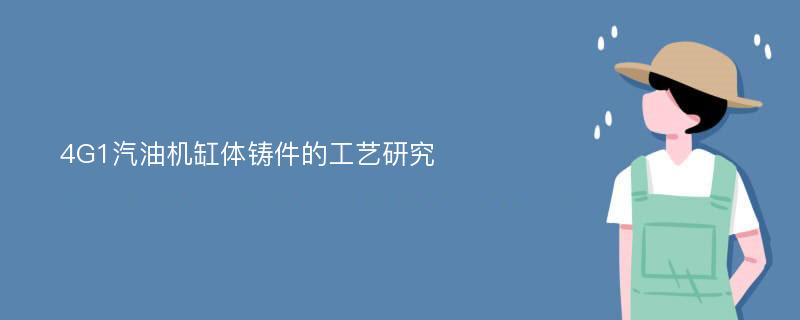
论文摘要
本文利用研制单位现有的生产设备及多年积累的成型经验,主要从铸造工艺方案优化、铸造工艺参数优化及铸造工艺难点分析三方面进行了研究。工艺优化方案主要研究铸造工艺性分析及工装设计;工艺参数优化是通过试验确定了制芯、造型、熔化等环节的主要工艺参数;铸造工艺难点分析重点研究解决研制过程中存在的铸造缺陷及金相组织等方面的问题。通过对工艺过程的研究分析表明,要利用现有设备达到工艺要求,必须采用一箱一件,冷、热芯盒共同制芯,封闭—开放式浇注系统,高温熔炼废钢增碳的铸造工艺方案。通过采用以上工艺,达到缸体硬度HB179~269,σ_b≥274MPa的技术要求,铸件本体取样分析石墨长度4级~6级,石墨类型为A型(B、D型≤20%),游离铁素体量≤3%,游离渗碳体量≤3%。根据以往的生产经验,水套芯采用热芯盒制芯,主体芯及端盖芯采用冷芯盒制芯。采用低合金化加复合孕育处理来得到满意的金相组织和机械性能。经过大量试验研究结果表明,当型砂中水分为2.7%~3.4%,有效粘土为6%~9%,全粘土为8%~12%;铁水化学成分C为3.10%~3.50%,Si为1.65%~2.50%,Cr为0.15%~0.40%,Cu为0.3%~0.6%,Sn为0.02%~0.10%时,可以得到较为满意的效果。本文还研究并解决了4G1缸体上顶面砂眼、气孔及掉砂问题,从而大幅度地提高了铸件的合格率,实现了4G1缸体国产化的生产。
论文目录
摘要Abstract第1章 绪论1.1 课题背景1.2 发动机缸体铸件的综合性能要求1.3 铸铁件在我国汽车工业中的应用1.4 铸铁件的生产现状及生产水平1.4.1 铸铁件的生产状况1.4.2 灰铸铁件生产的发展方向1.4.3 灰铸铁件生产国内外之间差距1.5 铸铁缸体的发展现状及研究重点1.5.1 铸铁缸体铸件国外发展现状1.5.2 铸铁缸体铸件国内发展现状1.5.3 铸铁缸体铸件今后研究重点1.6 本文的主要研究内容第2章 4G1缸体的铸造工艺方案优化2.1 4G1缸体铸件的铸造工艺性分析2.1.1 造型工艺方案设计2.1.2 制芯工艺方案设计2.1.3 组芯工艺方案设计2.1.4 浇注系统工艺方案设计2.1.5 铁水熔炼工艺方案设计2.1.6 缸体铸件喷漆工艺方案设计2.2 工装的设计2.2.1 芯盒设计中存在问题的解决2.2.2 组芯、下芯夹具的设计2.3 本章小结第3章 缸体铸件铸造工艺参数优化3.1 制芯工艺参数的选择3.1.1 覆膜砂种类的选择3.1.2 涂料、烘烤及涂料配比3.2 造型工艺参数的选择3.3 熔化工艺参数的选择3.3.1 4G1缸体的化学成分3.3.2 孕育剂的选择3.4 本章小结第4章 主要铸造缺陷分析及解决4.1 上端面气孔砂眼问题的解决4.2 冷、热芯盒交互使用问题的解决4.3 缸体铸件掉砂废品的控制4.3.1 控制型砂质量,减少掉砂废品4.3.2 砂芯质量的控制4.4 缸体铸件气孔缺陷的控制4.5 缸体铸件夹渣缺陷的解决4.6 本章小结结论参考文献致谢工程硕士研究生简历
相关论文文献
标签:灰铸铁论文; 缸体论文; 工艺方案论文;