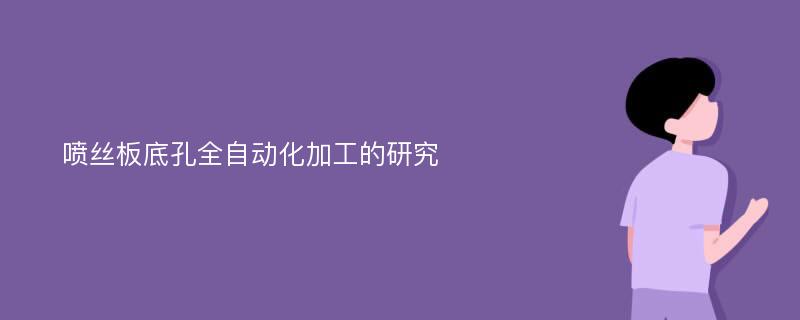
论文摘要
喷丝板作为制造化学纤维的重要装备——纺丝机的核心高精密度零件,其高精度是保证纤维成品质量及良好纺丝工艺的关键因素。喷丝板底孔的孔型、结构和精度都将直接影响到成形纤维的性能。喷丝板属于精密产品,各道工序的精度要求都很高,其中的孔道加工属于典型的大深径比微小孔加工,孔道加工时间占整个喷丝板加工时间的80%。底孔的加工质量和时间直接影响整个喷丝板的加工时间和后续纤维成形的质量。国内喷丝板制造厂通常采用人工方法对底孔进行加工,即先用麻花钻进行粗加工,再用扁钻进行铰孔底的工艺。在现有的喷丝板底孔加工工艺中,不可避免的将出现刀具和孔底不对心、刀具磨损、断刀、钻屑堆积等问题,稍有疏忽,即会造成整板报废。因此,要实现底孔的自动化加工,必须针对加工过程中的刀具、切削工艺、自动监测等问题进行研究,开发出集刀具监测、磨损检测、排屑等功能于一体的底孔自动化加工装备和工艺。本文首先介绍了国内外喷丝板加工的现状与发展,分析了国内外底孔加工存在的问题,底孔的尺寸精度要求和加工工艺过程等。国外基本上实现数控加工,国内则依靠传统手工加工,在加工过程中会出现刀具折断、留底厚不统一和效率低下等问题。其次在底孔全自动化加工装备等方面,针对微小盲孔难排屑、刀具磨损补偿及扁钻容易折断等难题,提出主轴中空数控走位清屑、使用对刀仪实现刀具磨损补偿及刀具在线折断检测等特殊功能,在原有加工中心的基础上增加自动化加工所需的相关辅助功能。在喷丝板底孔的全自动加工方面,由于传统手工刀具的工艺并不适应本自动化加工系统,因此需要对刀具和工艺进行优化。本课题重点研究了精钻全自动加工相应的切削参数及针对微小钻头刚性的问题,提出采用数控程序暂停的方法保证统一留底厚。扁钻是底孔加工中最重要的刀具,本课题针对底孔角度对纺丝的影响,设计了不同角度的扁钻进行孔底加工,并通过试验得出相应的最优切削参数,针对扁钻尖部易折断等问题,提出采用尖部倒角优化的方法进行优化,并针对实际加工中出现的各类问题进行分析总结,通过对各影响因素的合理调节,在国内首次实现了喷丝板底孔的全自动加工,加工出的底孔光洁度可达1.6,留底厚精度保证在±0.01mm。最后,在上述研究的基础上,针对加工过程进行优化,成功设计出了刀具在线观测系统,加工前通过采用本系统进行刀具跳动检测,提高了每把刀具加工的孔数和底孔加工的质量及效率。该产品填补了国内喷丝板加工领域的空白,目前已投入工厂生产使用。
论文目录
摘要ABSTRACT第一章 绪论1.1 课题研究背景、目的和意义1.1.1 喷丝板简介1.2 喷丝板加工技术综述1.2.1 国内外喷丝板孔道加工现状1.2.2 喷丝板孔道尺寸精度要求1.2.3 喷丝板的材质1.2.4 喷丝板的制造1.3 课题的来源及研究意义1.4 课题的难点、研究方向及实现目标1.4.1 课题的难点1.4.2 课题的研究方向1.4.3 课题的实现目标1.5 本章小结第二章 底孔全自动加工总体方案设计2.1 系统的需求分析2.1.1 可纺性2.1.2 底孔作用2.1.3 入口效应与法向压力差2.2 系统的功能设计2.2.1 盲孔清屑功能2.2.2 刀具磨损补偿2.2.3 刀具破损监测2.3 底孔自动化加工专用CNC加工中心2.3.1 CNC加工中心硬件组成2.3.2 控制系统2.4 本章小结第三章 精钻钻削加工3.1 精钻结构3.2 精钻工艺参数选择及优化3.2.1 钻削基本理论3.2.2 切削参数优化3.2.3 高速钢与硬质合金两种材料对比3.3 微细精钻刚性3.4 结构优化3.4.1 入钻阶段的力学模型3.4.2 精钻与扁钻角度配合优化3.5 本章小结第四章 扁钻钻削加工4.1 底孔加工刀具4.1.1 半圆刀4.1.2 扁钻4.1.3 扁钻的加工4.2 扁钻的有限元模拟4.2.1 刀具和工件的建模4.2.2 刀具和工件模型的网格划分4.2.3 仿真模拟参数设置4.2.4 模型的切屑分离准则4.2.5 不同刀具钻削性能对比4.3 工艺参数选择及优化4.3.1 三种不同锋角扁钻钻削工艺4.3.2 不同材质扁钻孔底加工对比4.3.3 切削液对加工影响4.4 扁钻优化及实际加工问题优化4.4.1 负前角优化4.4.2 尖部倒角优化4.4.3 工艺路线优化4.4.4 实际加工过程问题及改进4.5 本章小结第五章 刀具在线观测系统5.1 初始设计方案评价5.2 刀具在线观察系统方案设计5.2.1 机器视觉简介5.2.2 设计方案之一CCD系统5.2.3 设计方案之二USB显微镜5.2.4 两种方案对比5.3 在线观测系统的实现5.3.1 在线观测系统5.3.2 扁钻跳动测量5.3.3 改进试验效果5.4 效果比较5.5 本章小结第六章 总结与展望6.1 总结6.2 展望参考文献攻读硕士学位期间发表的学术论文致谢
相关论文文献
标签:喷丝板论文; 底孔论文; 扁钻论文; 结构优化论文; 在线观测论文;