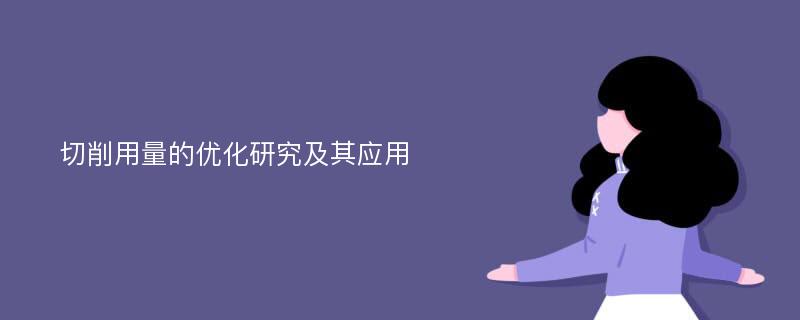
论文摘要
在机械产品中,绝大多数零部件是通过切削加工实现的,而在切削加工系统中,切削用量的合理选择将直接影响产品的质量、生产周期、生产成本,以及整个生产系统的经济效益等。因此,随着市场竞争的日益激烈,运用科学合理的手段选择切削用量的最优组合已势在必行。本文以地铁DZ44型转向架轴箱的机加工工序所涉及到的切削方式为研究对象,针对切削用量的优化选择问题,采用最大生产效率为主优化目标、最低生产成本为次优化目标的多目标优化准则,在通过对机加工工艺中单工序单工步和多工序单工步制造系统切削用量优化目标数学模型的建立方法进行全面研究的基础上,建立多工序制造系统切削用量的优化目标数学模型和约束条件方程。根据切削用量的优化模型,通过对最优化技术进行研究,本文分别运用数值优化技术和非数值优化技术(遗传算法)实现多工序制造系统切削用量二因素(切削速度和进给量)的优化组合。切削用量优化的相关成果正在逐步应用于实际生产中,使企业能够根据市场的需求快速做出生产决策,并为企业的自动化生产奠定了基础,对企业追求经济效益的最大化有着指导意义。本文的主要研究工作可总结如下:1.运用数值优化技术实现了对多工序单工步制造系统切削速度的无约束优化,给出了不同优化准则下关键工序的确定方法,以及松弛工序的最佳切削速度选择准则。2.建立了符合生产实际的多工序多工步制造系统切削用量优化的目标数学函数模型和相应生产条件下的约束方程,并给出了基于多目标优化准则下切削用量的数值解析优化方法。3.通过对现代智能优化技术的研究,给出了多工序多工步制造系统切削用量优化组合的非数值优化—遗传算法的实现方法。4.结合轴箱部分机加工工序的工艺信息,运用C#程序设计语言,编写了基于数值优化技术和非数值优化技术—遗传算法的切削用量优化程序,实现了对多工序制造系统切削用量的有约束优化组合。5.运用均匀设计实现了钻削工序最优切削用量的验证性试验方案设计,并通过对试验数据进行直观分析,从而验证了切削用量优化思想的正确性。
论文目录
摘要Abstract第一章 绪论1.1 课题的来源及背景1.2 国内外的研究现状及存在的问题1.3 课题的研究内容和意义1.3.1 课题研究的意义1.3.2 课题研究的主要内容第二章 切削用量的优化选择方法及其评价2.1 以试验为主的传统优化方法2.1.1 查表法2.1.2 经验法2.1.3 图解法2.1.4 单因素—图解法2.1.5 正交试验设计法2.1.6 回归正交设计法2.2 以数学模型为主的先进优化方法2.2.1 应用“最优切削温度守恒定律”确定最优切削用量组合2.2.2 应用最优化技术确定最优切削用量本章小结第三章 切削用量优化理论的分析验证及其实现3.1 经济生产的评价标准3.2 单工序制造系统切削速度的无约束优化3.2.1 基本的优化目标数学模型3.2.2 以切削速度为参变量的优化目标数学模型3.2.3 最优切削速度的确定3.3 多工序制造系统切削速度的无约束优化3.3.1 基本数学模型3.3.2 最优切削速度的确定3.3.3 多工序生产系统切削速度的优化实例本章小结第四章 多工序多工步制造系统切削用量的有约束优化4.1 数学模型建立4.1.1 单位生产时间4.1.2 单位生产费用4.1.3 切削用量和工步余量对生产时间影响的分析4.1.4 切削用量对刀具耐用度影响的分析4.1.5 以切削用量为参变量的优化目标制造模型4.2 目标函数的优化分析4.3 制造系统的约束条件4.3.1 工件刚度约束4.3.2 刀杆刚度与强度约束4.3.3 刀片强度约束4.3.4 机床进给机构的强度约束4.3.5 钻削时的几个特殊约束4.3.6 加工表面粗糙度约束4.3.7 机床技术参数的约束4.4 进给量的优化选择4.5 切削速度的优化选择4.5.1 机床功率对主轴转速的约束4.5.2 铣刀刀齿破损条件对切削速度的约束4.5.3 切削速度的无约束最优解4.5.4 最优主轴转速的优化选择4.6 切削用量的多目标优化分析4.6.1 工序生产时间4.6.2 生产周期时间4.6.3 切削用量的数值优化技术的实现4.6.4 切削用量的非数值优化技术—遗传算法的实现本章小结第五章 轴箱切削用量的优化及试验研究5.1 轴箱切削用量的优化实现及其分析5.1.1 轴箱机加工工艺信息5.1.2 遗传算法的实现过程5.1.3 数值与非数值优化结果的比较及其分析5.2 试验研究5.2.1 试验方案设计5.2.2 试验验证本章小结总结与展望参考文献附录A 轴箱零件图和加工工序卡片攻读硕士学位期间发表的学术论文致谢
相关论文文献
标签:切削用量论文; 多目标优化论文; 多工序制造系统论文; 遗传算法论文;