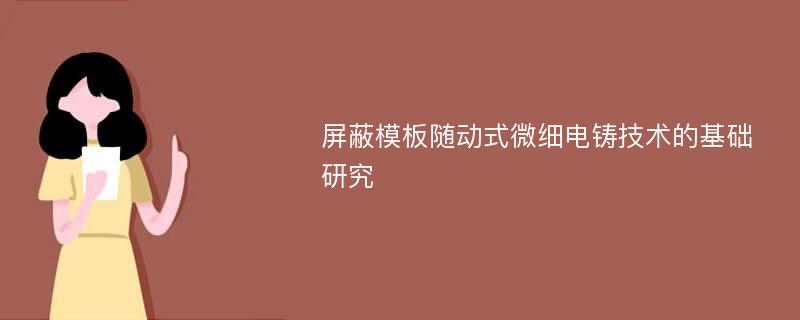
论文摘要
电铸是利用金属离子在阴极上沉积来制造金属制品的增材加工过程,其加工过程是以离子的形式进行的。由于金属离子的尺寸非常微小,小于纳米尺度,因此电铸技术相对于其它很多微加工方法在原理上具有优势,在微纳米加工领域有着很大的发展潜能。另外,电铸属非接触加工,具有无切削应力变形、无热影响区、无工具损耗、低成本、适用范围广等优点。微小尺度(Micro/Meso尺度)是高科技产品和国防产品最密切相关的尺度领域,因而相对应的Micro/Meso加工技术成为各工业发达国家广泛关注和重点投入的研究热点。本文主要针对Micro/Meso尺度金属微结构,首先提出一种实用的微细电铸成型技术,然后围绕这一新技术的开发进行研究。本文的主要内容包括以下几个方面:(1)提出屏蔽模板随动式微细电铸技术,即通过屏蔽模板随电沉积层高度的增加而微量移动,从而用厚度有限的屏蔽模板制造出原理上高度不受限制的三维金属微结构。(2)针对屏蔽模板随动式微细电铸技术的特点,建立了随动式电沉积试验系统。整个试验系统包括四个部分:加工控制系统、电解液系统、电沉积系统以及加工状态的检测与监控。该系统满足屏蔽模板随动式电铸技术的要求,实现了x-y-z三轴精密联动,加工状态的在线监控以及沉积厚度的实时检测;实现了电解液加热循环,周期更新;针对装夹中出现的屏蔽模板与阴极之间的楔形误差,设计了自找平夹具。基于LabVIEW开发的控制软件,方便实现各种随动电沉积方式,并对加工中的电信号进行实时检测,同时根据采集到的信号作出快速反应,对异常加工情况自动采取相应措施,保证加工顺利进行。(3)试验研究了基于金属基底的SU-8光刻胶紫外光刻工艺的各个环节,包括甩胶、前烘、曝光、后烘、显影等。在正交试验的基础上运用BP神经网络对试验数据进行分析处理,预测了较正交试验分析结果更为优化的工艺组合,并用试验验证了其正确性。利用优化的工艺措施,制备出了高尺寸精度、轮廓清晰、表面质量好、无明显缺陷、与基底结合力强的屏蔽阳极模板。(4)根据电场基本理论建立屏蔽阳极模板随动式微细电铸极间电场模型。基于建立的电场模型,利用有限元技术分析加工定域性,并对加工过程进行模拟。将数值分析及模拟结果用于指导试验研究。(5)开展屏蔽阳极模板随动式微细电铸关键技术研究。研究屏蔽阳极模板采用可溶与不可溶材料、磷铜与电解铜基底时对沉积结果的影响;在分析屏蔽阳极模板随动式微细电铸技术电沉积的特点及极化曲线测定的基础上,研究电流密度对沉积微结构表面质量的影响,得到电流密度的选择范围;对屏蔽阳极模板受到的化学、电化学以及机械破坏作用进行研究,提出延长屏蔽阳极使用寿命的技术措施;开展不同随动方式加工金属微结构的试验研究,成功制造了微齿轮等微金属元器件。(6)理论分析了活动模板随动式电铸过程中扩散传质及电场分布对沉积结果的影响。深入开展了活动模板随动式微细电铸技术试验研究,利用该技术成功制造了微圆柱电极阵列及微梳齿驱动器等金属元器件。本文进行的屏蔽模板随动式微细电铸技术研究,是特种微细加工技术的拓展,将其应用于金属微结构器件的制作,必将对微机电系统的进一步发展起到有力的推动作用。
论文目录
摘要Abstract图表索引符号索引第一章 绪论1.1 微机电系统与微细加工1.2 金属材料微细加工的种类及发展1.2.1 LIGA 及LIGA-like 技术1.2.2 EFAB 技术1.2.3 局部电化学沉积技术1.2.4 基于STM 的微细电化学加工1.2.5 微细电火花加工1.2.6 微细电解加工1.2.7 其它加工方法1.3 微细电铸技术研究与发展1.4 本文研究的意义及主要研究内容1.4.1 研究意义1.4.2 主要研究内容第二章 屏蔽模板随动式微细电铸技术方案2.1 电铸基本理论2.2 屏蔽模板随动式电铸方案2.2.1 屏蔽阳极模板随动式微细电铸方案2.2.1.1 简单三维实体电铸方案2.2.1.2 等截面扭曲实体电铸方案2.2.2 活动模板微细电铸方案2.3 屏蔽模板随动式微细电铸技术的影响因素分析2.4 屏蔽模板随动式微细电铸技术的特点2.5 本章小结第三章 屏蔽模板随动式微细电铸试验系统3.1 随动式微细电铸试验系统总体规划3.2 屏蔽模板随动式微细电铸技术加工控制系统3.2.1 加工控制系统的硬件结构3.2.1.1 加工控制系统的硬件结构设计3.2.1.2 加工过程运动控制3.2.2 加工控制系统的软件设计3.2.2.1 LabVIEW 图形编程语言3.2.2.2 控制系统软件设计3.3 电解液系统3.4 电沉积系统3.5 加工状态的检测与监控3.5.1 沉积结果在线观测3.5.2 沉积厚度在线监测3.5.2.1 理论电沉积速率3.5.2.2 虚拟电量计3.5.3 电沉积状态的实时监控3.6 本章小结第四章 基于紫外光刻的屏蔽阳极模板制作工艺优化研究4.1 引言4.2 屏蔽阳极模板紫外光刻工艺基础研究4.2.1 SU-8 光刻胶简介4.2.2 光刻掩模板的设计4.2.3 金属基底的处理4.2.4 涂胶4.2.4.1 SU-8 胶旋转涂铺基本工艺过程4.2.4.2 光刻胶旋转涂铺厚度理论4.2.4.3 SU-8 胶旋涂试验4.2.5 前烘4.2.6 曝光4.2.7 后烘4.2.8 显影4.2.9 漂洗和干燥4.2.10 后处理4.3 光刻工艺优化试验研究4.3.1 正交试验4.3.2 基于BP 神经网络的工艺参数优化4.3.2.1 BP 神经网络的设计4.3.2.2 BP 神经网络的训练4.3.2.3 BP 神经网络对尺寸偏差的预测4.4 本章小结第五章 屏蔽阳极模板随动式微细电铸技术基础研究5.1 极间电场的数学模型5.2 基于电场的屏蔽阳极模板随动式电铸成型模拟加工5.2.1 屏蔽阳极模板随动式电铸成型理论5.2.2 基于APDL 的随动式电铸过程模拟5.2.3 模拟结果及分析5.3 电沉积定域性研究5.3.1 电沉积定域性概念5.3.2 基于电场的定域性分析5.3.3 电沉积定域性试验研究5.4 屏蔽阳极模板随动式微细电铸的基础试验研究5.4.1 电铸溶液的选择5.4.2 屏蔽阳极模板不同基底材料对电铸结果的影响5.4.2.1 不溶性阳极5.4.2.2 可溶性阳极5.4.3 屏蔽阳极模板性能试验5.4.3.1 化学腐蚀5.4.3.2 电化学腐蚀5.4.3.3 机械作用5.4.3.4 提高屏蔽阳极模板性能的措施-“预填充”防止侧向钻蚀5.4.4 电流密度的选择及其对表面形貌的影响5.4.4.1 阴极极化曲线的测定5.4.4.2 阴极电流密度对铸件表面形貌的影响5.4.4.3 “突出生长”原因理论分析5.4.5 加工实例5.5 本章小结第六章 活动屏蔽模板高深宽比微细电铸技术研究6.1 扩散传质分析6.2 电场分析6.2.1 理论模型6.2.2 有限元分析结果及讨论6.3 电铸金属微结构试验研究6.3.1 试验条件6.3.2 模板加工与处理6.3.3 单周期试验结果及讨论6.3.4 多周期高深宽比微结构加工试验结果及讨论6.3.5 后续加工处理6.4 本章小结第七章 总结与展望7.1 论文研究工作总结7.2 对未来工作的展望参考文献致谢在学期间发表的学术论文及研究成果
相关论文文献
标签:微细电铸论文; 屏蔽阳极模板论文; 活动模板论文; 微小尺度论文; 电场论文; 定域性论文;