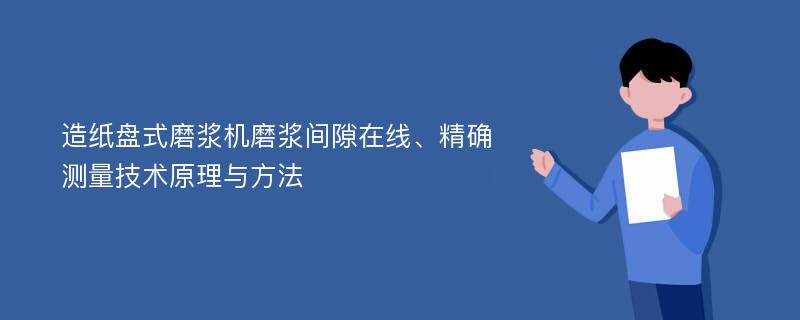
论文摘要
在打浆和高得率制浆中广泛采用的盘式磨浆机,其磨浆间隙的测量与控制一直是国内外磨浆设备的关键技术之一。然而,国内外目前采用主电机总电流即磨浆功率控制手段,实际受浆流量、浓度、杂物及盘齿磨损等因素影响使磨浆间隙测量间接且不准确,故磨浆间隙的精确、在线实时测量技术始终未获突破。它对提高磨浆纤维质量以及设备安全运行等意义重大。本文首先在研究分析出解决盘间磨浆间隙精确、在线实时测量技术需满足的关键条件;并研究筛选出可满足的传感器测量技术;进一步研究了所选择的传感器测量旋转齿盘类金属构件表面位移物理量的基本理论、方法和其输入与输出特性;研究了实际盘式磨浆机上磨浆间隙在线实时测量的安装的理论、技术与方法,各种工况下的传感器输入与输出特性;最后,研究和设计了磨浆间隙信号采集与处理过程中的标度变换与算法流程、基本程序等。本文主要获得以下成果:1、较适合于盘式磨浆机运行工况及具有磨盘磨片特征的旋转齿盘形金属构件表面位移量直接、精确测量的传感器为电涡流位移传感器。2、电涡流传感器探头引起齿盘形金属表面电涡流分布为:盘齿部分电涡流环域分布为畸形圆闭环流的组合,边界附近密度很高;齿体部分电涡流同样是以探头线圈轴为轴心对称,但分割开各自形成非圆形、边缘畸变的独立闭环流;齿槽底面以下部分,电涡流环域分布为一以探头线圈轴为轴心的整体同心圆。有效测量齿盘形金属表面微位移时,探头所覆盖齿盘面区域的电涡流特性保持固定。3、直径Φ11 mm电涡流传感器探头测量齿盘形金属表面静态或动态旋转时,与平面金属导体的电压—位移(U-X)特性曲线整体变化趋势完全一样;在X接近于0距离时输出值U“突变提升”要比平面盘提前。齿盘形金属表面变转速状态下,转速<760rpm(相当于线速172m/min)时,U在<±0.04v内波动;而当转速>760rpm时,U值稳定,且转速越高、示值越平稳;在0.60~7.20mm齿盘位移间隙测控范围内,传感器静、动态试验数据进行最佳特性曲线线性回归相关系数都大于0.999,各齿盘试件的特性曲线斜率基本相同。4、在测量齿盘形金属表面边界区位移量时,电涡流传感器输出特性存在边缘影响效应,其影响范围为探头径向端面与齿盘形金属表面边缘距离e<3mm。5、电涡流传感器探头直接且精确的实时测量盘式磨浆机磨浆间隙时,不受磨浆浆种、浓度和流量的影响;在动、定磨盘处于无浆静态、无浆动态以及有浆动态三种工况下,电涡流传感器的位移电压输入输出特性基本一致,线性好,且退盘与进盘时重现性好。6、盘式磨浆机磨浆盘间隙动态监测引起磨浆间隙变化的共有“阶段性开机前的间隙调零和取得初始间隙,启动旋转运行,进、退盘操作,停机”四种操作状态。对应于四种操作状态具有相应的间隙算法和算法程序转换流程。本课题研究,在国内外首次进行了电涡流传感器用于旋转齿盘形金属面位移测量的理论与输入、输出特性研究,并为电涡流传感器开劈了新的非接触测量位移的用途;提出了盘式磨浆机高速旋转齿盘的动态非接触式测量位移的理论与方法,以及直接、实时、精确测量与调节控制磨浆间隙的技术原理和具体实施方法,为使理论研究的磨浆工艺在磨浆机上精确实施和提高磨浆工艺技术控制水平奠定了理论基础,具有广阔的应用前景。
论文目录
致谢摘要ABSTRACT第一章 绪论1.1 课题的提出及其意义1.1.1 课题提出的背景1.1.1.1 盘式磨浆机在打浆设备中地位1.1.1.2 盘式磨浆机磨浆间隙测量与调节控制现状1.1.2 课题提出的意义1.2 盘式磨浆机国内外研究进展1.2.1 盘片材料、耐用性与经济性的研究1.2.2 盘片磨浆面物理特征(形状、型式)的研究1.2.3 工况条件、产能与结构关系的研究1.2.4 工况条件的生产运行控制的研究1.2.5 磨浆能耗分布、微观磨浆机理的研究1.2.6 盘式磨浆机运行振动机理与安全受限的研究1.2.7 中、高浓磨浆和高产量的磨浆机结构的研究1.3 位移测量技术研究进展1.3.1 位移测量概述1.3.1.1 位移测量及其基本用途1.3.1.2 位移测量常用传感器1.3.2 位移测量技术现状及发展1.3.2.1 位移测量原理现状及发展1.3.2.2 位移测量用传感器现状及发展1.4 论文主要工作1.4.1 研究内容1.4.2 论文预期达到的水平和目标1.4.3 论文主要特色与创新点第二章 盘式磨浆机磨浆间隙测量方法研究2.1 磨浆间隙测量与调节方法的现状分析2.1.1 游标间隙测量与机械调节方法2.1.2 游标间隙测量与电动—机械调节调节方法2.1.3 游标尺间隙测量与液压调节方法2.2 磨浆间隙变化与测量的特点2.2.1 盘式磨浆机磨浆过程2.2.2 磨浆间隙变化与测量的特点2.3 相关位移测量技术应用于磨浆机间隙测量的研究2.3.1 接触式位移测量技术测量盘式磨浆机间隙技术研究2.3.1.1 光栅式位移传感器测量技术2.3.1.2 差动式变压器式位移传感器测量技术2.3.1.3 高精度纳米分辨率线位移测量技术2.3.2 非接触位移测量技术测量盘式磨浆机间隙技术研究2.3.2.1 光学式位移传感器测量技术2.3.2.2 电容式位移传感器测量技术2.3.2.3 霍尔式位移传感器测量技术2.3.2.4 电涡流式位移传感器测量技术2.4 实现磨浆间隙在线精确测量的要求2.5 本章小结第三章 电涡流在齿盘面分布状况研究3.1 盘式磨浆磨片结构特征3.1.1 盘式磨浆磨片结构对磨浆的影响3.1.2 盘式磨浆机磨片结构特征3.1.3 盘式磨浆机磨片材料3.1.4 盘式磨浆机磨片选择3.2 电涡流基本原理3.2.1 电涡流3.2.1.1 金属的导电性与磁特性3.2.1.2 电磁感应与涡流3.2.2 电涡流的集肤效应3.2.2.1 电涡流的集肤效应现象与概念3.2.2.2 电涡流的集肤效应的计算3.3 盘齿表面电涡流分布3.3.1 磨片盘齿表面特征3.3.2 盘齿表面电涡流分布3.3.3 测量盘齿表面位移用探头直径研究3.4 本章小结第四章 电涡流传感器对金属旋转齿盘的响应特性研究4.1 基本研究方法4.1.1 模拟实验用旋转齿盘4.1.1.1 模拟实验用旋转齿盘设计4.1.1.2 模拟实验用旋转齿盘加工4.1.2 传感器4.1.2.1 传感器参数计算4.1.2.2 传感器选用4.1.3 其它研究用手段4.2 电涡流传感器测量齿盘位移的特性的试验方案4.2.1 测量齿盘位移的特性的静态试验方案4.2.1.1 静态试验组确定4.2.1.2 静态试验装置与方法4.2.2 测量齿盘位移的特性的动态试验方案4.2.2.1 动态试验组确定4.2.2.2 动态试验装置与方法4.3 齿盘不同位移的试验结果与讨论4.3.1 静态试验结果与讨论4.3.1.1 静态试验结果4.3.1.2 无齿盘与同齿宽、同槽宽、不同齿高齿盘间的结果比较4.3.1.3 无齿盘与不同齿宽、不同槽宽、相同齿高齿盘间的结果比较4.3.2 动态试验结果与讨论4.3.2.1 动态试验结果4.3.2.2 无齿盘与同齿宽、同槽宽、不同齿高齿盘间的结果比较4.3.2.3 无齿盘与不同齿宽和槽宽、相同齿高齿盘间的结果比较4.3.2.4 变转速、变间隙下电涡流传感器输出特性4.3.3 齿盘位移的动、静态试验结果比较4.4 传感器最佳特性曲线拟合方程式4.4.1 特性曲线拟合方程式拟合方法4.4.2 静态试验最佳特性曲线拟合方程式4.4.3 动态试验最佳特性曲线拟合方程式4.5 本章小结第五章 电涡流传感器在盘式磨浆机上测量间隙技术研究5.1 实验手段与研究研究方法的确立5.1.1 研究手段5.1.1.1 研究手段说明5.1.1.2 电涡流传感器5.1.1.3 盘式磨浆机5.1.1.4 间隙监测仪5.1.1.5 数显式万用表与游标卡尺5.1.1.6 齿盘试件5.1.2 研究方法的研究5.1.2.1 传感器安装于齿盘边缘效应的研究5.1.2.2 传感器安装方法的研究5.1.2.3 电涡流传感器输出特性曲线的研究5.1.2.4 传感器响应最佳特性曲线拟合方程5.2 试验结果与讨论5.2.1 电涡流传感器安装于齿盘边缘位置及边缘效应的研究5.2.1.1 探头安装于齿盘边缘效应的实验结果5.2.1.2 探头安装于实际盘片边缘的位置5.2.2 电涡流传感器响应特性的研究5.2.2.1 实验步骤5.2.2.2 静态试验电涡流传感器响应特性5.2.2.3 无浆动态试验电涡流传感器响应特性5.2.2.4 空盘静、动态试验电涡流传感器响应特性5.2.2.5 有浆动态试验电涡流传感器响应特性5.2.2.6 电涡流传感器响应最佳特性曲线拟合方程5.3 本章小结第六章 标度变换计算算法与变换程序6.1 磨浆间隙显示仪显示标度变换6.1.1 磨浆时盘片磨损状态变化与间隙算法6.1.2 显示仪显示标度变换6.2 显示间隙程序算法流程6.2.1 磨片生产过程中控制状态6.2.2 算法流程转换程序6.3 本章小结第七章 显示仪表的基本设计7.1 盘间隙显示仪相关问题7.1.1 显示参数的确定7.1.2 显示界面设计7.2 仪表主要结构原理与经济投入分析7.2.1 本技术成果主要内容7.2.2 仪表主要结构原理7.2.3 测量系统的配置7.2.4 主要功能7.2.5 测量系统的投入7.3 本章小结第八章 结论与展望8.1 本文主要结论8.2 本文的创新点8.3 展望主要参考文献附:攻读博士学位期间发表的相关学术论文与申请的发明专利详细摘要
相关论文文献
标签:盘式磨浆机论文; 磨浆间隙论文; 在线测量论文; 电涡流传感器论文; 齿盘金属面论文; 非接触位移测量论文; 边缘效应论文; 特性曲线论文;
造纸盘式磨浆机磨浆间隙在线、精确测量技术原理与方法
下载Doc文档