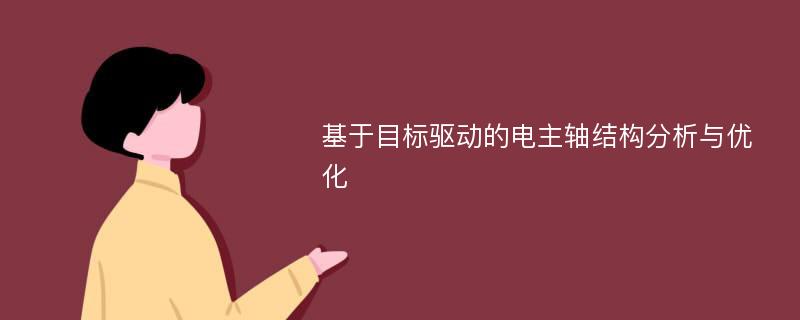
论文摘要
现代数控机床综合应用机械设计与制造工艺、计算机自动控制技术等技术领域中的最新成果,正朝着高速度、高精度、复合化、柔性化等趋势发展。机床主轴系统的静、动态特性是影响机床加工精度的主要原因之一,因此将有限元分析应用于电主轴单元的设计过程,有助于提高机床整体的效率与设计水平。本文分别应用有限元理论分析模型与模态实验测试方法对主轴系统的动静态特性进行分析,并确定优化目标,在目标驱动下对电主轴动态性能进行优化,具体工作包括:(1)根据本主轴系统所用轴承型号,对主轴轴承的刚度和阻尼进行了理论计算,分析了轴承预紧力与轴承刚度的关系,得出角接触球轴承的刚度随预紧力变化的规律。(2)对电主轴进行了有限元建模,在Femap+NX Nastran中,用梁单元模拟主轴,对其进行静力学分析,得到主轴的静刚度。(3)应用Matlab软件,对主轴进行动态特性分析,求得电主轴前四阶模态频率以及其相对应的振型,进一步对主轴模型进行谐响应分析,得到主轴前端、中部和后端的响应曲线。总结了主轴响应幅值与固有频率及振型的关系。(4)应用LMS测试系统对电主轴有限元模型进行验证实验,实验结果表明,电主轴谐响应曲线变化趋势基本与测试结果相符,理论模型仿真与实验测试所得的前三阶固有频率值误差都在9%以内,证明有限元建模基本正确。(5)计算电主轴系统的临界转速,在原有的动力学模型中添加了主轴因高速而产生的离心力和陀螺力矩,分析了离心力与陀螺力矩对主轴临界转速求解的影响,总结出固有频率随主轴转速变化的规律。(6)利用偏心质量对主轴产生的影响,计算主轴系统的动刚度在各个转速下对应的动刚度值,并总结出主轴动刚度随转速变化的规律。(7)对主轴进行优化设计,建立主轴系统的参数化有限元模型,从主轴应用的实际角度出发,以主轴动刚度为优化目标,并以此目标为驱动,优化主轴各阶梯段的长度、外圆半径、悬伸量以及轴承跨距等结构参数,对主轴系统进行优化设计,使主轴系统在质量减轻的情况下,具有更好的的动态性能。
论文目录
摘要Abstract第一章 绪论1.1 电主轴系统概述1.2 电主轴系统性能评价与研究方法1.2.1 电主轴系统性能的评价1.2.2 电主轴系统性能的研究方法1.3 课题研究背景及意义1.4 课题研究内容与章节安排第二章 电主轴主要结构设计参数2.1 电主轴轴承的设计2.2 电主轴润滑系统设计2.3 电主轴冷却系统设计2.4 电主轴驱动系统设计2.5 主轴的跨距设计2.6 主轴的过盈设计2.7 本文所用电主轴结构设计参数2.8 本章小结第三章 电主轴静态特性的研究3.1 电主轴静态特性3.2 角接触球轴承的研究3.2.1 Hertz接触理论3.2.2 角接触球轴承预紧力与位移3.2.3 角接触球刚度计算3.2.4 角接触球轴承阻尼计算3.3 电主轴刚度有限元分析3.3.1 分析软件介绍3.3.2 构建几何模型3.3.3 网格划分与单元选用3.3.4 计算电主轴静刚度3.4 本章小结第四章 电主轴动态特性的研究4.1 结构动力学基本理论4.1.1 模态分析理论4.1.2 谐响应分析理论4.2 动力学理论仿真研究方法4.2.1 动力学理论仿真研究的基本步骤4.2.2 用于电主轴动力学建模的软件简介4.2.3 电主轴动力分析通用软件开发4.3 电主轴动力学建模4.3.1 简化模型4.3.2 划分网格4.3.3 设置模型边界条件4.4 电主轴模态分析4.4.1 固有频率与振型仿真实验4.4.2 临界转速的计算4.5 谐响应分析4.5.1 电主轴谐响应分析4.5.2 电主轴动刚度计算4.6 电主轴动力学模型实验验证4.6.1 模态测试技术概述4.6.2 电主轴模态测试实验4.7 本章小结第五章 目标驱动的电主轴结构优化设计5.1 优化设计概述5.2 确立驱动目标5.2.1 电主轴常用工作转速5.2.2 电主轴不平衡质量的确定5.2.3 电主轴驱动目标5.3 优化变量的选择5.4 基于目标驱动的电主轴动态特性优化5.4.1 电主轴悬伸量的优化设计5.4.2 电主轴跨距的优化设计5.5 本章小结总结与展望参考文献攻读硕士学位期间发表论文致谢
相关论文文献
标签:电主轴论文; 静态特性论文; 动态特性论文; 优化设计论文; 有限元论文;