.2.5.2 不同孔型高度下轧件横截面应力应变分析4.2.5.3 不同孔型高度对轧件宽展的影响4.3 K2′孔型轧制模拟结果分析4.3.1 轧件在轧制过程中的变形情况4.3.2 K2′孔型下轧件横截面变形分析4.3.3 K2′孔型轧制后轧件横截面各向应力应变分析4.3.4 孔型圆弧半径对轧件横截面应力应变及宽展的影响4.3.4.1 不同孔型圆弧半径下轧件横截面应力应变分析4.3.4.2 不同孔型圆弧半径对轧件宽展的影响4.3.5 孔型高度对轧件应力应变及宽展的影响4.3.5.1 不同孔型高度下轧件横截面变形分析4.3.5.2 不同孔型高度下轧件横截面应力应变分析4.3.5.3 不同孔型高度对轧件宽展的影响4.4 最优孔型的确定4.5 本章小结第五章 优化后孔型设计的可行性分析5.1 引言5.2 模拟结果分析比较5.2.1 五道次孔型轧制的完整轧件变形分析5.2.2 轧制过程中轧件宽向和高向位移曲线比较5.2.3 轧件横截面等效应力比较5.2.4 轧件横截面等效应变比较5.2.5 各道次轧制力比较5.2.6 各道次孔型轧制的残余应力分析5.3 本章小结第六章 采用"方案二"进行的连轧有限元仿真6.1 引言6.2 新孔型设计思路6.3 模拟条件及有限元模型6.4 模拟结果分析6.4.1 各道次变形结果分析6.4.2 各道次等效应力分析6.4.3 各道次等效应变分析6.4.4 各道次残余应力分析6.4.5 各道次宽向及高向位移分析6.4.6 各道次轧制力分析6.5 本章小结第七章 结论与展望7.1 结论7.2 展望参考文献致谢学位论文评阅及答辩情况表
相关论文文献
标签:有限元模拟论文; 孔型优化论文; 不锈钢线棒材论文; 冷连轧论文;